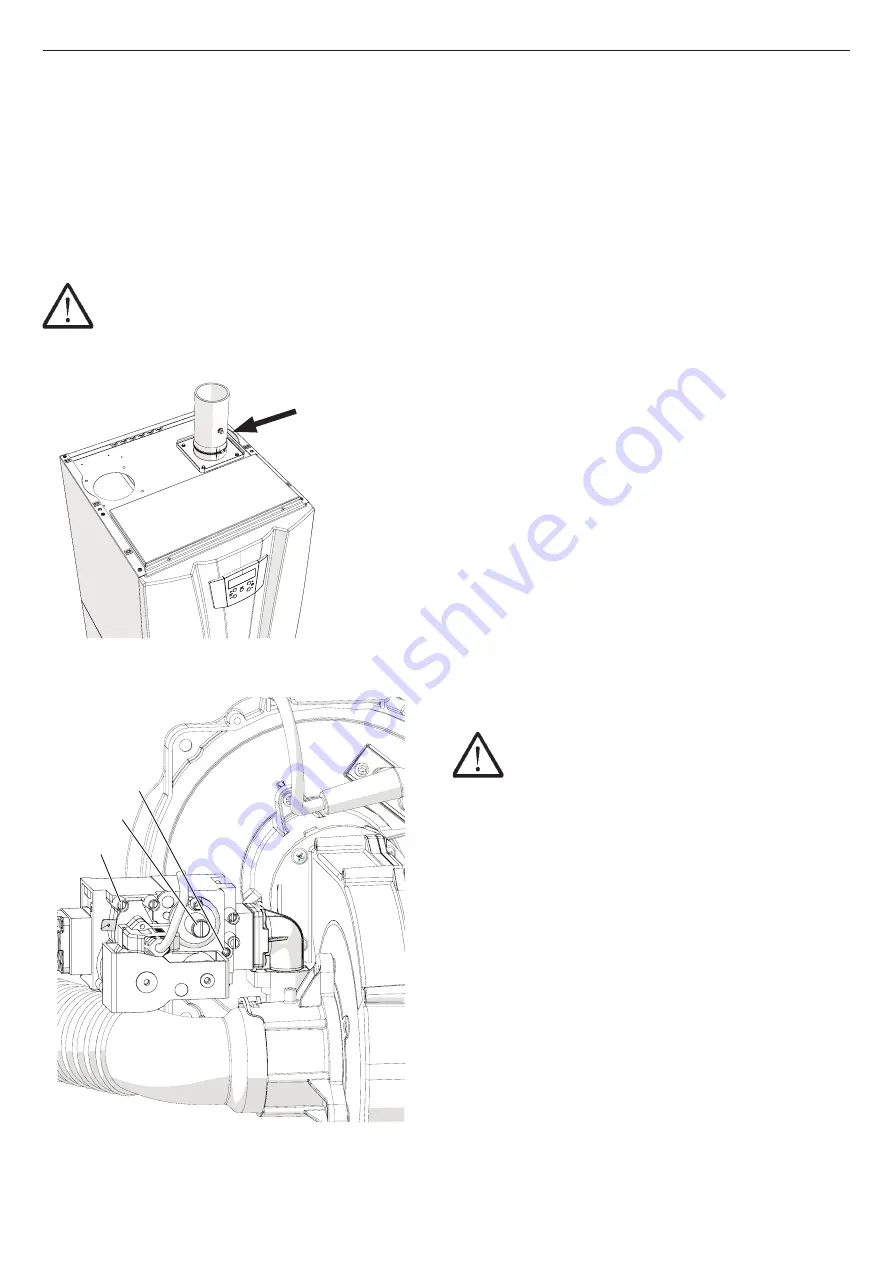
68
60T - 280T
COSMOGAS
16 - START-UP
Figure 16-9 - Taking combustion analysis
Figure 16-10 – Gas valve
D - Gas inlet tapping point.
E - CO2 regulation screw.
F - Factory regulation screw (do not touch).
E
D
F
E
D
F
020010.01.022
16.8 - Controlling the level of
CO2 and any adjustments
Table 16-8 shows the correct values of CO2 for a boiler
working in normal conditions, at an altitude of less than 1000
metres. A different value from the one shown can cause
malfunctions. A combustion analysis must be carried out to
check and make any necessary adjustment to this value.
Proceed as follows:
16.8.1 - Check the CO2 content and make
any necessary adjustment on boiler
models 70T
WARNING! If during this procedure a CO value
of more than 1000 ppm is detected, turn off the boiler
and contact the dealer.
1.- If one is not already present, you will have to make a hole
for the combustion analysis, located about 200 mm from the
exhaust gases outlet pipe (see figure 16-9 corresponding to
stopper “F”).
2.- Turn on the boiler and open the link between terminals “10”
and “11”;
3.- Make sure that the temperature demanded is higher than
that of the boiler/hot water heater;
4.- Go into the installer menu (see section 17.15) and set
parameter
2010
to
HIGH.
Now the boiler will operate
at maximum power for 20 minutes;
5.- Wait two or three minutes for the CO2 to stabilise;
6.- Insert the sensor to read the value of CO2 in point “F” shown
in figure 16-9;
7.- Compare the value of CO2 detected with that shown in table
16-8; make sure you read the value for the type of gas being
used. If the value of CO2 is not that shown in table 16-8, you
must correct it using screw “E” in figure 16-10. Using a 2.5
mm six-sided spanner (turn the screw clockwise to reduce
the value of CO2 and anticlockwise to increase it), make
small turns, always waiting for the CO2 value to stabilise
before continuing with further movements, until you reach
the desired value.
8.- Once you have reached the correct value of CO2 as in table
16-8, seal the screw with red paint or a similar system to
discourage any tampering with it.
9.- Set parameter
2010
at
LO
. The boiler will now operate
at minimum power for 20 minutes.
10.- Wait two or three minutes for the CO2 to stabilise;
11.- Compare the reading for the value of CO2 with that shown
in table 16-8, make sure you read the value for the type of
gas being used. The value of CO2 must fall within the values
shown, if that is not the case you must turn off the boiler and
contact the manufacturer.
12.- Set parameter
2010
to
OFF
to return the boiler to
normal operation.
13.- Close the combustion analysis hole in figure 16-9, with
a suitable stopper “F” as shown in the manufacturer’s
instructions for the outlet pipe.
WARNING! Once stopper “F” is in position with
the boiler at maximum power, check there are no leaks
of exhaust gases.
F - Taking combustion analysis
F
020010.01.042