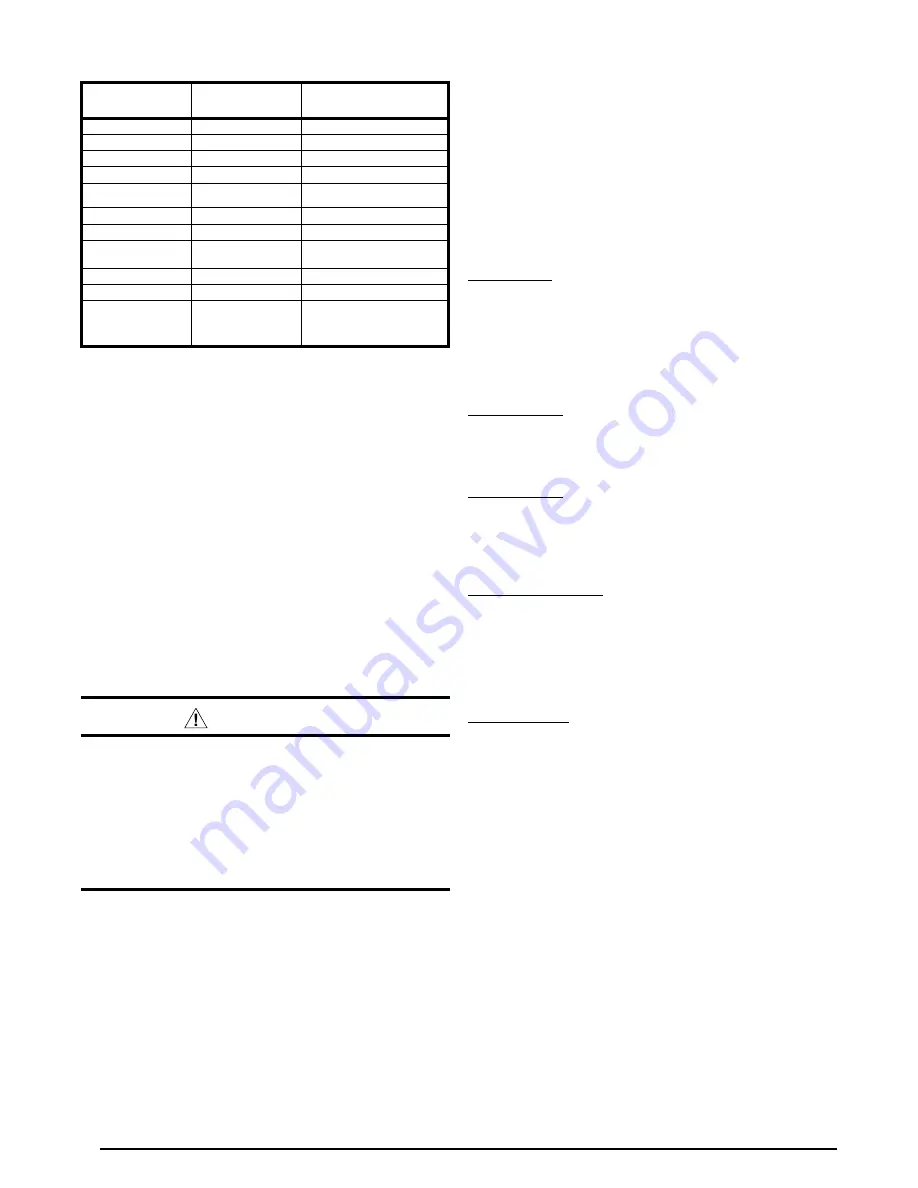
10
STARTUP & ADJUSTMENTS
Pre-Start Checklist
The following check list should be observed prior to starting
the unit.
√
Is the unit level? Unit should be level or slightly slanted toward
the drain for proper condensate drainage.
√
Is the unit installed with the proper clearances as listed on
√
Is the wiring correct according to the wiring diagram and
electrical codes?
√
Are all the wiring connections tight? Check the condenser fan
to make sure it turns freely.
√
Is the overcurrent protection properly sized?
√
Is the thermostat wired correctly? Is it installed in a proper
location?
√
To achieve rated capacity and efficiency the compressor must
be exposed to refrigerant for at least 24 hours prior to running
and then must be run for a minimum of 12 hours.
Start-Up Procedure
CAUTION:
If the unit is equipped with a crankcase heater,
allow 24 hours prior to continuing the start up
procedures to allow for heating of the refrigerant
compressor crankcase. Failure to comply may
result in damage and could cause premature
failure of the system. This warning should be
followed at initial start up and any time the power
has been removed for 12 hours or longer.
The control circuit consists of an anti-short cycle timer that will
not let the compressor re-start before 5 minutes have elapsed.
1. Set the system mode to OFF and the temperature mode to
its highest setting.
2. Turn power on at the disconnect switch.
3. Set the system mode to ON or COOL.
4. Set the temperature mode below room temperature. Verify
that the indoor blower, outdoor fan, and compressor energize
and the cooling function starts.
5. Verify the discharge air grilles are adjusted and the system
air is balanced.
6. Verify the duct work has no air leaks.
7. Verify the condensate drain is installed correctly and functions
properly.
8. Set the temperature mode above room temperature. The unit
should stop.
9. Instruct the homeowner on unit and thermostat operation and
filter servicing.
Air Circulation
Leave the thermostat system mode on OFF, and set the fan
mode to ON. Blower should run continuously. Check the air
delivery at the supply registers and adjust register openings for
balanced air distribution. Examine ducts for leaks or obstruction
if insufficient air is detected.
Set the thermostat fan mode to AUTO. The blower should stop
running.
System Heating
Set the thermostat system mode to HEAT and the fan mode to
AUTO. Change the thermostat temperature selector above the
existing room temperature and check for the discharge of warm
air at the supply registers.
System Cooling
Set the thermostat’s system mode to COOL and the fan mode to
AUTO. Change the thermostat temperature selector below the
existing room temperature. Allow the cooling system to operate
for several minutes and check for the discharge of cool air at
the supply registers.
Short Cycle Protection
The control circuit is equipped with a time-delay feature for
protection against short cycling. With the system operating in
the cooling mode, gradually raise the thermostat temperature
setting until the whole system de-energizes. Immediately lower
the thermostat temperature to the original setting and verify that
the indoor blower is energized. After approximately 5 minutes
the compressor and the outdoor fan will energize.
Emergency Heat
(Available only when Electric heat is supplied)
1. Set the thermostat’s system mode to EM HT and the fan
mode to AUTO (intermittent air) or ON (continuous air).
2. Set the thermostat’s temperature selector above the existing
room temperature and check the following:
• The thermostat auxiliary heat is indicated as ON.
• The compressor and the fan should not run; low voltage
circuit remains energized.
• The blower runs according to the thermostat’s fan mode
setting.
Forced Defrost Mode (Field Test)
• When the
TEST
terminals are shorted for more than 3 seconds,
with the
Y1
input active and pressure switches closed, the
ACST will be eliminated and the compressor contactor output
energizes. The control will be placed into a forced defrost
mode.
NOTE:
The coil temperature sensor does not need to be cold
when the unit is forced into defrost.
• If the short across the TEST pins exist, the unit will stay
in DEFROST as long as the short remains or until the
TERMINATE TIME is reached (11 minutes). This will happen
regardless of coil temperature.
Table 2. Control Board Status Indicators
STATUS
INDICATOR
STATUS
TYPE
DIAGNOSTIC
DESCRIPTION
C1
Operating Status Cooling, 1st Stage
H1
Operating Status Heating, 1st Stage
SC
Operating Status Anti Short Cycle Timer
dF
Operating Status Defrost
_.
Operating Status Power on, no call for
operation
01
Fault
Pressure Switch, low
02
Fault
Pressure Switch, high
03
Fault
Temperature Sensor,
Ambient
04
Fault
Temperature Sensor, Coil
05
Fault
Board
dF
(flashing)
Input Error
Forced defrost - test
short applied longer than
11 minutes