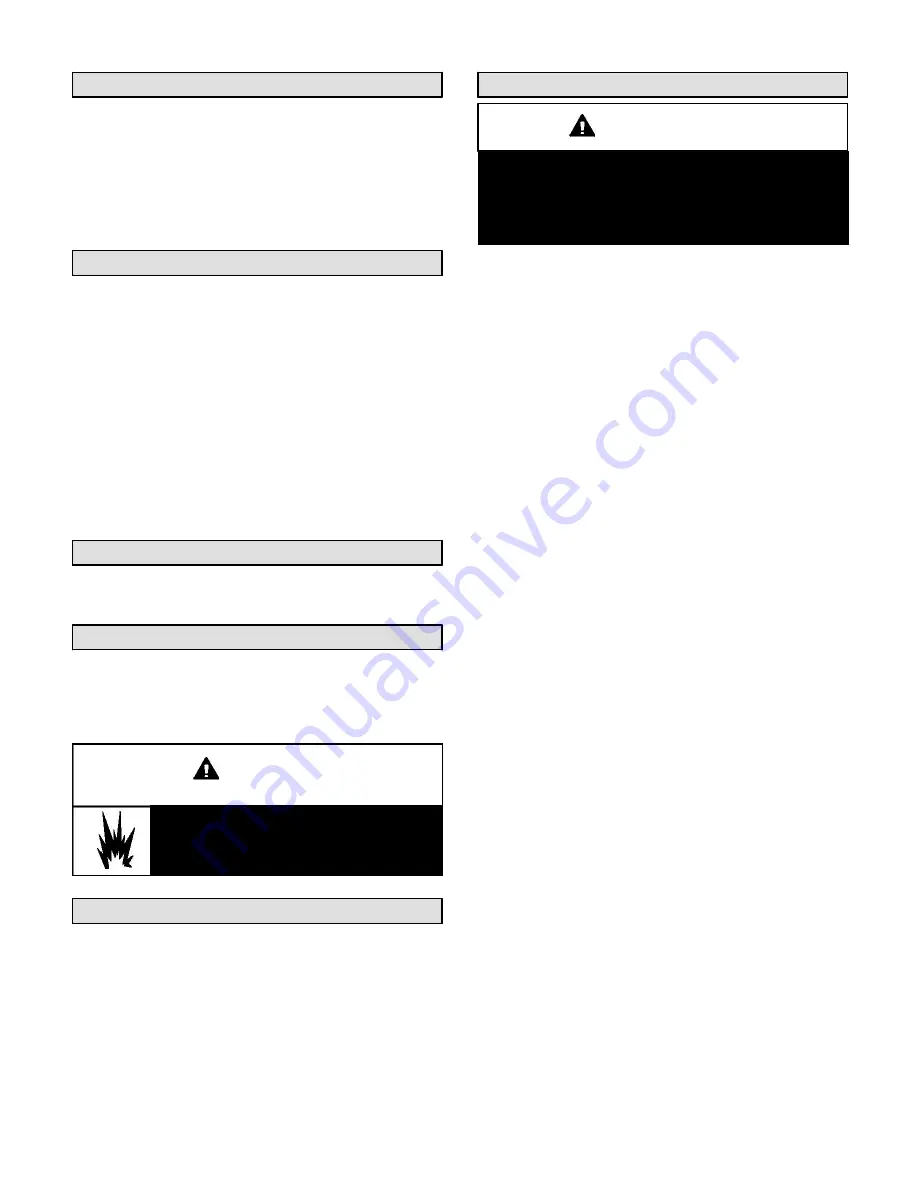
Gas Flow
To check for proper gas flow to the combustion chamber,
determine the Btu input from the appliance rating plate.
Divide this input rating by the Btu per cubic feet of
available gas. Result is the required number of cubic
feet per hour. Determine the flow of gas through the
gas meter for two minutes and multiply by 30 to get the
hourly flow of gas.
Gas Pressure Adjustment
1
− Check gas line pressure with unit firing at maximum
rate. A minimum of 5" (127mm) w.c. for natural gas
or 11" (279mm) w.c. for LP/propane gas should be
maintained for proper unit operation.
2
− After line pressure has been checked and adjusted,
check regulator pressure. Adjust manifold pressure
to values specified on the unit rating plate. See
figures 8, 9, and 10 for gas pressure adjustment
screw location. A natural gas to LP/propane gas
changeover kit is required to convert unit in the field.
Refer to installation instructions provided with
changeover kit for conversion procedure.
Limit Control Switch
The limit control switch(es) are factory-set and are not
field-adjustable.
Louver Vane Adjustment
The SEP series unit heaters are provided with adjustable
louver vanes. Air flow from the unit can be directed down,
straight, out, up, or any combination of these.
WARNING
DO NOT CLOSE the bottom three lou-
vers on SEP. Premature failure to the
heat exchanger can occur.
Combustion Air Pressure Switch
This pressure switch checks for proper combustion air
inducer operation before allowing an ignition trial. The
switch is factory
−set and no field adjustment is necessary.
Service
CAUTION
The unit heater and vent system shall be inspected
once a year by a licensed professional service
technician, or equivalent.
LUBRICATION
1
−
Combustion air inducer motor bearings are
pre
−lubricated and sealed. No further lubrication
is necessary.
2
−
Fan motor bearings should be lubricated
according to manufacturer’s instructions on each
motor. If no instruction is provided, use the
following as a guide: motors with oiling ports are
pre
−lubricated for an extended bearing life,
re
−lubricate with a few drops of SAE No. 10
non
−detergent oil once e
very two years.
BURNERS
1
−
Periodically examine burner flames for proper
appearance during the heating season.
2
−
Before each heating season examine the burners
for any deposits or blockage that may have
occurred.
3
−
Clean burners as follows:
a
−
Turn off both electrical and gas supplies to unit.
b
−
Disconnect gas supply piping, high tension
and sensor leads. Remove gas manifold.
Remove burner tray.
c
−
Clean burners as necessary. Make sure that
burner heads line up properly to ensure flame
crossover. Check spark gap on electrode and
adjust if required. The gap should be
between 0.110" and 0.140" (2.8 mm to 3.6
mm). The gap may be checked with
appropriately sized twist drills or feeler
gauges.
d
−
Reinstall burner tray, gas manifold, high
tension and sensor leads. Reconnect gas
supply piping.
e
−
Restore electrical power and gas supply.
Follow lighting instructions to light unit. Check
burner flame.
Turn off gas and electrical power to unit before
per-forming any maintenance or service
operations on this unit. Remember to follow
lighting instructions when putting unit back into
operation after service or maintenance.
DO NOT CLOSE the bottom three louvers
on SEP. Premature failure to the heat
exchanger can occur.
16
Summary of Contents for SEP-100
Page 20: ......