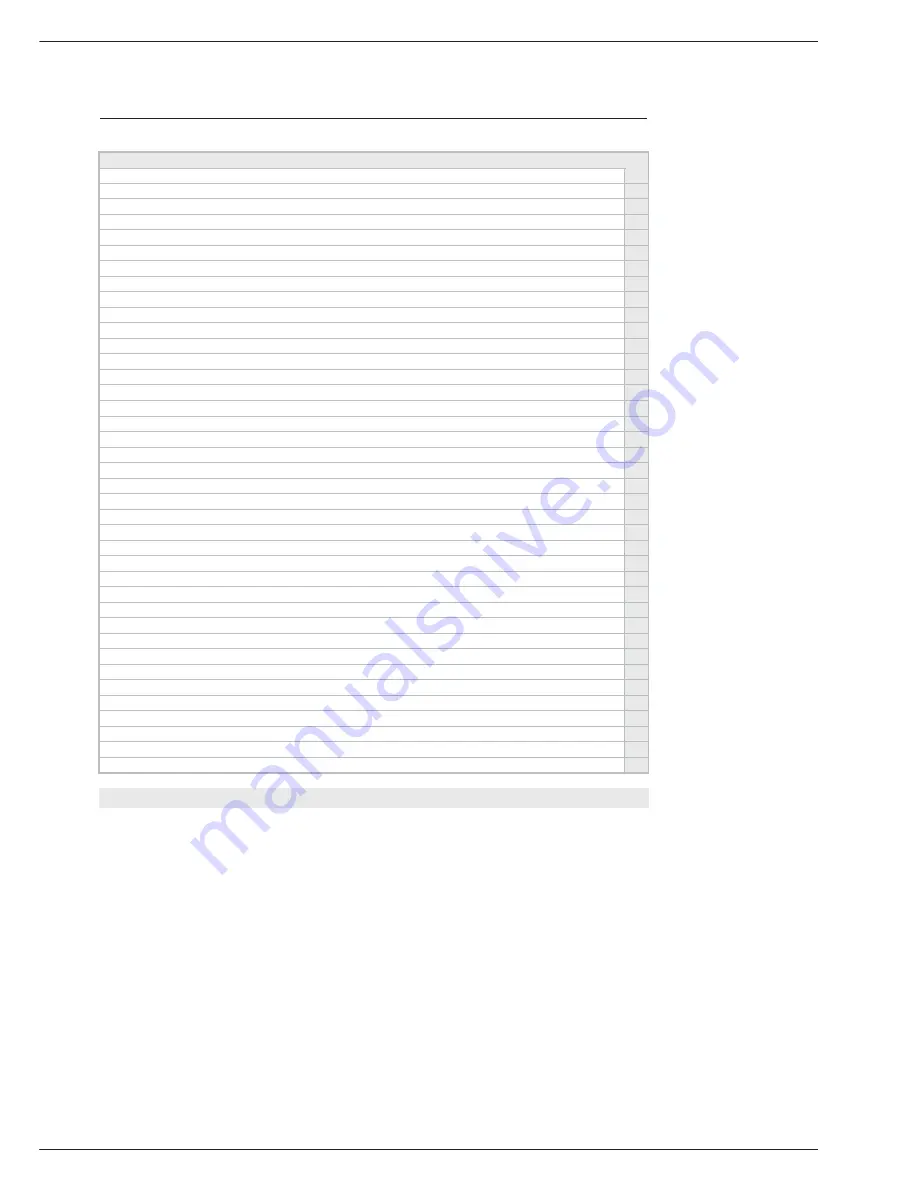
19
BURNER CHARACTERISTICS
Corrective measures
Fit lining in the chimney
1
Increase the boiler T°
2
Check and clean the chimney
3
Check and clean the chimney
4
Comply with local requirements governing boiler room ventilation
5
Clean the burner and the boiler
6
Clean the burner and the boiler
7
Set the room thermostat to the required temperature
8
Free the pump or replace it
9
Move the switch to the Winter position or replace it
10
Properly fill and vent the system and the boiler
11
Open the radiator taps or adjust the thermostat valves
12
Properly fill and vent the system and the boiler
13
Check that the pipes and the meter are suitable for the system
14
Check that the pipes and the meter are suitable for the system
15
Replace the boiler thermostat/potentiometer
16
Ensure that the electrical system complies with regulations
17
Replace the fuses and look for the cause of the problem
18
Properly fill and vent the system and the boiler
19
Adhere to the performance data as indicated by ACV
20
Adhere to the performance data as indicated by ACV
21
Set the thermostat to the required temperature or replace it
22
Replace the Summer/Winter switch
23
Replace the main switch
24
Replace the NTC sensor
25
Replace the boiler thermostat/potentiometer
26
Abnormal situation
27
Replace the p.c.b.
28
Replace the p.c.b. but look for the cause of the malfunction
29
Replace the fan
30
Replace the p.c.b. if the fan turns but does not send a PWM signal
31
Replace the electrode or set it correctly
32
Replace the electrode or set it correctly
33
Insert the connectors correctly
34
Replace the gas valve and set it up according to the setting parameters
35
Replace the p.c.b.
36
Replace the boiler thermostat/potentiometer
37
Fill and vent the system and the boiler
38
Insert the NTC sensor in the pocket correctly
39
ACV provides details of training courses on the maintenance of BG 2000 burners
TABLE OF CORRECTIVE MEASURES