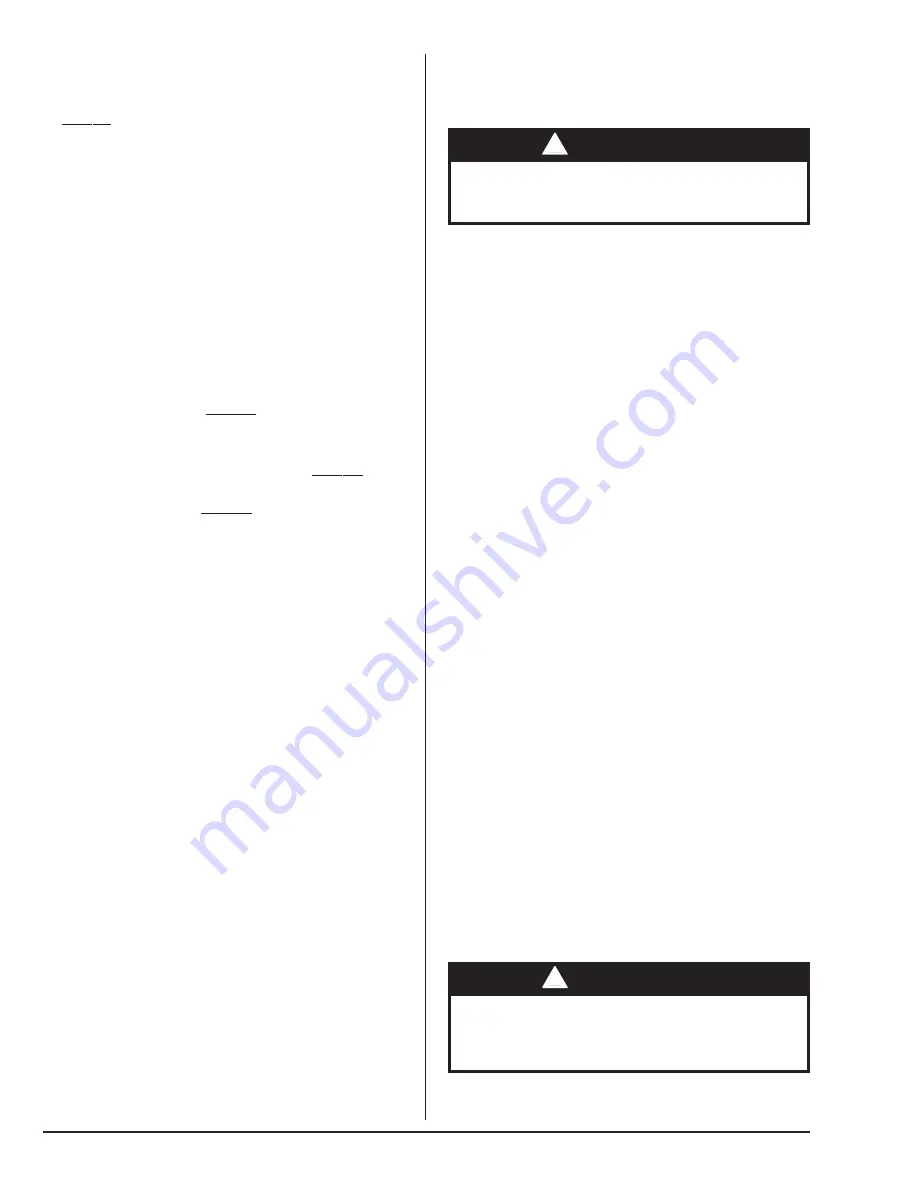
18
American Dryer Corp.
WFR 112807 - 15
Gas Pressure Testing _________________
For proper operation, the gas pressure must be correct,
consistent and maintained at the gas pressure rates shown
on page
14. Provisions are made at the gas valve for taking
gas pressure readings.
There are two types of devices used to measure gas
pressure. They are the spring/mechanical type gauge and
the manometer. The use of the spring/mechanical type
gauge is not recommended because they are very easily
damaged and are not always accurate. The preferred type
of gauge is the manometer because it is a simple device to
use and is highly accurate. A manometer is simply a glass
or transparent plastic tube with a scale graduated in inches
or millibars. When it is filled with water and pressure is
applied, the water in the tube rises, showing the exact gas
pressure.
Gas Pressure Test Procedure
Turn gas cock in gas supply line to “OFF” position.
60 Hz dryers: Install pressure tap and attach manometer
(refer to the illustration on page
Turn gas cock to “ON” position.
Start the dryer in Heat Mode and wait for ignition. Gas
manifold pressure should be as shown on page
If the gas pressure needs to be adjusted, refer to “Gas
Pressure Adjustment” on page
Once test is complete, turn gas cock to “OFF” position.
Remove manometer. Tighten screw inside the pressure
tap or install plug.
Turn gas cock to “ON” position and check for leaks with
soap solution with main burner “ON.”
Water Information ____________________
Before You Start
Check Local Codes and Permits
Call your local water company or the proper municipal
authority for information regarding local codes.
IMPORTANT:
It is your responsibility to have all plumbing
connections made by a qualified professional to ensure
that the plumbing installation is adequate and conforms to
local, state, and federal regulations or codes.
It is the installer’s or owner’s responsibility to see that the
required water pressure, pipe size, or connections are
provided. The manufacturer assumes no responsibility if
the fire suppression system is not connected, installed, or
maintained properly.
Installation
Water Supply
The fire suppression system must be supplied with a
minimum water pipe size of 1/2-inch (12.7 mm) and be
provided with 40 psi +/- 20 psi (2.75 bar +/- 1.37 bar) of
pressure.
If the rear area of the dryer or the water supply is located in
an area where it will be exposed to cold/freezing
temperatures, provisions must be made to protect these
water lines from freezing.
!
WARNING
If the water in the supply line or water solenoid valve
freezes, the fire suppression system will be
inoperative!!
Water Connections
The water connection is made to the 3/4”-11.5 NH hose
adaptor, which is shipped in the tumbler and must be
installed to the 1/2” N.P.T. water connection, located at the
upper rear of the dryer. A flexible supply line/coupling must
be used in an effort to avoid damaging the electric water
solenoid valve.
NOTE:
The 3/4”-11.5 NH is a standard hose coupling
screw thread. It is not to be confused with 3/4” N.P.T. The
sealing of an NH connection is made with a washer
opposed to the mating threads of an N.P.T. assembly. The
2 thread designs are not compatible.
It is recommended that a filter or strainer be installed in the
water supply line.
IMPORTANT:
Flexible supply line/coupling must be used.
Solenoid valve failure due to hard plumbing connections
will void warranty.
The dryer is to be connected to the water mains using a
new hose set and the old hose set should not be reused.
Optional Manual Bypass
Provisions are made in the dryer’s fire suppression system
for the installation of an optional manual bypass. The
connections for the manual bypass are made at the “cross”
or “four way” fitting located in the outlet supply side of the
water solenoid valve. The manual ball cock shutoff valve
must be located outside of the dryer at a distance from the
dryer where it is easily accessible. The use and connection
of this manual bypass is at the option or discretion of the
owner.
The water connection for the manual bypass is made to the
“cross” or “four way” fitting, which has a 3/8” F.N.P.T. and a
coupling must be used to provide the minimum 1/2-inch
(12.7 mm) supply (feed) line.
Electrical Requirements
No independent external power source or supply connection
is necessary. The 24-volt power to operate the fire
suppression system is accomplished internally in the dryer
(from the dryer controls).
!
WARNING
Electrical power must be provided to the dryer at all
times. If the main electrical power supply to the dryer
is disconnected, the fire suppression system is
inoperative!!
Summary of Contents for ES35/35
Page 24: ...WFR112807 15 06 05 18 ...