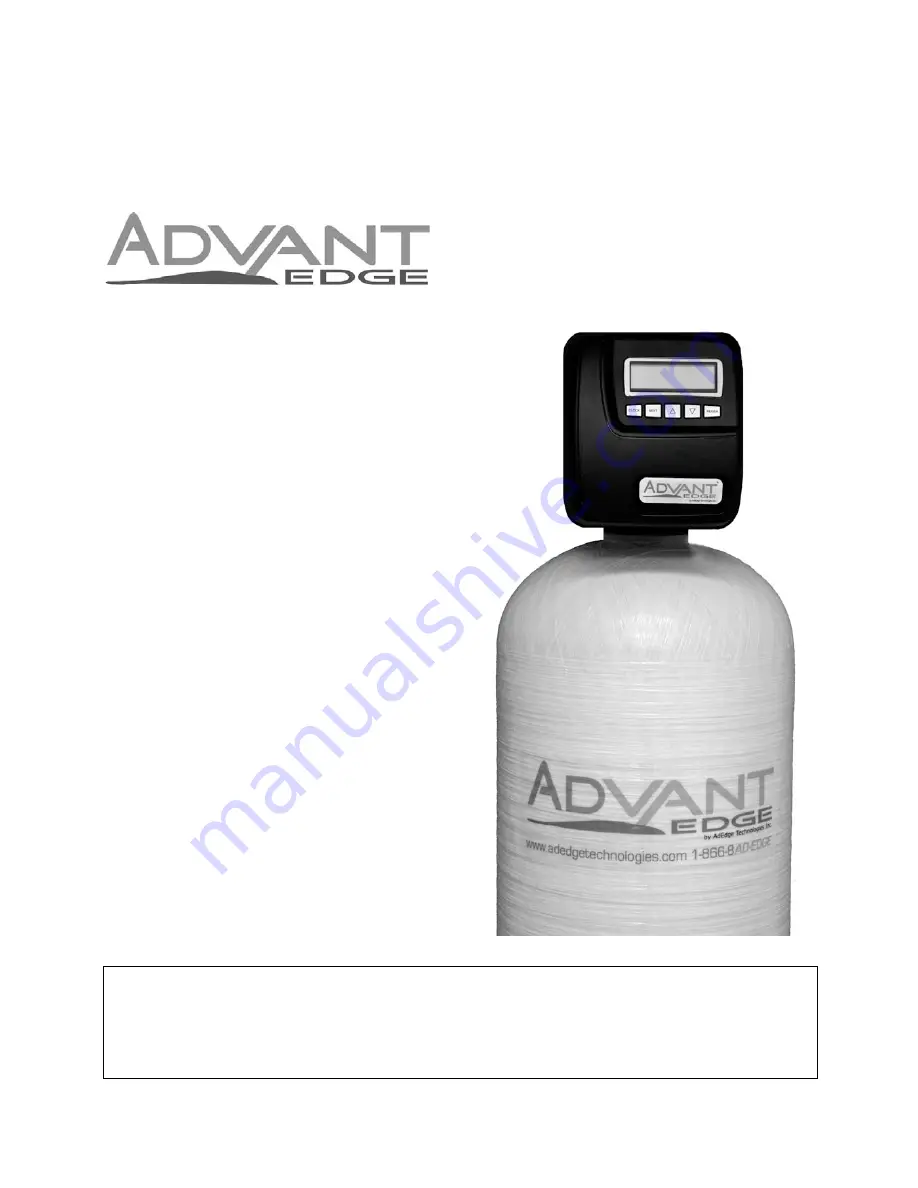
Service and Installation Guide
Models:
POE-5-1252
POE-7-1354
POE-10-1465
Arsenic Treatment Solutions
Designed by:
AdEdge
Water
Technologies,
LLC.
5152 Belle Wood Court, Suite A
Buford, GA 30518
Toll Free: 866-823-3343
Phone: 678-835-0052
Fax: 678-835-0057
The service and installation guide is designed to assist the professional
water treatment provider and qualified staff. This document is not
intended for the end user.
Medallion Series
Arsenic Removal Systems
TM
by AdEdge
Water
Technologies
,
LLC
.