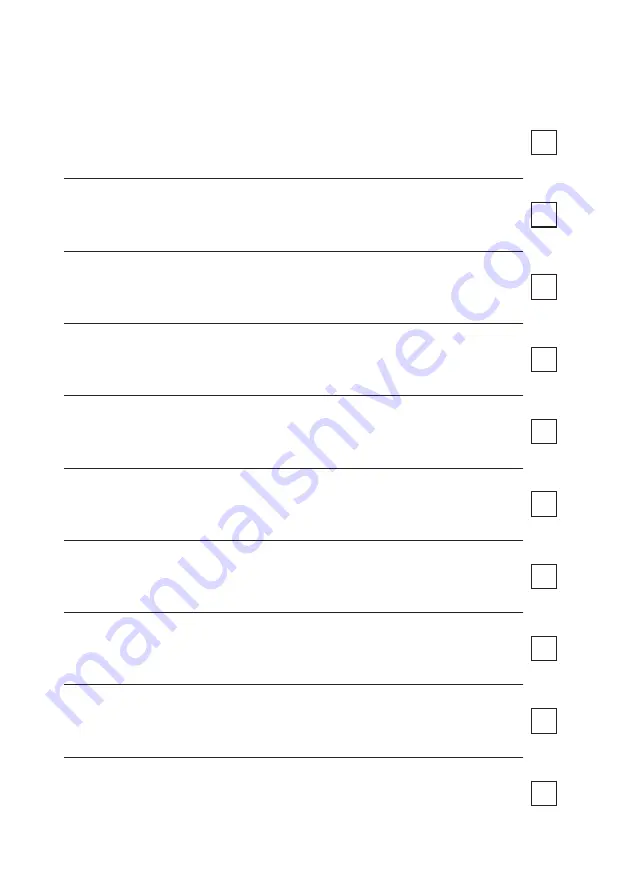
4
Control List
1
Make sure the unit receives power and grounding is done!
2
Make sure the length of electric cables is correct! (Check for overheating on cables!)
3
Check if the cables heading to the electrical box are shielded (protected against magnetic
field) and shield is grounded. If not, replace!
4
Check if the exhaust and supply filters are clean and make sure they do not prevent air flow!
5
Make sure the drain hose is connected and check for any blockages through the drain line!
If needed, clean it!
6
Please check that the duct dimensions used in the duct system are correct and of the same
dimension of the units duct connection. If wrong correct it with appropriate one.
7
Make sure there is enough service space for installation. If not, repeat installation.
8
In extremely cold climates in which freezing may occur on the heat recovery unit, use electric
pre-heater at the fresh air suction to raise the air temperature to -8 °C or above.
9
Make sure electrical connections are done as it is described in this manual. Make necessary
corrections if there is any faulty connection.
10
Check for unusual noise or vibration after the installation. If there is, control if anti-vibration
pads are used.