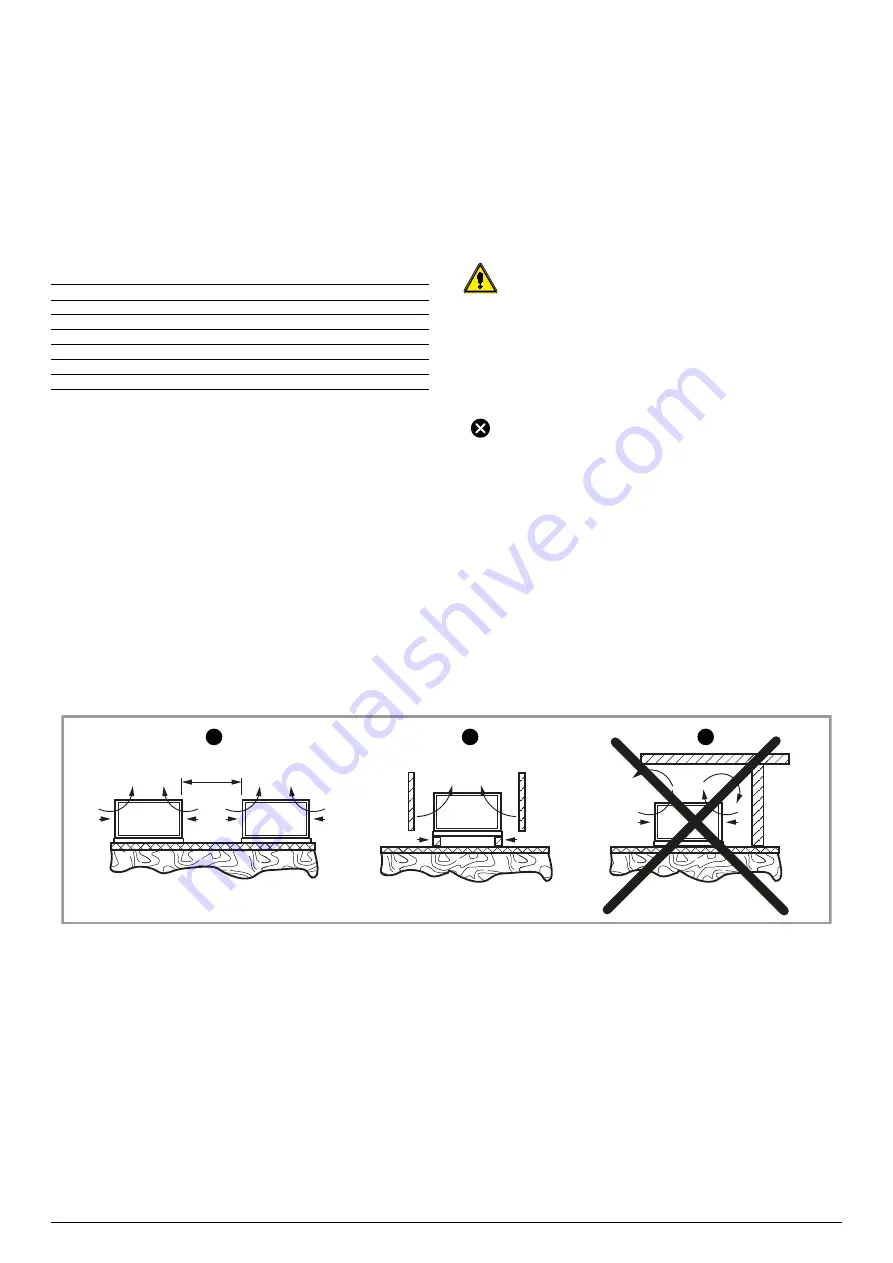
22.11 – 5167557_03
15
STORAGE
It is possible that the units may not be immediately installed upon receipt. If they
are stored for a medium-long period of time, the following procedures are recom-
mended:
— The units cannot be stacked;
— Check for any damage
— Make sure there is no water inside the hydraulic systems;
— Do not remove the protections from the heat exchanger;
— Do not remove the plastic protective films;
— Make sure that the electrical panels are closed;
— Before using the equipment, put all the supplied items in a dry and clean loca-
tion so that they can be used in the future.
The minimum and maximum unit storage temperature depends on the
type of refrigerant used, see the table. Above this limit, there is a risk of
refrigerant leaks through the pressure relief valves.
Maximum storage temperature
Refrigerant
Type
Class
Min temp. (°F) Max. temp. (°F)
R134a
HFC
A1
-4.0 °F
< 122.0 °F
R410A
HFC
A1
-4.0 °F
< 122.0 °F
R513A
HFC
A1
-4.0 °F
< 122.0 °F
R32
HFC
A2L
-4.0 °F
< 122.0 °F
R1234ze
HFO
A2L
-4.0 °F
< 122.0 °F
POSITIONING
The units must:
— They must be installed in an area that cannot be accessed by the public and/or
be protected against access by unauthorised persons, if necessary also install
fences;
— Be positioned on a levelled surface that is able to support the weight of the
unit with the refrigerant load and complete water, in addition to the occasional
presence of maintenance equipment;
— In locations exposed to frost, if the unit is installed on soil, the support base
must rest on concrete columns with a depth greater than the normal depth of
frost of the soil. It is always advisable to build a support base separate from the
main building to avoid the transmission of vibrations;
— If the machine is installed in a place potentially subject to snow accumulation
or ice formations in the base, it is recommended to install the unit with at least
300 mm above the ground;
— It is recommended to use suitably sized anti-vibration supports.
— The unit must be fixed to the anti-vibration supports and these firmly fixed
to the concrete base, see chapter weight distribution and minimum technical
spaces. Check that the contact surfaces of the anti-vibration supports are lev-
elled at the base. If necessary, use spacers or level the base, but in any case make
sure that the anti-vibration supports are placed flat on the surfaces of the base;
— The use of anti-vibration supports MUST be done in combination with the in-
stallation of flexible couplings in the unit's water pipes. The anti-vibration sup-
ports must be fixed to the unit BEFORE being earthed. AERMEC is not responsi-
ble for selecting the capacity of the anti-vibration supports;
— Each side of the unit must have space to allow all routine and extraordinary
maintenance to be performed, the vertical air exhaust must not be obstructed.
PLACE OF INSTALLATION
All the units in this series are designed to be installed outdoors:
on
roofs or on the ground in places where there are no obstacles that could
reduce the air flow towards the finned heat exchanger coils.
The location of the unit must be defined by the system designer or a person who is
an expert in the material and must consider both the purely technical requirements
as well as any local laws in force.
For unit installation it is important to perform the following preliminary prepara-
tion tasks:
The following must be avoided
— Positioning in air shafts, holes and/or basement windows;
— Obstacles or barriers that cause the return of the exhaust air;
— Locations with aggressive atmospheres;
— Areas in which the unit's noise level could be amplified due to reverberations
or resonance;
— Positioning in corners where there is usually an accumulation of dust, leaves
and anything else that could reduce the efficiency of the equipment, obstruct-
ing the passage of air;
— That the air expulsion from the equipment can penetrate into living areas
through doors or windows;
— That the air expulsed by the unit is countered by adverse wind;
— For the positioning of the air-cooled units for outdoor use, choose a place that
is not exposed to excessive wind (install windbreaks if the wind speed exceeds
2.2 m/s).
1
Side-by-side units;
2
Windbreak barrier
recommended for wind above 2.2 m/s;
3
Installation not permitted;
3
2
1
2300 mm
Summary of Contents for NRK 0150
Page 2: ......
Page 39: ...22 11 5167557_03 39 ...