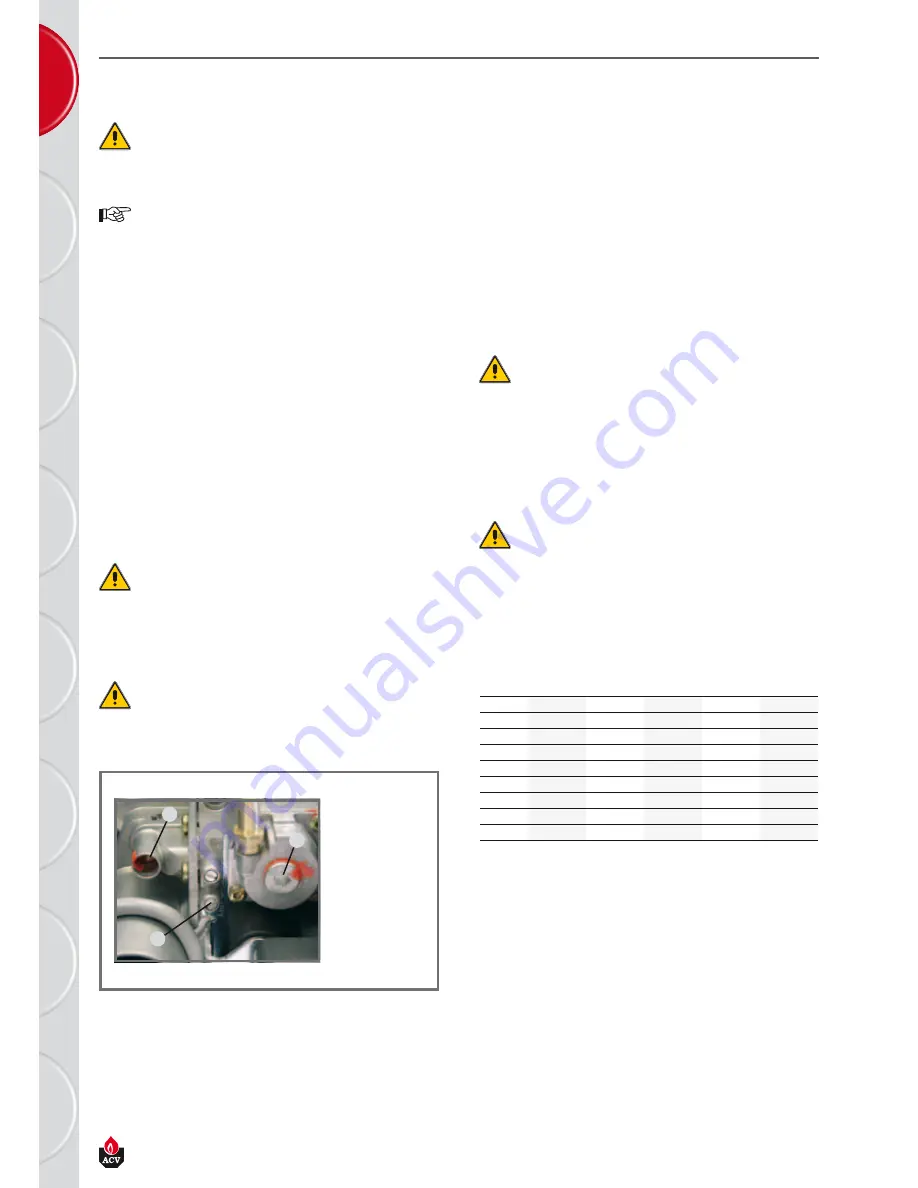
EN • 22
664Y4500 • D
E
N
FR
R
U
P
L
DE
IT
ES
N
L
CommIssIoNING aND maINtENaNCE
commIssIonIng tHe sYstem
The DHw tank (secondary) must be vented and pressurised
before filling and pressurising the heating circuit (primary).
The two circuits, DHw and heating, must be filled prior to
using the appliance.
- Fill the DHW tank slowly and purge it by opening the hot water outlet.
Purge all the outlets and make sure there are no leaks in the domestic hot
water system.
- Fill the heating installation to at least 1.5 bar using the boiler’s filling valve.
Fill the system slowly. Check that the automatic air vent is operating. Check
for leaks in the central heating system.
- Purge the charging pump and check that it rotates.
- Open the gas valve, purge the pipe and check for leaks in the system.
- Ensure the condensate trap is correctly fitted underneath the boiler.
- Connect the power cable to the boiler via the terminal provided and switch
on the appliance. Where appropriate, put the room thermostat at its
highest setting. The boiler starts up. Check the gas pressure and allow the
boiler to heat up for a few minutes.
Set the boiler to high power mode and check the CO
2
. (see table of technical
characteristics). Next, set the boiler to minimum power mode and check
the CO
2
(see table of technical characteristics).
- Set the central heating and hot water temperatures according to the values
indicated in the instructions for use.
- Bleed the central heating system again, and, if required, fill to reach the
desired pressure.
- Make sure that the heating system is properly balanced, and, if required,
adjust the valves to prevent certain circuits or radiators from getting a flow
rate that is far above or below the set rate.
The diameter of the condensate discharge pipe cannot be
reduced. The pipe must never be obstructed.
cHeckIng tHe settIngs
Specific regulation in Belgium for HeatMaster® 25.
The CO
2
, gas flow, air flow and air/gas supply parameters are
factory preset and cannot be changed.
- Check if the parameters are set to meet the user’s needs.
- Checking the boiler’s settings: only an ACV-trained installer or the ACV
maintenance department can perform this task.
- Set the appliance to maximum power mode.
- Check the dynamic gas pressure on the gas valve.
(see figure below ref.1) This must be at least 18 mbar.
Let the appliance heat for a few minutes until it reaches at least 60 °C. Check
the CO
2
setting of the appliance using a measuring instrument. The optimal
value is indicated in the table of technical characteristics. To increase the
CO
2
value, turn the venturi screw counter-clockwise , and turn it clockwise
to decrease this value (see diagram below, ref. 2).
Next, switch the appliance to minimum power mode. Let the appliance
stabilize for a few minutes. Check the CO
2
value. It should be either equal to
the value at full power or a maximum of 0.5 % less than it. If you observe a
significant deviation, please contact ACV’s maintenance department.
boIler maIntenance
ACV recommends that you have your boiler inspected,
and cleaned, if required, at least once a year.
Disconnect the electrical power supply before undertaking any work on it.
- Check that the condensate trap is not clogged, fill it as required and check
for leaks.
- Check that the safety valves are in good working order.
- Vent the whole system and refill the appliance if required to 1.5 Bar.
In the case of repeated fills, contact your installer.
- Check the boiler’s combustion in maximum power mode.
If this value is very different from the original setting it may indicate an
obstruction in the air intake ducts or flue gas exhaust pipes, or that the
exchanger is clogged.
temperature sensor resIstance table
REF. 3:
The OFFSET
setting of the gas
valve is set at the
factory and sealed.
It cannot be
modified.
2
1
3
T° [°C]
R
Ω
T° [°C]
R
Ω
T° [°C]
R
Ω
- 20
98200
25
12000
70
2340
- 15
75900
30
9800
75
1940
- 10
58800
35
8050
80
1710
- 5
45900
40
6650
85
1470
0
36100
45
5520
90
1260
5
28600
50
4610
95
1100
10
22800
55
3860
100
950
15
18300
60
3250
20
14700
65
2750