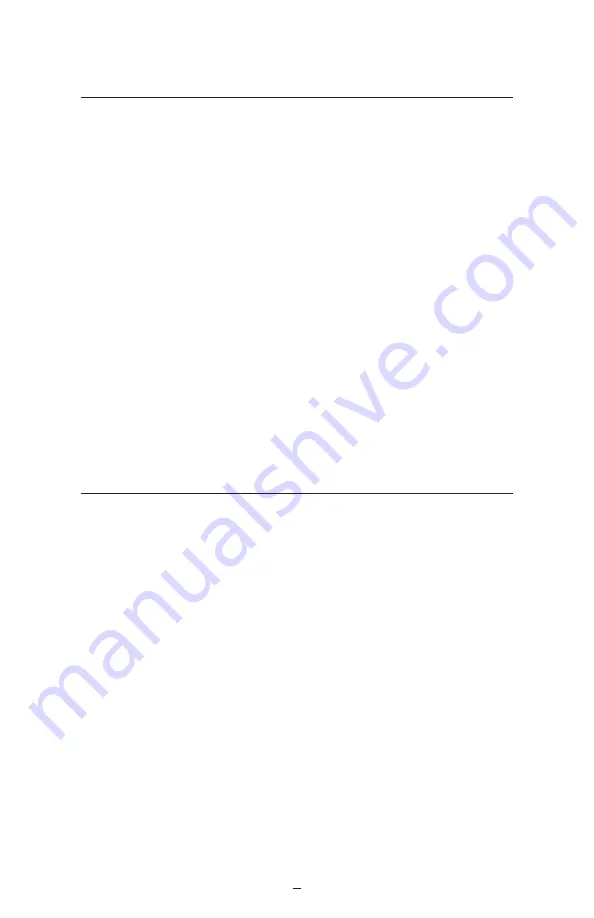
MOUNTING
WARNING: Before attempting to install and operate these pres-
sure switches, read and fully understand the safety precautions
on page 2 in this booklet. Failure to follow the safety precautions
may result in serious personal injury and/or damage to equipment.
1. Pressure switches are usually mounted adjacent to the end of the
manifold and connected to the manifold header with
1
⁄
8
inch tubing
and compression-type male connectors supplied with each unit.
2. The device can be mounted in any position however, for weather
tight installation in high humidity areas, orient housing so electri-
cal connection is at the 6 o’clock position to prevent condensate
from collecting in the housing enclosure.
Note:
Line mounting by either process connection or electrical
connection is not recommended.
3. Secure housing mounting pad to the wall or other support with
two suitable
1
⁄
4
inch bolts.
Note:
When mounting to irregular or uneven surface, install rub-
ber washers (provided) on bolts between housing and mounting
surface to prevent deformation of housing, which could change
relative positions of internal parts and affect calibration or render
the device inoperative.
PROCESS CONNECTION
WARNING: DO NOT exceed pressure and temperature specifica-
tions during operation. DO NOT operate the pressure switch
under any circumstances if it leaking or otherwise malfunction-
ing. Damage to equipment and/or injury to personnel may result.
1. Connect
1
⁄
4
in. NPT male x
1
⁄
8
compression connector to pressure
switch using two wrenches: one to hold hex flats on pressure port,
the other to tighten male connector. Use Teflon
®
tape on all pipe
threads to prevent galling.
Note:
Be certain process connection is tightened and positioned so
bending and torsional forces imposed on pressure switch are mini-
mal. Use care not to loosen pressure port from body or body from
housing.
2. Connect
1
⁄
8
in. NPT male x
1
⁄
8
compression connector to manifold or
pipeline.
3. Install
1
⁄
8
in. tubing between pressure switch and manifold or pipe-
line using the male connectors installed in steps 1 and 2 above.
4. Leak test all connections with a nonhazardous gas using either a
soap solution, such as Snoop
®
or a gas leak detector.
4