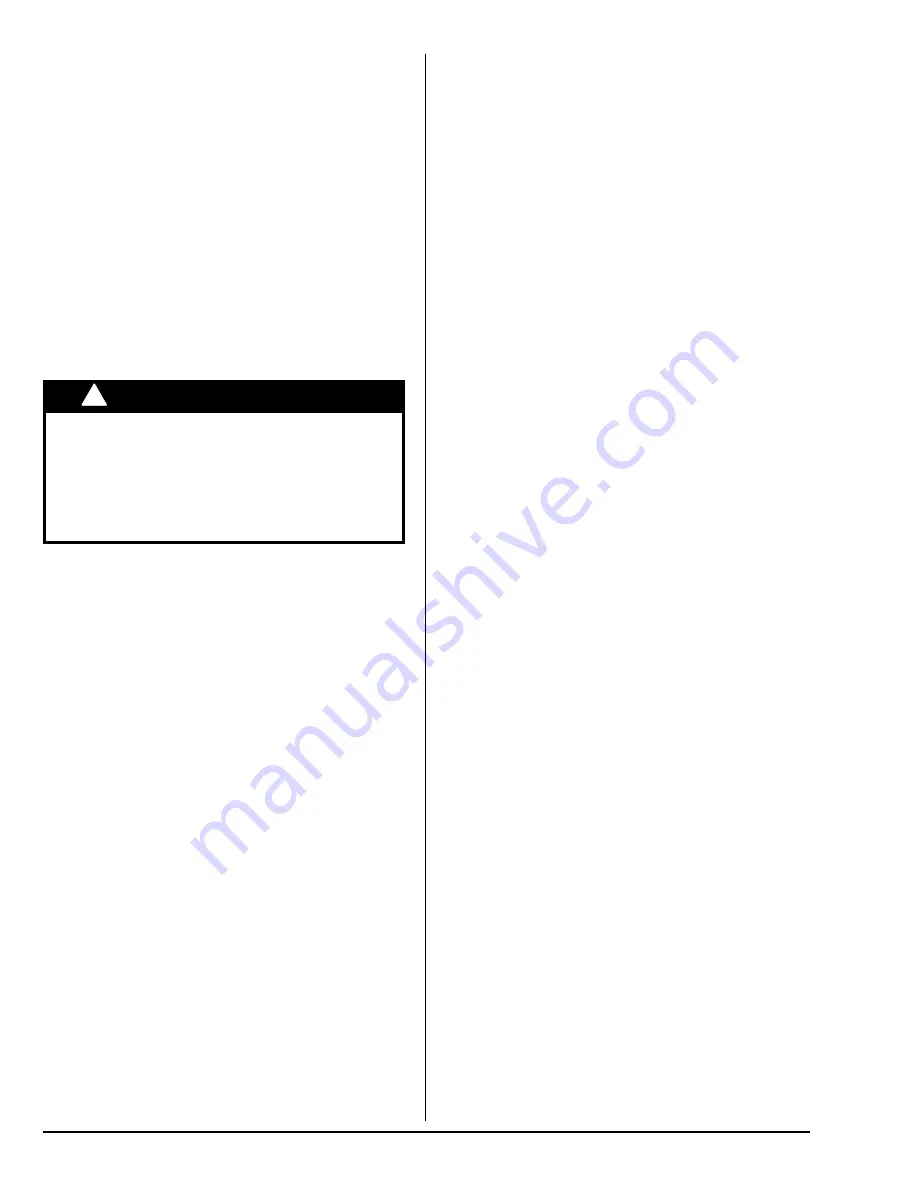
16
American Dryer Corp.
112217 - 4
Gas Pressure Adjustment
Disconnect electrical power to the dryer.
IMPORTANT:
The following procedures must be
performed on both top and bottom tumblers.
To adjust gas valve’s internal regulator, remove the regulator
vent cap, turn the screw clockwise to raise pressure and
counterclockwise to lower pressure.
Gas (burner) pressures are measured with the burner in
operation for all burner adjustment conditions. Therefore
once the necessary adjustments have been made, the dryer
must be operated in a heating cycle to verify that the pressure
is correct. If it is not correct, you must discontinue the power
to the unit and make further adjustments. Repeat these
steps as many times as necessary to achieve the correct
burner pressure. Once the adjustment of the valve is
complete, the vent cap must be replaced and sealed with,
for example, paint to prevent maladjustment by the user.
!
WARNING
(CE Dryers)
This appliance must only be operated with the gas
type indicated on the dryer’s data plate. If the
appliance is converted (gas type changed), a data
plate amendment must be obtained from American
Dryer Corporation.
Conversions done improperly can result in a fire or
explosion!
Gas Pressure Testing
For proper operation, the gas pressure must be correct,
consistent and maintained at the gas pressure rates shown
on page
14. Provisions are made at the gas valve for taking
gas pressure readings.
There are two types of devices used to measure gas
pressure. They are the spring/mechanical type gauge and
the manometer. The use of the spring/mechanical type
gauge is not recommended because they are very easily
damaged and are not always accurate. The preferred type
of gauge is the manometer because it is a simple device to
use and is highly accurate. A manometer is simply a glass
or transparent plastic tube with a scale graduated in inches
or millibars. When it is filled with water and pressure is
applied, the water in the tube rises, showing the exact gas
pressure.
Gas Pressure Test Procedure
Turn gas cock in gas supply line to “OFF” position.
60 Hz dryers: Install pressure tap and attach manometer
(refer to the illustration on page
Turn gas cock to “ON” position.
Start the dryer in Heat Mode and wait for ignition. Gas
manifold pressure should be as shown on page
If the gas pressure needs to be adjusted, refer to “Gas
Pressure Adjustment” on this page.
Once test is complete, turn gas cock to “OFF” position.
Remove manometer. Tighten screw inside the pressure
tap or install plug.
Turn gas cock to “ON” position and check for leaks with
soap solution with main burner “ON.”
Preparation for Operation / Start-Up__
The following items should be checked before attempting
to operate the dryer:
• Read all “CAUTION,” “WARNING,” and “DIRECTION”
labels attached to the dryer.
• Check incoming supply voltage to be sure that it is the
same as indicated on the data label. In the case of 208
VAC or 230/240 VAC, the supply voltage must match the
electric service exactly.
• GAS MODELS – Check to ensure that the dryer is
connected to the type of heat/gas indicated on the dryer
data label.
• GAS MODELS – Be sure that all gas shutoff valves are
in the open position.
• Be sure all back panels (guards) and electric box
covers are in place.
• Be sure the service doors are closed and securely in
place.
• Be sure the lint door/drawer is securely in place.
• Rotate the tumbler (drum) by hand to be sure it moves
freely.
• Check bolts, nuts, screws, terminals, and fittings for
tightness and security.
• Check that the vent is connected to the dryer and is
exhausted to the outdoors.
Preoperational Test __________________
All dryers are thoroughly tested and inspected before leaving
the factory. However, a preoperational test should be
performed before the dryer is publicly used. It is possible
that adjustments have changed in transit or due to marginal
location (installation) conditions. Installer must instruct the
user on how to correctly operate the dryer before leaving.
Turn on electric power to the dryer.
Refer to the Operating Instructions for starting your particular
model dryer.
Gas Dryers
Open all shutoff valves.
When a gas dryer is first started (during initial start-up), it
has a tendency not to ignite on the first ignition attempt.
This is because the gas supply piping is filled with air, so it
may take a few minutes for the air to be purged from the
lines.
NOTE:
During the purging period, check to be sure that
all gas shutoff valves are open.
A gas pressure test should be taken at the gas valve
pressure tap of each dryer to ensure that the water column
pressure is correct and consistent.
NOTE:
Water column pressure requirements (measured
at the pressure tap of the gas valve body) must be
verified.
IMPORTANT:
In most cases there is no regulator provided
in an L.P. dryer. The water column pressure must be
regulated at the source (L.P. tank), or an external regulator
must be added to each dryer.
Summary of Contents for AD222
Page 20: ...ADC Part No 112217 4 05 05 15 ...