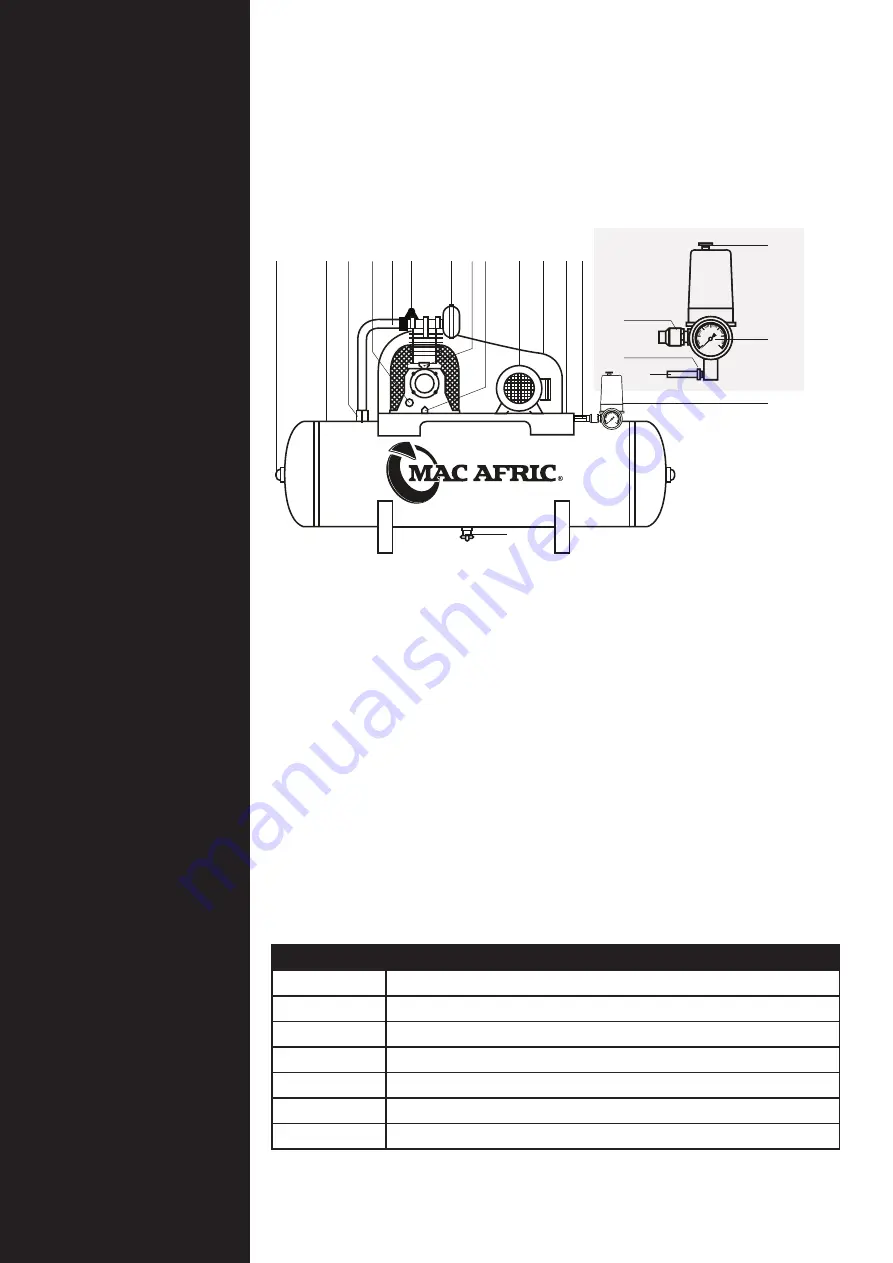
AIR COMPRESSORS
DIRECT & BELT DRIVEN MANUALS
COPYRIGHT ADENDORFF MACHINERY MART
6
ELECTRICAL COMPRESSORS
1
2
5 6
7
10
15
Illustrative purposes only
14a
14c
14e
14d
14b
14
11 12 13
8 9
3
4
GENERAL ARRANGEMENT (BELT DRIVEN MODEL)
I. Inspection Plug
8. Oil Filler/Breather
14. Pressure Switch
2. Air Receiver
9. Oil Drain Plug
14a. On/Off Switch
3. Non-return Valve
10. Electric Motor
14b. Pressure Gauge
4. Oil Level Sight Glass
11. Wire Guard
14c. Saftey Valve
5. Air Delivery Pipe
12. Saddle
14d Air Bleed Valve
6. Air Compressor Pump
13. Air Bleed Pipe
14e. Air Bleed Pipe
7. Air Intake Filter
15. Drain Tap
Note: Illustrations are for reference only. Certain models may differ.
LUBRICATION
PUMP:
Use Adendorff Synthetic Compressor oil.
VOLUME
MODEL
250 ml
COMPRE-024-515-115
300 ml
COMPRV-123
450 ml
COMPRE-517 , COMPRV-120-130
1000 ml
COMPRE-210-615-315-310
1600 ml
COMPRV-510-575
1700 ml
COMPRV-355-375-377
1750 ml
COMPRE-300
Figure 2