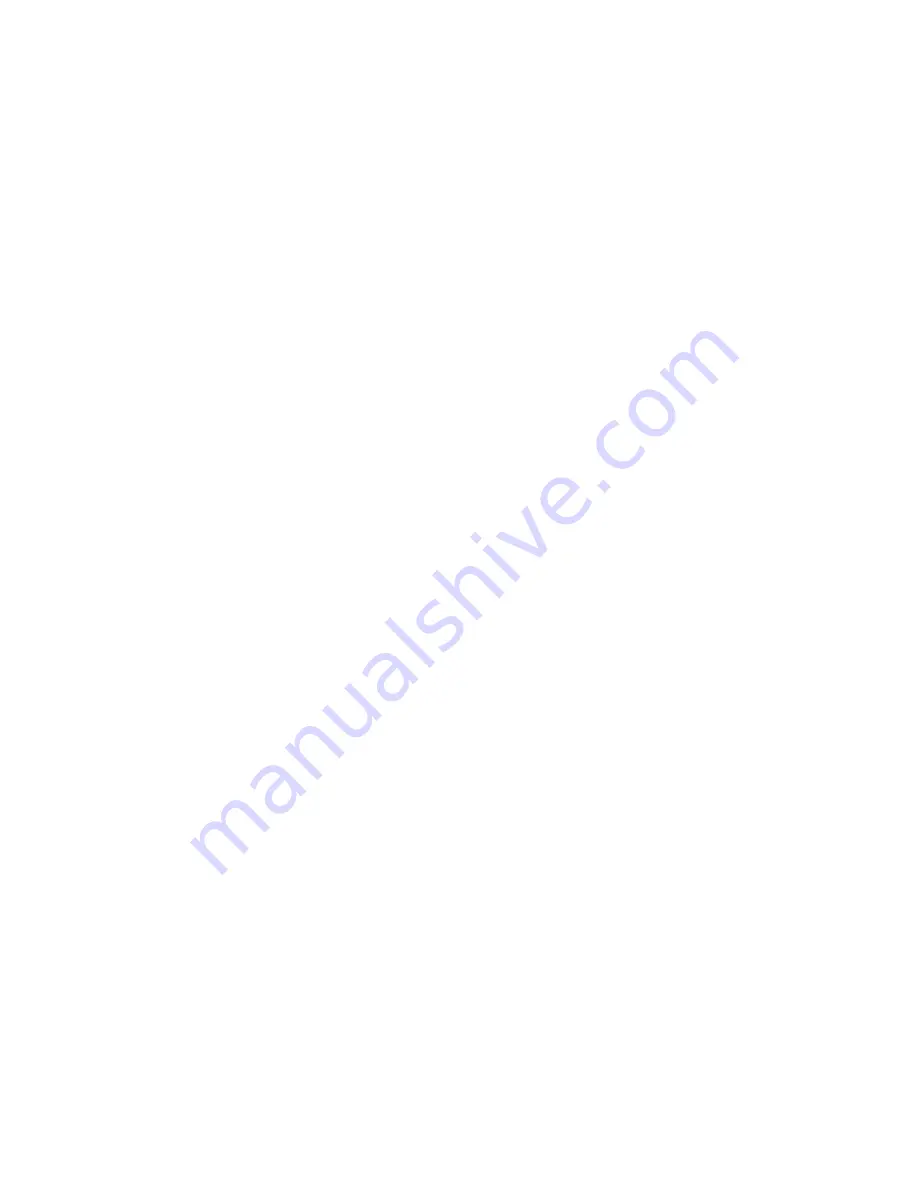
INSTALLATION, OPERATION & MAINTENANCE
6-6
NOTE
The CASCADE MANU (Cascade Manual) mode will time out after a period of 15 minutes.
When this occurs, the boiler will revert the Auto mode function under program control.
9. Turn the Rotary Knob clockwise until CASCADE MANU is displayed.
10. Press the Program Key. BOILER 1 will be displayed.
11. Press the Program Key again. The display will show CODE NO., requesting the valid code to be
entered.
12. Enter code 0000 (4 zeros) by pressing the Program Key four times. The red LED will remain lit
while the four code digits are entered. The LED will turn off after the last code digit is entered.
13. With BOILER 1 displayed, press the Program Key. The red LED will light.
14. Turn the Rotary Knob clockwise and select a fire rate of 100%. Press the Program Key to store
the 100% fire rate.
15. Wait until the Boiler stage fires at the 100% fire rate.
16. Next, turn the Rotary Knob clockwise until BOILER 2 is displayed.
17. Repeat steps 13 through 16 for each Boiler stage.
18. With all Boiler stages firing at 100%, check the inlet manifold gas pressure. Verify that the
pressure is at least 4.0” W.C.
19. If the gas pressure is less than 4.0” W.C., contact your gas supplier. Do Not proceed until the
supply gas pressure is corrected.
20. If the gas pressure is adequate at full-fire, close the hinged panel of the Controller.
21. Set the
ON/OFF
switch on the front of the boiler to the
OFF
position.
22. Turn off the gas supply to the boiler by closing the external shut-off valve.
23. Remove the manometer from the gas manifold pressure tap. Close the tap by rotating the
adjustment screw fully clockwise to its stop. This manometer will be used to measure gas valve
outlet pressure for each stage during the Combustion Calibration procedure in paragraph 6.5.5.
6.5.5 COMBUSTION CALIBRATION.
The Modulex boiler is combustion calibrated prior to shipment from the factory. However, AERCO
recommends that the following calibration and adjustments be performed due to possible differences in
altitude, BTU content, installed gas supply piping and regulators used.
In addition to checking the oxygen (O
2
), carbon dioxide (CO
2
) and carbon monoxide (CO) combustion
readings, this procedure will also check the gas valve outlet pressure for each Boiler stage. This is
accomplished by connecting the 16” W.C. manometer (or gauge) to the outlet pressure tap of the valve
(Figure 6-2) for the boiler stage being checked.
NOTE
The manometer installed in steps 1, 2 and 3 will be moved each time the next Boiler
stage is calibrated. Ensure that the outlet pressure port of the gas valve is fully closed
(rotated fully clockwise) prior to connecting the manometer to the valve for the next Boiler
stage to be calibrated.
Summary of Contents for Modulex 1060
Page 16: ......
Page 25: ...INSTALLATION OPERATION MAINTENANCE 2 9 Figure 2 7 Sample Data Plate ...
Page 33: ...INSTALLATION OPERATION MAINTENANCE 5 3 Figure 5 2 ...
Page 34: ......
Page 44: ......
Page 51: ...APPENDIX A A 1 APPENDIX A Temperature Sensor Resistance Charts ...
Page 53: ...APPENDIX B B 1 APPENDIX B Modulex Parts List ...
Page 54: ...APPENDIX B B 2 ...
Page 55: ...APPENDIX B B 3 ...
Page 56: ...APPENDIX B B 4 ...
Page 58: ......