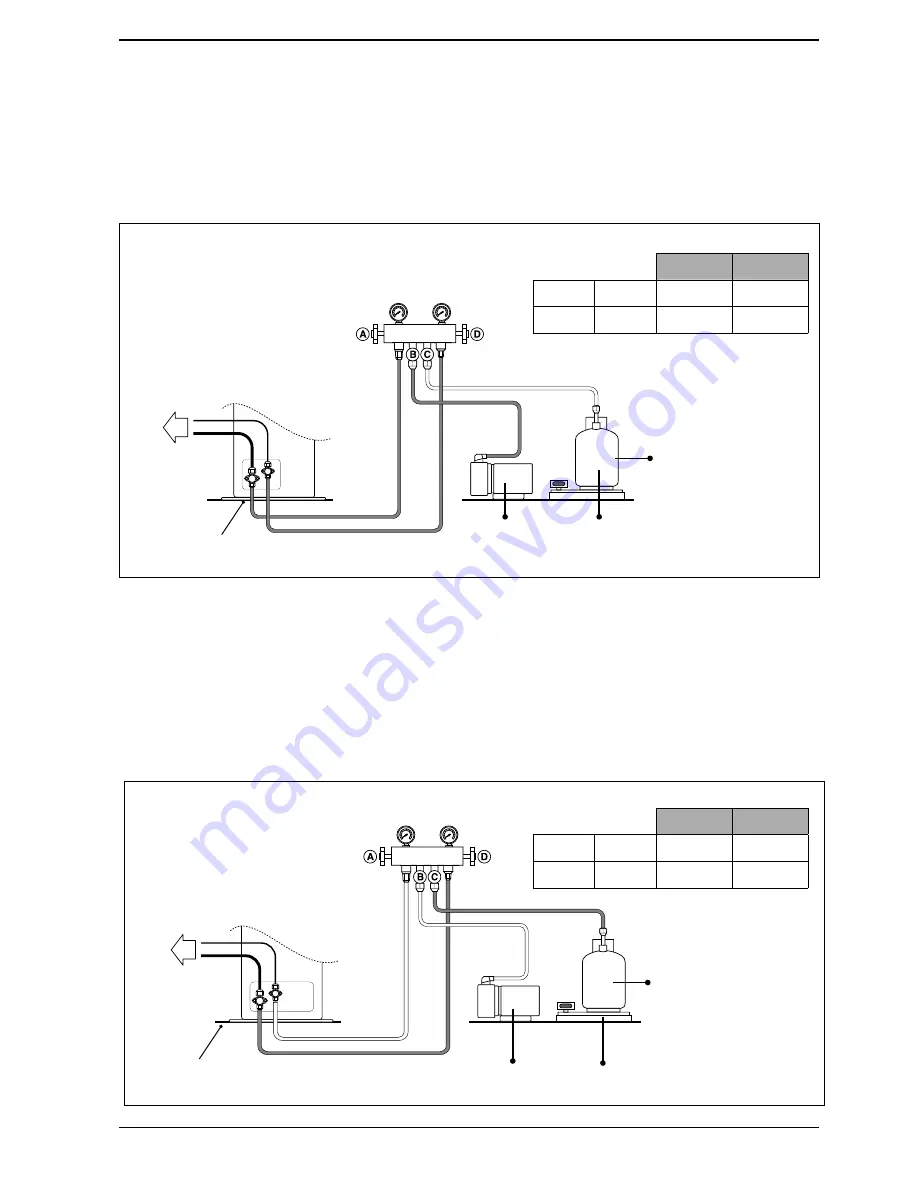
23
IHBI. 1011. 4138500_00
18. NOTES FOR EMPTYING THE LINES
Proceed as follows to empty the lines:
1) Connect the rods between the pump, the manometer unit,
the machine and the cylinder as indicated in the layouts.
2) Check that all cocks on the manometer unit are closed.
(3) Open cocks A-B-D.
(4) Switch the pump on.
(5) Wait for the necessary time.
(6) Close cocks A-B-C-D.
(7) Switch the pump off.
(8) Leave the machine in vacuum and check the low pressure
manometer (it must be in full scale position -1) and check if the
air conditioner keeps the vacuum state.
VACUUM CONNECTIONS ON THE LINES
MANOMETER UNIT
Service cylinder
with drip riser
Scales
Vacuum
pump
INDOOR UNIT
OUTDOOR UNIT
Liquid
Gas
19. NOTES FOR LOADING THE SYSTEM
Proceed as follows to load the system:
(1) Zero the scales.
(2) Open the cylinder and loosen the fi t-
ting near to the cock C.
(3) Open cocks A-C.
(4) Read how much Freon has been in-
troduced into the air conditioner from the
scales.
(5) When loading has been completed,
close the cocks and the cylinder.
(6) Open cocks on the conditioner.
(7) Switch the air conditioner on.
Once the lack of leaks from the system
has been ascertained, when the com-
pressor is not active, load the specifi ed
quantity of R410A liquid into the unit
through the fi lling opening of the outdoor
unit liquid pipe valve.
Make sure to load the specifi ed amount
of liquid refrigerant in the liquid pipe. As
this refrigerant is the mixed type, if it is
added in gaseous form, it could cause a
change in its composition, thus obstruct-
ing normal functioning.
Before loading, check whether the refrig-
erant cylinder is equipped with a siphon.
VACUUM CONNECTIONS ON THE LINES
INDOOR
UNIT SIDE
OUTDOOR
UNIT SIDE
GAS
mm
(inch)
15,87 (5/8") 15,87 (5/8")
LIQUID
mm
(inch)
9,52 (3/8")
9,52 (3/8")
INDOOR
UNIT SIDE
OUTDOOR
UNIT SIDE
GAS
mm
(inch)
15,87 (5/8") 15,87 (5/8")
LIQUID
mm
(inch)
9,52 (3/8")
9,52 (3/8")
MANOMETER UNIT
Service cyl-
inder with
drip riser
Scales
Vacuum
pump
INDOOR UNIT
OUTDOOR UNIT
Liquid
Gas
Summary of Contents for HBI 080
Page 2: ......
Page 35: ...35 IHBI 1011 4138500_00 HBI080C HBI100C HBI120C HBI140C HBI160C ...
Page 44: ......