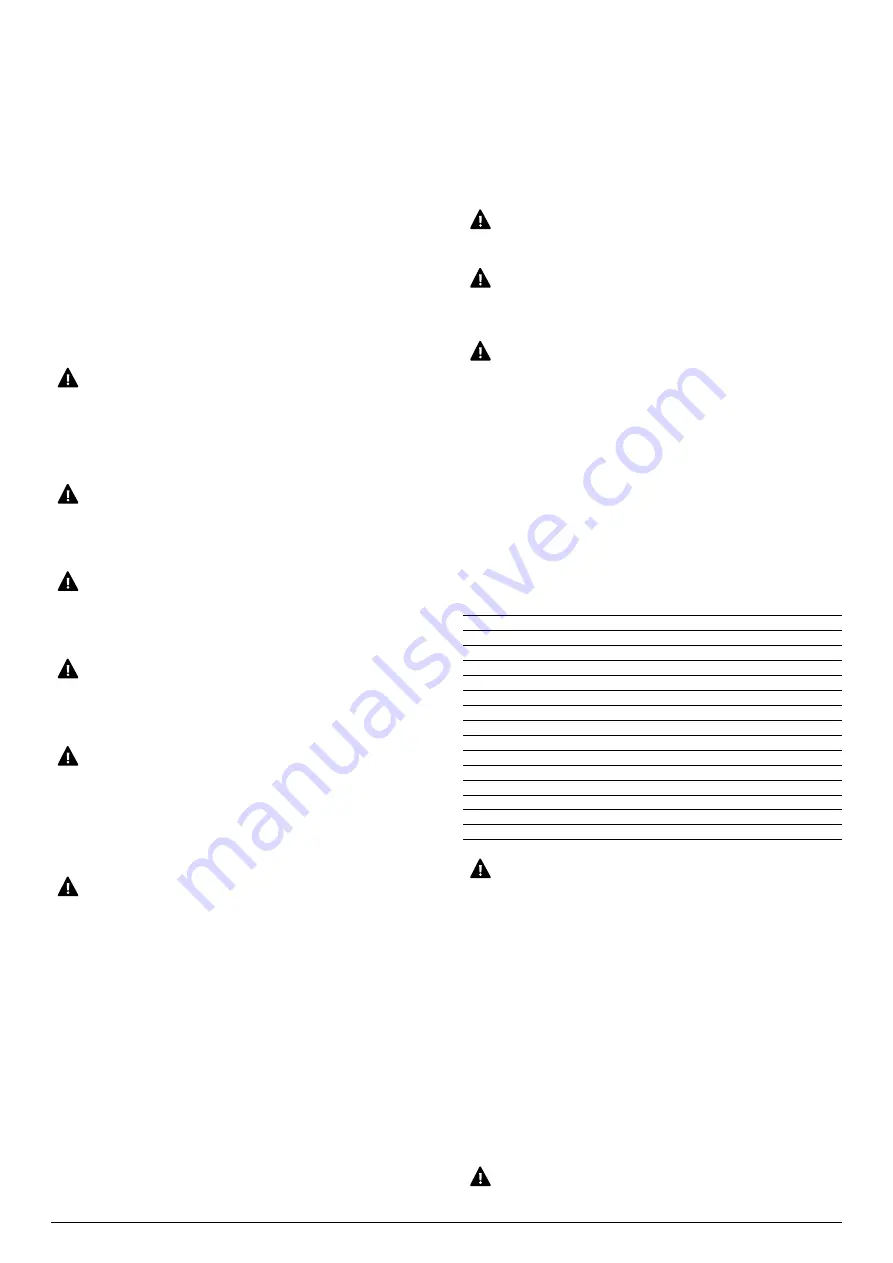
44
22.05 – 4037365_03
14 HYDRAULIC CONNECTIONS
In particular, the unit is intended to be connected:
— to a hydronic system that must be designed to be classified according to EN
378-1 as an indirect ventilated system (ref EN 378-1; 2016, par. 5.5.2.2 ), as an
indirect vented closed system (ref EN 378-1;2016, par. 5.5.2.3 ), or as a double
indirect system according to EN 378-1 (ref. EN 378-1; 2016, par. 5.5.2.4 ).
— The intermediate fluid (water or water-glycol mixture) is in direct communica-
tion with the occupied space and a refrigerant leak in the intermediate circuit
must be dissipated to the atmosphere outside the occupied space and in an
area that is suitably ventilated to prevent the generation of explosive atmos-
pheres.
— In particular, for a closed system this condition requires installing a properly
sized mechanical device in a suitable position of the hydronic circuit for the col-
lection and draining of the refrigerant. If drain and/or safety valves are installed
in the unit, they do not in any way replace this device.
— The automatic air drain must be installed in all the highest points of the hydrau-
lic circuit, outside the building and far from sources of ignition. In order to gua-
rantee that flammable refrigerant will not flow into the environment in the case
of leaks, it is recommended to install it with a primary and secondary circuit.
The units may be available with or without integrated hydronic kit, in any case:
WARNING! Clean the system carefully before connecting the unit:
this is done in order to eliminate possible residues such as welding spatter,
waste, rust or any other impurity from the pipes. These substances could
deposit inside and cause the equipment to malfunction. The connection
pipes must be properly supported so as not to burden the unit with their
weight.
WARNING! The choice and installation of components external to the
unit is up to the installer, who must operate according to the rules of
good technical design and in compliance with the regulations in force
in the country of destination.
WARNING! The hydraulic connection pipes to the unit must be suit-
ably dimensioned for the effective water flow rate requested by the
system when running. The water flow rate to the heat exchanger
must always be constant.
WARNING! The charge or discharge of the heat exchange fluids must
be made during installation by qualified technicians using the fit-
tings provided on the hydraulic circuit. Never use the unit heat ex-
changers to top-up the heat exchanger fluid.
During commissioning, it is mandatory to carry out a seal test on
the air of the hydraulic circuit (minimum pressure 36.3 psi and a
search for leakages on every joint - e.g. using leak detector foam or
soap+water) before filling it with glycol. This is to avoid the need for
corrections due to leaks caused, for example, during the transporta-
tion/handling stage (even though the circuit is tested before leaving
the Aermec factory).
WARNING! Water filter and flow switch:
It is necessary to install a water
filter and a flow switch upstream of each heat exchanger if they are not
supplied with the unit.
CONNECTIONS
Before starting the system, check that the hydraulic circuits are connected to the
correct heat exchangers. The water circulating pump must preferably be installed
upstream so that the evaporator/condenser is subjected to positive pressure. The
water inlet and outlet connections are indicated in the dimensions table in this
manual, or are available online at www.aermec.com
It is important to follow the recommendations (not complete) below:
— The water pipes must not transmit radial or axial forces or vibrations to the ex-
changers (use flexible hoses to reduce the transmitted vibrations);
— It is necessary to install manual or automatic vent valves in the highest points
of the circuit and also provide discharge fittings in the lowest points to allow
emptying the entire circuit;
— To maintain the pressure in the circuits, you must install an expansion tank and
a safety valve;
— Respect the water inlet and outlet connections shown on the unit;
— Install manometer on the water inlet and outlet fittings;
— Install stop valve near the water inlet and outlet fittings;
— Install flexible joints for the connection of the pipes;
— After performing a leak test, insulate the pipes to reduce heat loss and prevent
the formation of condensation;
— If the external water pipes are in an area where it is likely that the environment
temperature drops below 32.0 °F, insulate the pipes and provide an electric
heater. As an option, you can also protect the pipes inside the unit;
— Check the continuity of the earthing;
It is prohibited to operate the unit without an installed and clean wa-
ter filter.
The charge or discharge of the heat exchange fluids must be made
during installation by qualified technicians using the fittings provid-
ed on the hydraulic circuit.
Never use the unit heat exchangers to top-up the heat exchanger
fluid.
WATER CHARACTERISTICS
It is recommended before loading the system to analyse the water, the hydraulic
circuit must have all the devices necessary for treating the water.
The use of untreated water or water that is not treated properly can cause deposits
of incrustations, algae, mud or cause erosion or corrosion, causing serious damage
to the heat exchanger.
It is recommended to request the support of a specialised technician for the water
treatment in order to determine the quality of your water and any corrective inter-
ventions.
Aermec shall not be liable for any damage deriving from the use of "hard" water
that is not treated or that was improperly treated.
The following table provides an incomplete list of the water quality recommended
for the plate heat exchangers:
System: Chiller with plate heat exchanger
PH
7,5 - 9
Total hardness
4,5 - 8,5 °dH
Temperature
< 65 °C
Oxygen content
< 0,1 ppm
Max. glycol amount
50 %
Phosphates (PO₄)
< 2ppm
Manganese (Mn)
< 0,05 ppm
Iron (Fe)
< 0,3 ppm
Alkalinity (HCO₃)
70 - 300 ppm
Chloride ions (Cl-)
< 50 ppm
Sulphate ions (SO₄)
< 50 ppm
Sulphide ion (S)
None
Ammonium ions (NH₄)
None
Silica (SiO₂)
< 30 ppm
It is of fundamental importance to keep the oxygen concentration in
the water under control, especially in open vessel systems. This type
of system, in fact, is very sensitive to the phenomenon of extra-oxy-
genation of the water (an event that can be encouraged by the incor-
rect positioning of some components). This phenomenon can trigger
corrosion processes and subsequent drilling of the heat exchanger
and pipes.
DISCHARGING SYSTEM
In the event the system is stopped during winter, the water in the heat exchanger
can freeze damaging the heat exchanger irreversibly.
To prevent danger of freezing, three solutions are possible:
1.
Full water discharge from the unit;
2.
Using the resistances. In this case the resistances must always be supplied
with electrical power for the entire period of possible freezing (machine in
stand-by);
3.
Operation with glycol/water fluid, with a percentage of glycol based on the
minimum outdoor temperature expected.
WARNING! Make sure that air drain valves have been installed in all
the highest points of the hydraulic circuit and outside inhabited en-
Summary of Contents for NLC 0280H
Page 2: ......