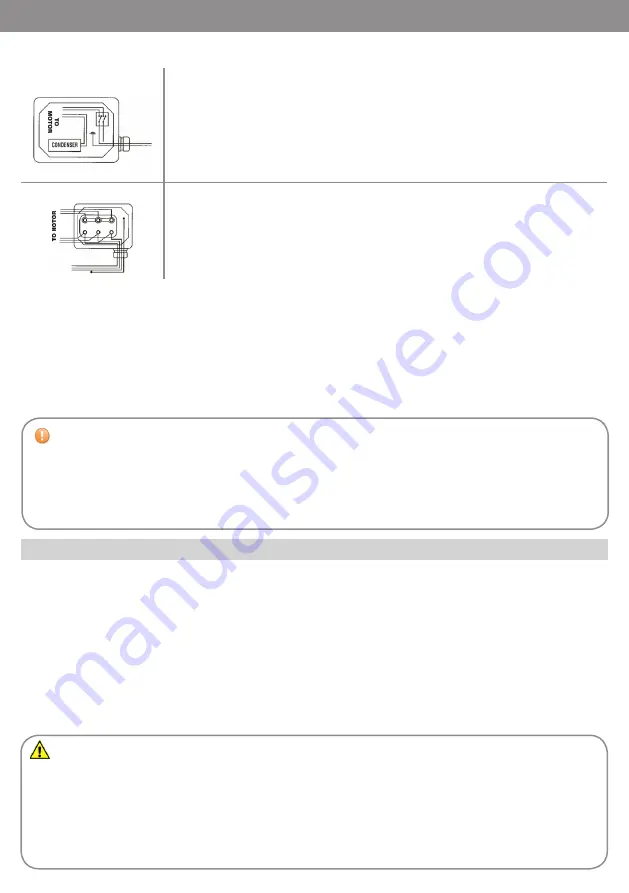
ENGLISH (TRANSLATION OF ORIGINAL INSTRUCTIONS)
WARNINGS! Never leave the filling position to prevent accidental diesel fuel spillage. Do
not start the pump before having connected the suction and discharge pipes. Do not start
or stop the pump by inserting or unplugging any plugs. Do not touch any switches with wet
hands. Avoid direct contact of the diesel fuel with skin or eyes as it may cause harm. Use of
goggles and gloves is recommended.The single-phase motors are fitted with motor protectors
and systems against accidental restart. In the event of a power failure, remember to switch
the pump off and unplug it before restoring it.Work cycles that are continuous or in extreme
5.4 - e
lectrIcal
connectIon
of
the
pump
SINGLE-PHASE MOTORS
Pumps with single-phase motors are supplied with a 2 m cable and plug.
To change the power cable, open the capacitor box cover and follow the connection diagram to the
side.
Single-phase motors are equipped with phase capacitor and double-pole switch.
The capacitor specifications are indicated for each model on the pump’s rating plate.
THREE-PHASE MOTORS
Pumps with three-phase motors are supplied with capacitor box and terminal board.
To connect the electric motor to the power line, open the capacitor box cover and follow the
connection diagram to the side.
For proper installation and electrical maintenance of the system, please follow these instructions:
- make sure the power lines are not live when installing or carrying out maintenance operations on the
system
- use cables with minimum section, rated voltages and type of installation suitable for the system’s
specifications
- make sure the three-phase motors are rotating in the right direction
- always connect the pump’s earth terminal to the electricity grid’s earth line.
6 - INTENDED USE
6.1 - p
relImInary
checks
and
start
-
up
After ensuring there is diesel fuel in the suction tank, that all pipes and components on the hydraulic
line are in good condition and properly sealed, and the nozzle is closed, the pump can be started. After
inserting the nozzle into the filling hole, switch the pump on, gradually release the nozzle lever and start
transferring the diesel fuel. When you have finished filling, close the nozzle and switch the pump off. If you
are using an automatic nozzle, it will automatically close as soon as you have finished filling.
CAUTION! The pumps are provided without safety devices such as fuses, motor protectors,
systems against accidental restart after a power failure. Even the switch, if any, will only start/
stop the pump and can in no way replace a suitable circuit breaker. It is therefore the direct
responsibility of the installer to connect the pump to the main electrical panel in compliance with
the regulations in force in the country of use.