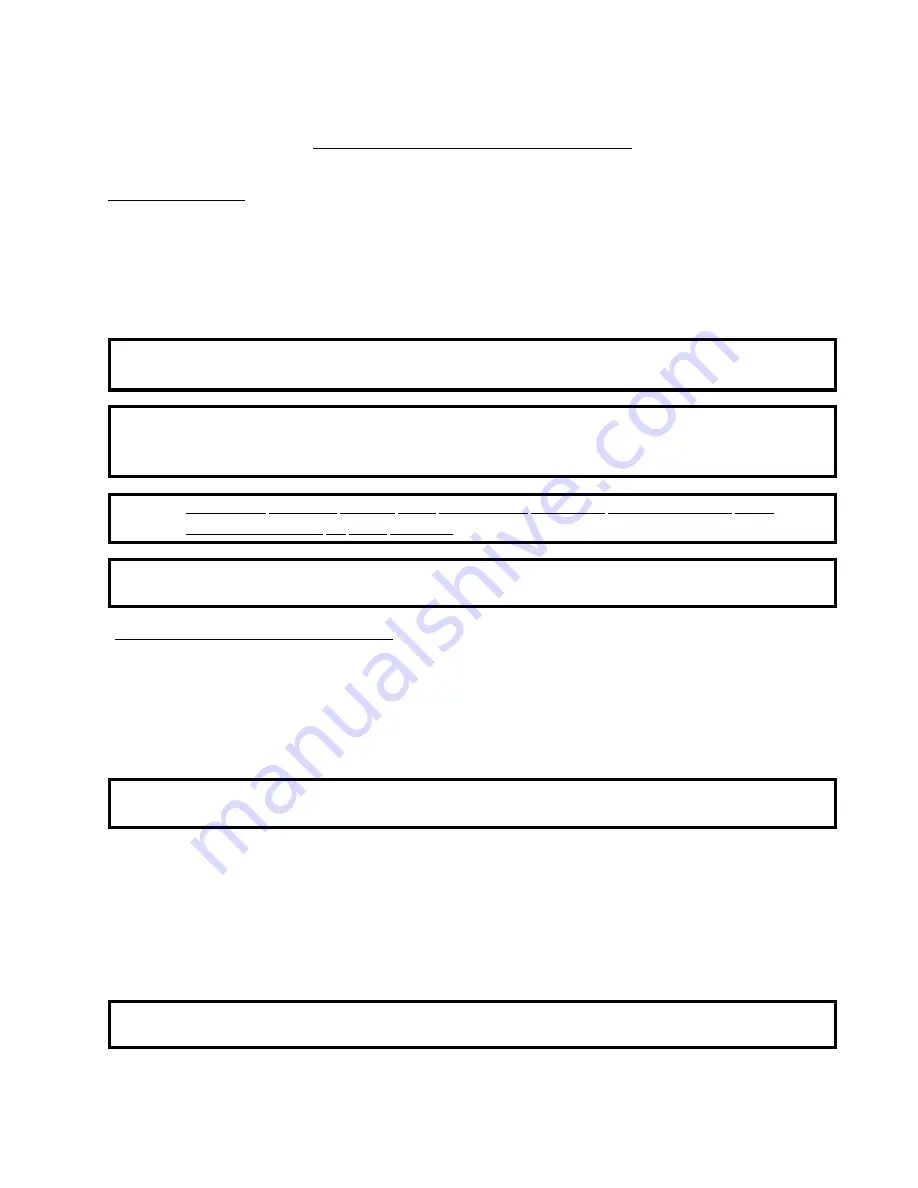
5
SECTION II
ROUTINE MAINTENANCE
A. CLEANING
A schedule
should be
established for periodic inspection, cleaning, and removal of lint from various areas of the
dryer, as well as throughout the duct work system. The frequency of cleaning can best be determined from
experience at each location. Maximum operating efficiency is dependent upon proper air circulation. The
accumulation of lint can restrict this air flow. If the guidelines in this section are met, an
ADC
dryer will provide
many years of efficient, trouble-free, and - most importantly - safe operation.
WARNING: LINT FROM MOST FABRICS IS HIGHLY COMBUSTIBLE. THE
ACCUMULATION OF LINT CAN CREATE A POTENTIAL FIRE HAZARD.
WARNING: KEEP DRYER AREA CLEAR AND FREE FROM COMBUSTIBLE
MATERIALS, GASOLINE, and OTHER FLAMMABLE VAPORS and
LIQUIDS.
NOTE: REMOVE
POWER
FROM
THE
MACHINE
BEFORE
PERFORMING
ANY
MAINTENANCE
IN
THE
DRYER.
NOTE
: Suggested time intervals shown are for average usage which is considered six (6) to eight (8)
operational (running) hours per day.
SUGGESTED CLEANING SCHEDULE
EVERY THIRD or FOURTH LOAD
Clean the lint screen. A clogged lint screen will cause poor dryer performance. The lint screen is located in
the lint drawer in the base of the dryer. Pull out the lint drawer, brush the lint off the lint screen, and remove
the lint. Inspect the lint screen and replace if torn.
NOTE
: The frequency of cleaning the lint screens can best be determined from experience at each
location.
WEEKLY
Open the hinged panels on each side of the tumbler section and remove any lint accumulation from the tumbler
drive motor, drive shafts, gear reducer, drive belts, drive wheels, and drive shaft bearings.
Slide the lint basket all the way out of the dryer and clean any lint accumulation off of the temperature sensor
bracket, which is located above the lint basket.
WARNING: TO AVOID THE HAZARD OF ELECTRICAL SHOCK, DISCONTINUE
ELECTRICAL SUPPLY TO THE DRYER.