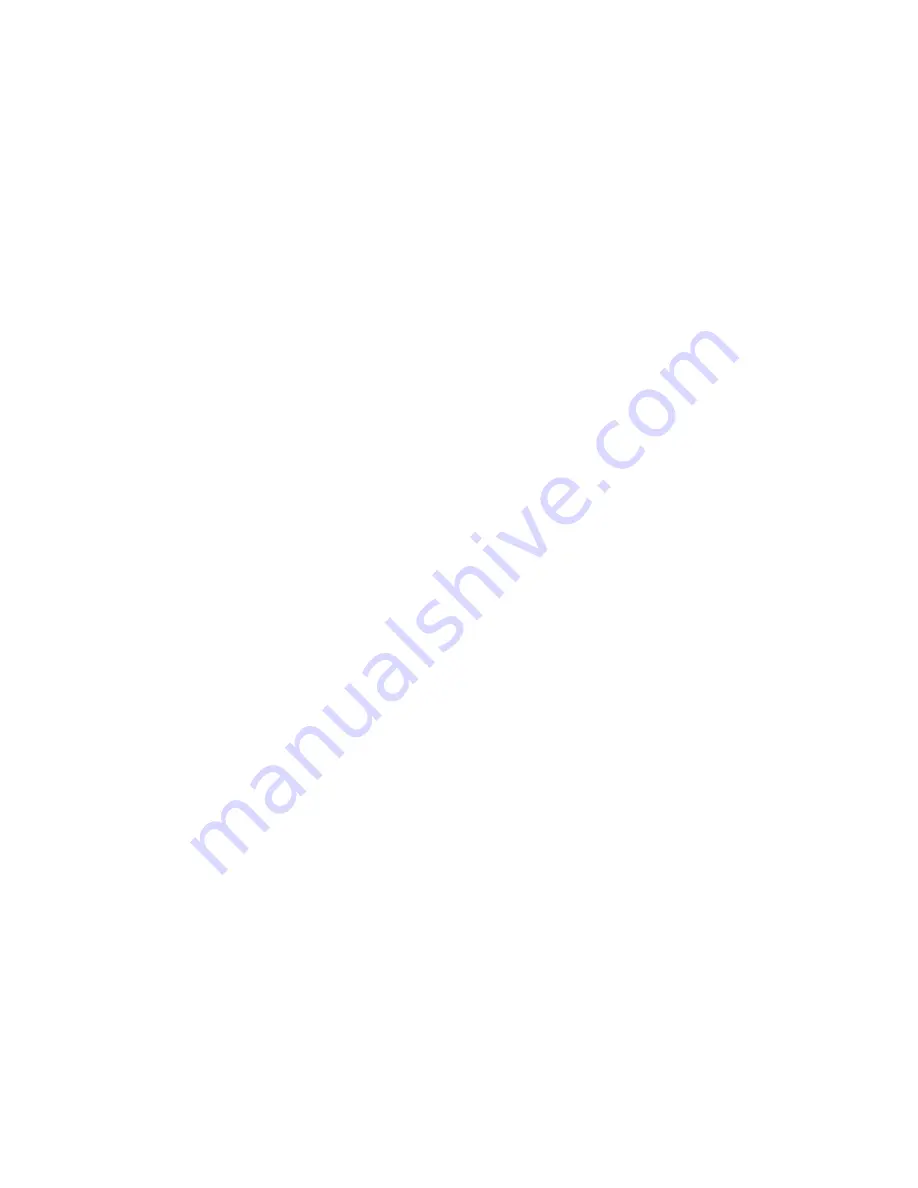
Reversing Flange and the Reversing Shaft. This is how the
Ribbon reverses.
VII.PLATEN INSTALLATION AND TRIMMING
Sometimes it is necessary to install a new Platen when
changing from three wheels to four wheels or when installing
a Year or Symbol Wheel. Remove old Platen from Hammer.
Before installing new Platen, apply adhesive substance to
Hammer. Beveled edge of Platen should be inserted into the
Hammer towards the top. Insert new Platen in Hammer
making sure Platen is in position to hit all Typewheels. Having
the Platen in the correct position, we can now press or hammer
Platen to be sure Platen is seated in Hammer. Manually push
in on Hammer and release; this will transfer typewheel print to
Platen. With a razor blade, remove all Platen around the
minute character. Take a sample print on time card. If print
quality is not adequate, the Platen may need to be filed or
ground flat.
VIII.
ELECTRICAL INFORMATION
One wire of the AC line (Terminal 4) connects to one AC
terminal on the full wave bridge Rectifier. The other AC wire
(Terminal 2) will connect to the Normally Open (NO) Termi-
nal of the Print (Left Card) Microswitch, leave the Print (Left
Card) Microswitch thru the Common (COM) Terminal and
proceeds to the Normal Open (NO) Terminal of the Cancella-
tion (Right Card) Microswitch thru the Common (COM)
Terminal and connect to the other AC terminal of the Rectifier.
The Print Solenoid is connected to the + and - terminals on the
Rectifier (one wire on the Solenoid to +; the other wire to -).
Always be sure Left and Right Card Microswitches are
connected to AC. NOTE: The Microswitches are connected in
series — (both Microswitches have to close to complete the
circuit for recorder to print).
IX. SERVICE TIPS
A. Losing time (minutes).
1.
Check 1 RPM motor with second hand on watch —
Minute Drive Lever should operate at the same
second for 4 or 5 minutes.
2.
Binding Minute Wheel against Drive Gear.
3.
Binding Hour Reduction Gears.
4.
Minute Cam loose on motor — Set Screw loose in
Drive Gear.
5.
Minute Detent out of adjustment.
6.
Check parts for lubrication.
7.
Ask if they experienced a power failure recently.
B. Gaining time (minutes).
1.
Minute Feed Pawl backing up two (2) teeth.
2.
Minute Feed Pawl and Detent Pawl out of adjust-
ment. When this adjustment is incorrect, the Hour
Cam on Minute Wheel wears the point off Hour Cam.
On the 59th minute, the Minute Feed Pawl comes out
of the 60-tooth Ratchet. At this time the Minute
Wheel can be rotated by the Hour Follower Level.
This will account for one (1) minute fast. Then the
recorder will take on (1) normal minute.
C.
Losing time (hours).
1.
Hour Ratchet binding on Typehead Rear Plate.
2.
Too much side play in Hour Follower Lever allowing
Hour Feed Pawl to get off Hour Ratchet.
3.
Day-Date Lever binding Hour Ratchet.
4.
Hour Detent binding — not enough clearance.
D. Gaining time (hours - Typewheels one or more hours
ahead of clock face).
1.
When Hour Typewheel is at 12:00 midnight, check
clearance between Day-Date Cam and Cam Follower
of Day-Date Lever. There should be 1/16" clearance
between Cam and Follower at midnight. Check Hour
Ratchet for adjustment and alignment. It may be
necessary to remove Day-Day Cam and grind about
1/16" for correct clearance.
2.
Binding Hour Detent Pawl.
3.
Hour Pawl Stop Screw loose — causing hours to
advance two hours at a time.
4.
Set screws in Hour Ratchet loose, causing Hour
Wheel to spin freely and appear to gain time.
E.
Day or Date not changing.
1.
Too much side play in Day-Date Follower Lever.
2.
Day-Date Detent binding — not enough clearance.
3.
Set Screws in Day-Date Ratchet loose, causing Day-
Date Wheel to spin freely.
4.
Day-Date Pawl Stop Screw too tight, not allowing
Pawl to advance.
5.
Clock may be set 12 Hours off, so Day-Date would
appear to advance at noon instead of midnight.
F.
Light or weak print.
1.
Ribbon worn out or not reversing.
2.
Ribbon Guide loose.
3.
Hammer Shaft and associated parts dry — need oil
G. Not Printing.
1.
Card Receiver out of adjustment — too wide for card.
2.
Rectifier or Solenoid burned out.
3.
Microswitch burned out.
4.
Bad connection at Terminal Block or Microswitch.
H. Ribbon not reversing.
1.
Ribbon Drive Ratchet loose on Ribbon Shaft.
2.
Ribbon Drive Arm loose on Hammer Shaft.
3.
Ribbon Feed and Detent Spring broken.
4.
Gears loose on Ribbon Drive Shaft on Ribbon Spool
Shaft.
5.
Ribbon Reverse Flange loose or out of adjustment.
I.
Platen Replacement. SEE PREVIOUS TEXT.
5
Summary of Contents for 200
Page 12: ...9 9 MODEL 200 DIAL MOUNTING PLATE ASSEMBLY ...
Page 14: ...MODEL 200 CARD GUIDE FRAME ASSEMBLY ...
Page 16: ...MODEL 200 TYPEHEAD ASSEMBLY 5 WHEEL ...
Page 18: ...MODEL 200 TYPEHEAD DIAL DRIVE ASSEMBLIES Including Minute Impulse and Rechargeable Options ...
Page 20: ...MODEL 200 SIDE FRAME ASSEMBLY ...
Page 22: ...MODEL 200 FINAL ASSEMBLIES ...
Page 24: ...MODEL 200 COVER ASSEMBLY ...