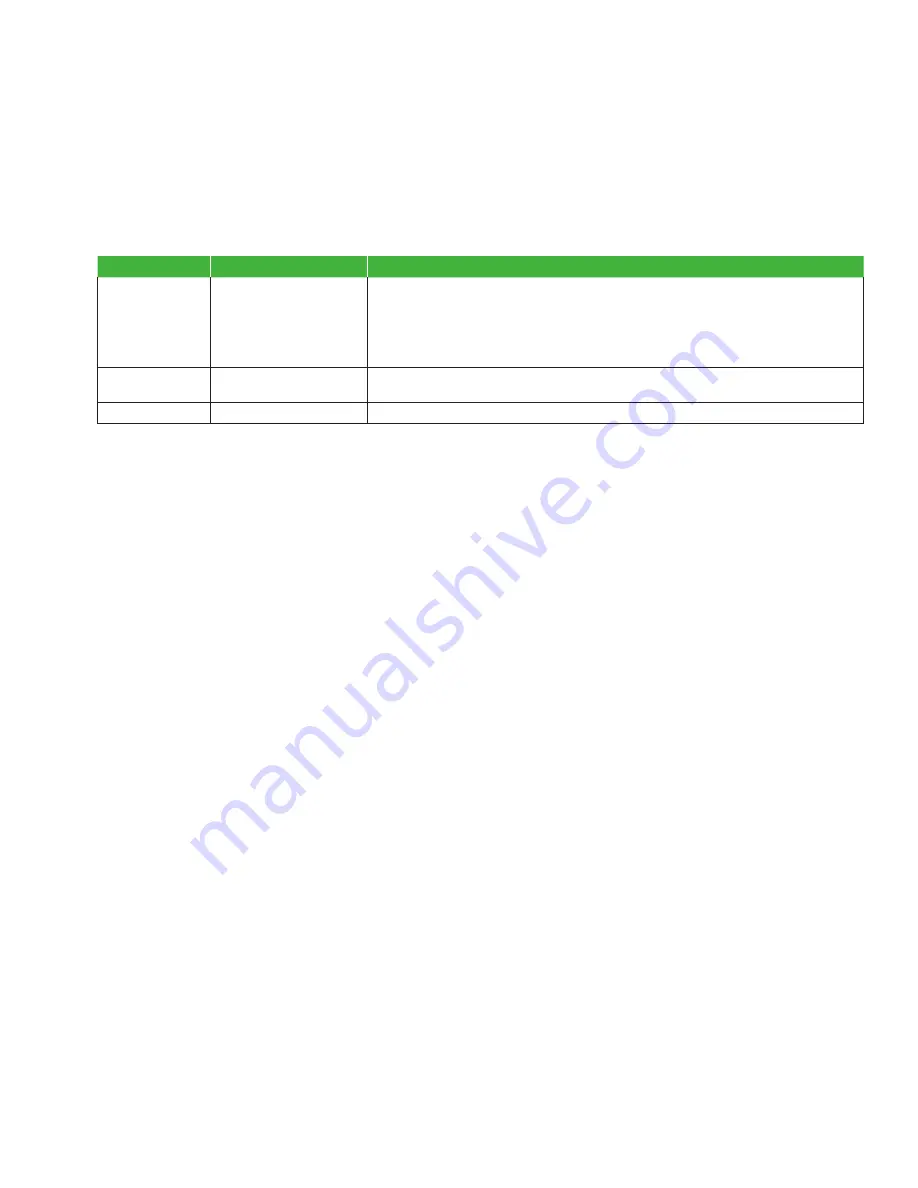
PerfectSpeed
®
Motor and User Interface Troubleshooting
Motor Is Not Running
If the PerfectSpeed
®
motor with User Interface isn’t running, perform the following checks:
1. Ensure that both the PerfectSpeed
®
motor and User Interface have proper line voltage for intended application.
2. Turn the User Interface on-board potentiometer fully clockwise (100% demand) and check to see if the motor runs.
3. If 0-10 VDC input is in use, disconnect the external input from the User Interface and perform Check 2.
4. Check the digital read- out of User Interface for an error code:
Error Code
Reason
Action
E1
No Communication
Remove power from both the PerfectSpeed
®
motor and User Interface for four (4)
minutes, then reconnect power and test again.
Check the communication cable connection between the PerfectSpeed® motor and
User Interface.
Check the continuity of communication cable (pin 1-1, pin 2-2 pin 3-4, and pin 4-3).
E2
Low Voltage
This is a reading from the PerfectSpeed
®
motor itself. Ensure that there is at least 71
VAC (for 115 VAC applications) or 142 VAC (for 230 VAC applications).
E3
Not a NMC Motor
Connect to a NMC motor.
Check 2: Electrical Troubleshooting
1. Disconnect or remove power to the equipment being
serviced and allow four (4) minutes for the capacitors to
discharge any residual voltage.
2. Check the rotation and speed of the motor. Determine if
the motor can spin freely by hand without effort or assisted
means. If any binding occurs, replace the motor and control
unit.
3. Determine whether the system is wired for 120 VAC power
or 240 VAC power.
4. Disconnect the power cord from the connector on the
control unit. Inspect the power cord for bent, damaged, or
recessed wires and terminals.
5. Disconnect or remove AC power to the equipment serviced
and allow four (4) minutes for the capacitors to discharge
any residual voltage.
6. Proceed to Check 3.
Check 3: Motor Verification
1. Disconnect or remove AC power to the equipment serviced
and allow four (4) minutes for the capacitors to discharge
any residual voltage.
2. Make sure that the motor shaft spins freely by hand without
effort in both directions.
3. DC motors can have a jump filling when rotating this is
perfectly normal, if motor does not rotate at all motor needs
to be replaced.
Final Checks of the Motor
1. Check the mounting and fastening of the motor and control
unit. Make sure the motor and the control unit are securely
attached together and mounted tightly in the system.
2. Check the control unit connectors. Inspect for shorts,
detached wiring, or loose connections.
3. Check the motor and verify the rotation of the driven load.
Make sure it spins freely by hand in both directions without
effort or assisted means.
4. Check all circuit breakers.
12