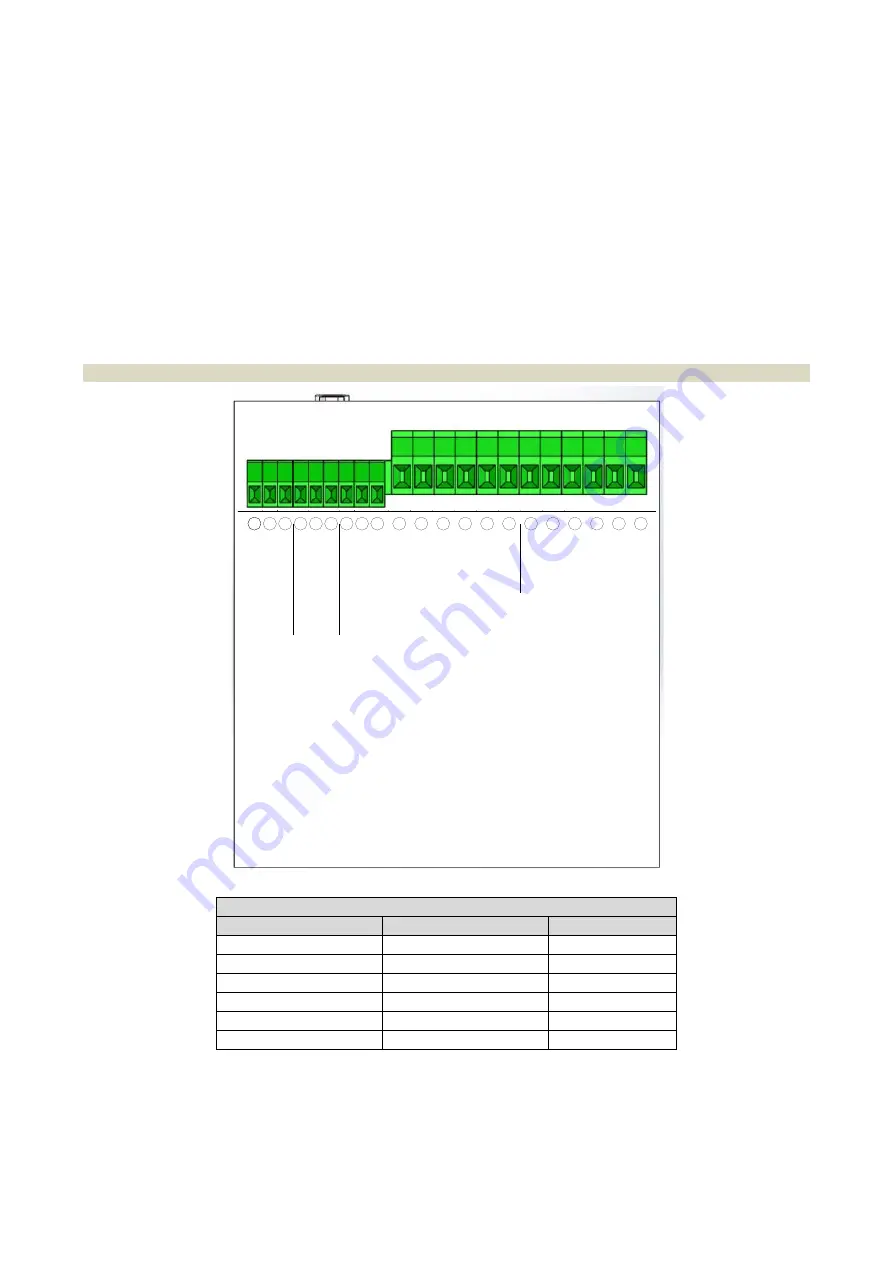
1569
‐
PT060EE1
Rev.
7
Page
17
of
62
3.7
Connection of load cells (side A)
The
cable
coming
from
the
load
cells
or
junction
box
must
be
connected
to
the
terminals
located
on
the
rear
of
the
instrument
and
called
LOAD
CELL
1.
Connection
between
the
load
cell
and
the
instrument
must
be
carried
out
with
a
shielded
cable.
The
cable’s
shield
must
be
connected
to
the
ground.
Connection
must
take
place
respecting
the
colour
code
indicated
on
the
load
cells.
T060
foresees
the
standard
connection
of
6
‐
wire
load
cells.
In
case
of
connection
of
4
‐
wire
load
cells,
connect
the
reference
wires
to
the
relative
polarities
of
the
power
supply
cables.
MAKE
SURE
THE
CONNECTION
CABLE
BETWEEN
LOAD
CELLS
AND
INSTRUMENT
IS
DUCTED
IN
TROUGHS
SEPARATE
FROM
THOSE
OF
POWER
LINES,
IN
ORDER
TO
AVOID
COUPLING
THAT
MAY
PREJUDICE
THE
MEASUREMENT
ACCURACY.
3.7.1
Connection of load cells 1
LC1
INDICATION
FUNCTION
TERMINAL
+A
+
Excitation
39
‐
A
‐
Excitation
38
+S
+
Signal
37
‐
S
‐
Signal
36
+R
+
Reference
35
‐
R
‐
Reference
34
31
28 29 30
-S
+R
-R
34
32 33
+S
36
35
37
-A
+A
39
38
-R
+R
-S
+S
-A
+A
LOAD CELL 2
LOAD CELL 1
23
20
19
22
21
25
24
27
26
SGND
3
IOUT
+
VOUT
+
SGND
2
-RS485
+RS
4
85
SGND
1
-RS
485/R
X
+R
S485/TX
SERIAL
OUT 1
SERIAL
OUT 2
ANALOG
OUTPUT
OPTO
OPTO