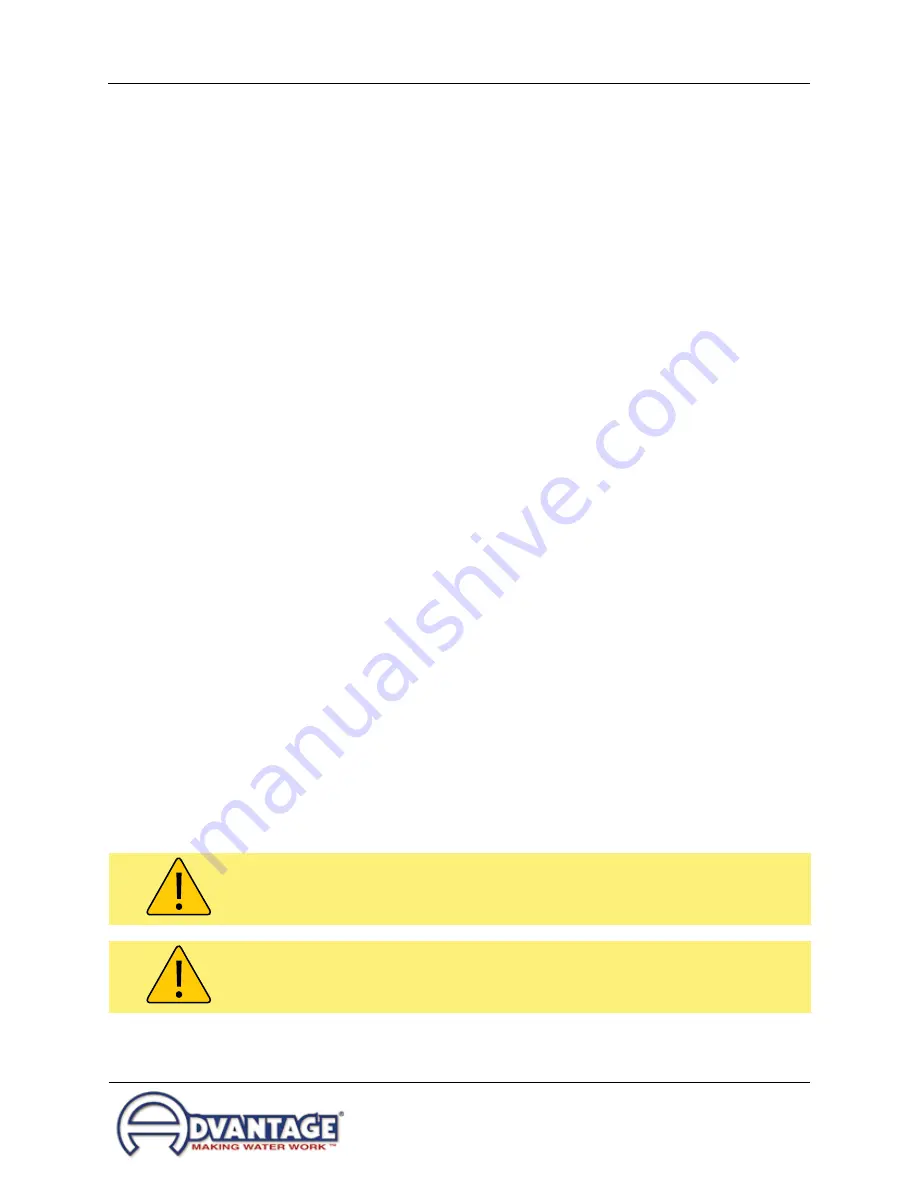
BC-N4 Glycol Chiller
Page: 30
ADVANTAGE ENGINEERING, INC.
525 East Stop 18 Road Greenwood, Indiana 46142
317-887-0729 Fax: 317-881-1277
Service Department Fax: 317-885-8683
Email: [email protected]
control waits the amount of time specified by the “LP TIME” potentiometer before
indicating an fault and turning off the compressor. If the condition is corrected
before the time expires, no fault occurs. If a low pressure condition occurs 15
seconds after the compressor turns on, the instrument waits 20 seconds before
indicating a fault and turning off the compressor.
Note: refer to section 4.4 of this manual for additional Low Refrigerant Pressure
troubleshooting.
E.
TEMPERATURE DISPLAY
1.
A three digit display window indicates the appropriate temperature. The window
also displays the numeric value for the setpoint temperature.
2.
The To Process temperature is always displayed unless a button has been
pressed. If there is a probe error, the display will show three dashes “---”.
3.
When the water temperature in the chiller is above approximately 100°F the
display will show three dashes “---”.
F.
PRESSURE GAUGES
1.
PROCESS PRESSURE GAUGE: Indicates process pump pressure.
2.
REFRIGERANT HEAD PRESSURE GAUGE: Indicates refrigerant pressure on
the discharge side of the compressor. The refrigerant head pressure is also the
condensing pressure which is critical to equipment efficiency.
3.
LOW PRESSURE GAUGE: Indicates refrigerant pressure on the suction side of
the compressor. This pressure will fluctuate with the process temperature.
3.4 SHUT DOWN/disconnect SEQUENCE
A.
PRECAUTIONS/WARNINGS
1.
The operator must follow all shut down procedures outlined in this manual. If the
operator fails to follow all procedures outlined in this manual, an unsafe condition
can develop resulting in damage to the unit or personal injury.
WARNING: Relieve static pressure before disconnection process lines.
WARNING: Follow all shut down procedures outlined in this manual.
Summary of Contents for BC-N4 Series
Page 2: ......
Page 6: ...Page 6 THIS PAGE INTENTIONALLY BLANK ...
Page 20: ...Page 20 THIS PAGE INTENTIONALLY BLANK ...
Page 32: ...Page 32 THIS PAGE INTENTIONALLY BLANK ...
Page 48: ...Page 48 THIS PAGE INTENTIONALLY BLANK ...
Page 54: ...Page 54 THIS PAGE INTENTIONALLY BLANK ...
Page 62: ...Page 62 THIS PAGE INTENTIONALLY BLANK ...
Page 63: ...END 2016 ADVANTAGE ENGINEERING INC RE 09 27 2016 ...
Page 64: ......