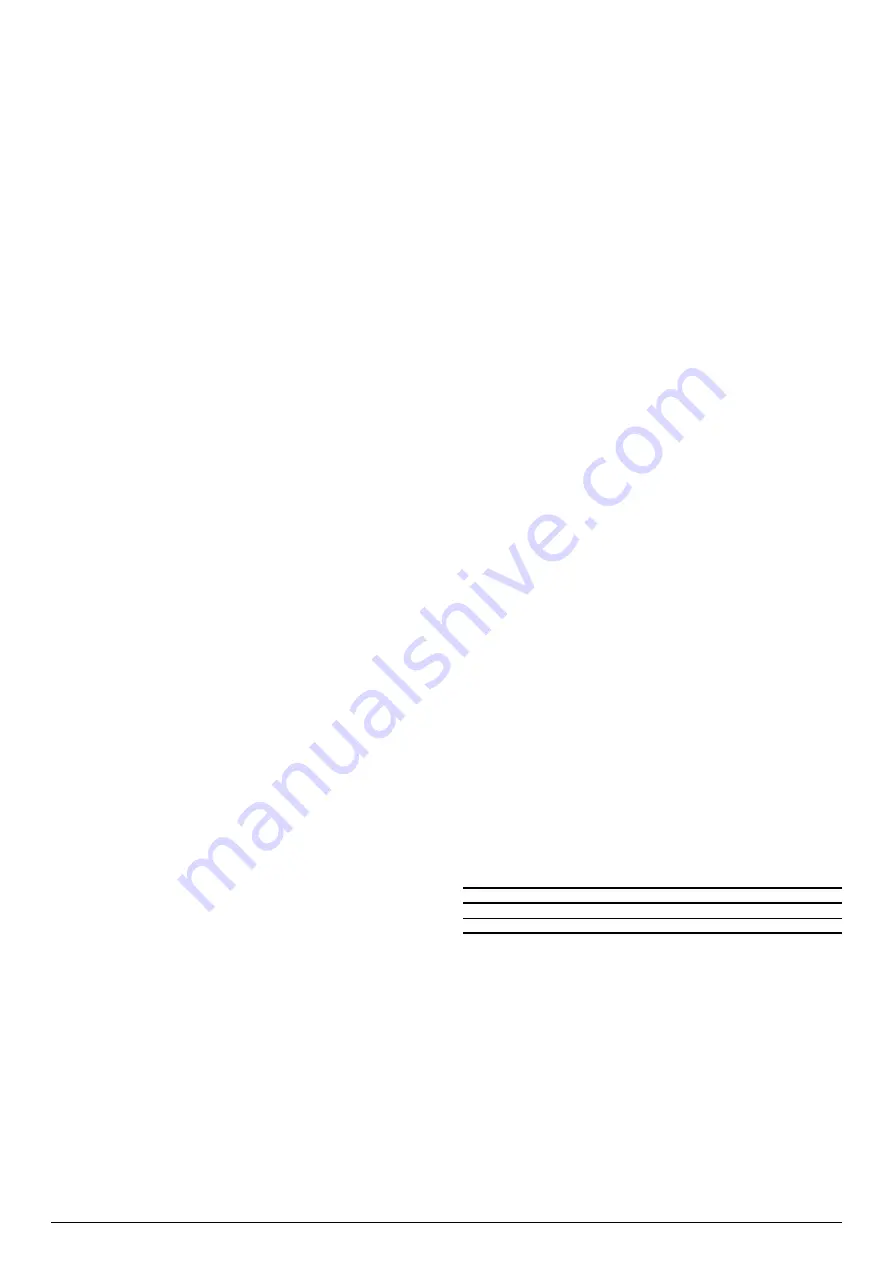
22.05 – 4037365_03
9
2 SELECTION CRITERIA OF THE HEAT EXCHANGERS ACCORDING TO THE PLACE OF INSTALLATION OF
THE UNIT
The guide provides advice for applications. Although recommendations
are given, all the details about the real world application of our prod-
ucts cannot be fully covered in this document.
For these reasons, this section contains the basic warnings and precau-
tions to be taken into account in general, it being understood that:
—
The final choice of the type of exchanger according to the place of instal-
lation is left to the client (or to the professional appointed by him).
—
In any case, it is recommended to wash the coils with adequate frequency
(a maximum time interval of three months is recommended, shorter in
conditions of particularly dirty and aggressive atmospheres) to preserve
their condition and ensure the proper functioning of the unit.
Potentially corrosive outdoor environments include areas near coasts, industrial
sites, densely populated urban areas, certain rural areas or a combination of these
environments. Other factors, including the presence of effluent gas, sewage vents
or open sewage systems and the exhaust of diesel engines can all be harmful for
the microchannel coil.
The purpose of this application guide is to provide general information on the
mechanisms of corrosion and corrosive environments.
SEA COAST ENVIRONMENTS
Coastal or marine environments are characterized by the abundance of sodium
chloride (salt) which is carried by sea spray, mist, or fog. Most importantly, this salt
water can be carried more than several miles by ocean breezes and tidal currents.
It's not uncommon to experience salt-water contamination as far as 6.2 mi from
the coast.
For this reason, it may be necessary to protect the exchangers from electrolytes
of marine origin through the appropriate choice of materials and / or appropriate
protective treatment.
INDUSTRIAL ENVIRONMENTS
Industrial applications are associated with several different conditions that can po-
tentially produce a variety of atmospheric emissions.
Contaminants from sulphur and nitrogen oxides are most often linked to high-den-
sity urban environments. The combustion of coal oils and fuel oils releases sulphur
oxides (SO
2
, SO
3
) and nitrogen oxides (NO
x
) into the atmosphere. These gases ac-
cumulate in the atmosphere and return to the ground as acid rain or low pH dew.
Industrial emissions are not only potentially corrosive: many industrial dust parti-
cles can be loaded with harmful components such as metal oxides, chlorides, sul-
phates, sulfuric acid, carbon and carbon compounds.
In the presence of oxygen, water or high humidity environments, these particles
can be extremely corrosive and in several forms, including general and localised
corrosion, such as pitting and anthill.
MIX OF SEASIDE AND INDUSTRIAL ENVIRONMENTS
Sea mist loaded with salt, associated with the harmful emissions of an industrial
environment, poses a serious risk.
The combined effects of the salt loaded mist and in-dustrial emissions accelerate
corrosion.
Within the manufacturing plants, corrosive gas may result from the processing of
chemicals or by the typical industrial processes used in manufacturing.
Potential sources of risk to be considered are open sewage systems, exhaust vents,
diesel engine exhaust, emissions from heavy traffic, landfills, aircraft and ocean-go-
ing ship engine exhaust, industrial production, chemical treatment facilities (cool-
ing towers in the vicinity) and fossil fuel power plants.
URBAN ENVIRONMENTS
Densely populated areas generally have high levels of emissions of motor vehicles
and increases in duel use for heating buildings.
Both conditions elevate sulfur oxide (SO
x
) and nitrogen oxide (NO
x
) concentrations.
Corrosive atmospheres may even occur in some closed areas, such as facilities with
swimming pools and water treatment systems.
It is advisable to pay particular attention to the positioning of the units if it occurs
in the immediate vicinity of these places, and to avoid that they are installed in the
vicinity of outlets for the expulsion of air coming from them, or in any case exposed
to such atmospheres.
Corrosion severity in this environment is a function of the pollution levels, which in
turn depend on several factors including population density in the area.
Any equipment installed in locations immediately adjacent to diesel engine ex-
hausts, incinerator flues, fuel-fired boiler flues, or areas exposed to fossil fuel emis-
sions shall be considered subject to the same measures as an industrial application.
RURAL ENVIRONMENTS
Rural environments may contain high levels of pollution from ammonia and nitro-
gen products from animal excrements, fertilizers and high concentration of diesel
engine exhaust. The approach to these environments must be entirely similar to
that of industrial environments.
Local weather conditions have a major role in the concentration or disper-sion of
outdoor gaseous contaminants.
Thermal inversions can trap pollutants, thereby producing serious air pollution
problems.
ADDITIONAL TIPS
Although each of the above corrosive environments can be detrimental to the life
of the heat exchanger, several additional factors must be considered before choos-
ing the final design.
The local climate surrounding the site of application may be influenced by the pres-
ence of:
— wind
— dust
— road salts
— swimming pools
— diesel engines discharge / traffic
— Localised mist
— cleaning agents for domestic use
— Sewage system outlets
— many other separate contaminants
Even within 1.9-3.1 mi from these particular local climates a normal environment
with moderate characteristics can be classified as an environment that requires pre-
ventive corrosion measures. When these factors are directly and immediately part
of the environment, their influence is further aggravating.
Only in the absence of potentially risky situations such as those indicated above can
an environment be considered moderate.
Application
Tip
Severe environments
Coils with suitable protection
Moderate environments
Standard coil °
Summary of Contents for NLC 0280H
Page 2: ......