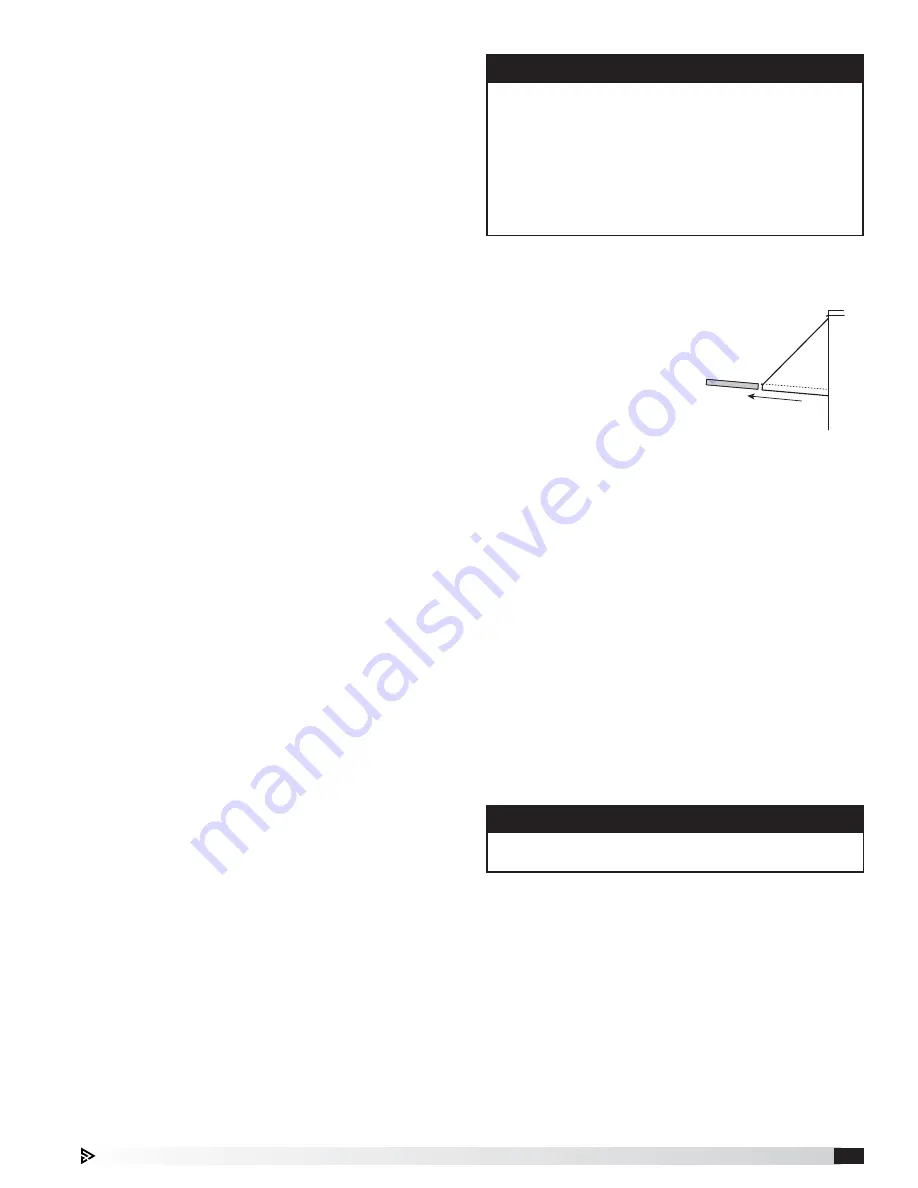
Packaged Rooftop Ventilator
29
Maintenance Procedures:
Lubrication
- Check all moving components for
proper lubrication. Apply lubricant where required.
Any components showing excessive wear should be
replaced to maintain the integrity of the unit and ensure
proper operation.
Dampers
- Check all dampers to ensure they open and
close properly and without binding. Backdraft dampers
can be checked by hand to determine if blades open
and close freely. Apply power to motorized dampers to
ensure the actuator opens and closes the damper as
designed.
Gas Furnace
- Maintain furnace in accordance with
instructions in the Indirect Gas-Fired Heat IOM shipped
with this unit.
Fan Motors
- Motor maintenance is generally limited
to cleaning and lubrication. Cleaning should be limited
to exterior surfaces only. Removing dust and grease
buildup on the motor housing assists proper cooling.
Never wash-down the motor with high pressure
spray. Greasing of motors is only intended when
fittings are provided. Fan motors typically have two
grease fittings. Each motor manufacturer has different
lubrication schedules for different models. Go to the
motor manufacturer’s website and download their
maintenance requirements.
Do not over-lubricate
motors or use an incompatible grease.
Many
fractional motors are permanently lubricated for life and
require no further lubrication.
Fan Wheel and Fasteners
- Wheels require very little
attention when moving clean air. Occasionally oil and
dust may accumulate on the wheel causing imbalance.
When this occurs, the wheel and housing should be
cleaned to assure smooth and safe operation. Inspect
fan impeller and housing for fatigue, corrosion, or wear.
Routinely check all fasteners, set screws and locking
collars on the fan, bearings, drive, motor base and
accessories for tightness. A proper maintenance
program will help preserve the performance and
reliability designed into the fan.
Internal Filter Maintenance
- The unit will typically be
provided with 2-inch thick pleated paper filters in the
airstream. These filters should be checked according
to a routine maintenance schedule and replaced as
necessary to ensure proper airflow through the unit.
Replacement filters shall be of same performance and
quality as factory installed filters. Filter must be pleated
design with integral metal grid. Two acceptable filter
replacements are Aerostat Series 400 or Farr 30/30®.
Filters upstream of the coil should be checked regularly.
If the filters are dirty, they should be cleaned or
replaced. It is important the filters stay clean to maintain
desired airflow.
WARNING
REFER TO GENERAL SAFETY INFORMATION
Do not operate this unit without the filters and
birdscreen installed. They prevent the entry of foreign
objects such as leaves, birds, etc.
Do not remove access panels or other unit
components while standing on a ladder or other
unsteady base. Access panels and unit components
are heavy and serious injury may occur.
Coil Maintenance
- Coils must be cleaned to maintain
maximum performance. Check coils once per year
under normal operating conditions and if dirty, brush
or vacuum clean. Soiled fins reduce the capacity of the
coil, demand more energy from the fan and create an
environment for odor and bacteria to grow and spread
through the conditioned zone. High pressure water
(700 psi or less) may be used to clean coils with a fin
thickness over 0.0095 inches thick.
TEST THE SPRAY
PRESSURE
over a small corner of the coil to determine
if the fins will withstand the spray pressure.
For coils with fragile fins or high fin density, foaming
chemical sprays and washes are available. Many coil
cleaners use harsh chemicals, so they must be used
with caution by qualified personnel only. Care must be
taken not to damage the coils, including the fins, while
cleaning.
Caution: Fin edges are sharp!
External Filter Maintenance
- Aluminum mesh, 2-inch
thick filters are located in the supply weatherhood (if
the weatherhood option was purchased). These filters
should be checked and
cleaned on a regular basis
for best efficiency. The
frequency of cleaning
depends upon the
cleanliness of the incoming
air. These filters should be
cleaned by rinsing with
a mild detergent in warm
water prior to start-up.
Filter
Outdoor Air Intake Hood
Mesh Filter Access
WARNING
Biological hazard. May cause disease. Cleaning
should be performed by qualified personnel.
Drain pans in any air conditioning unit will have some
moisture in them, therefore, algae and other organisms
will grow due to airborne spores and bacteria. Periodic
cleaning is necessary to prevent this buildup from
plugging the drain and causing the drain pan to
overflow. Inspect twice a year to avoid the possibility
of overflow. Also, drain pans should be kept clean to
prevent the spread of disease. Cleaning should be
performed by qualified personnel.