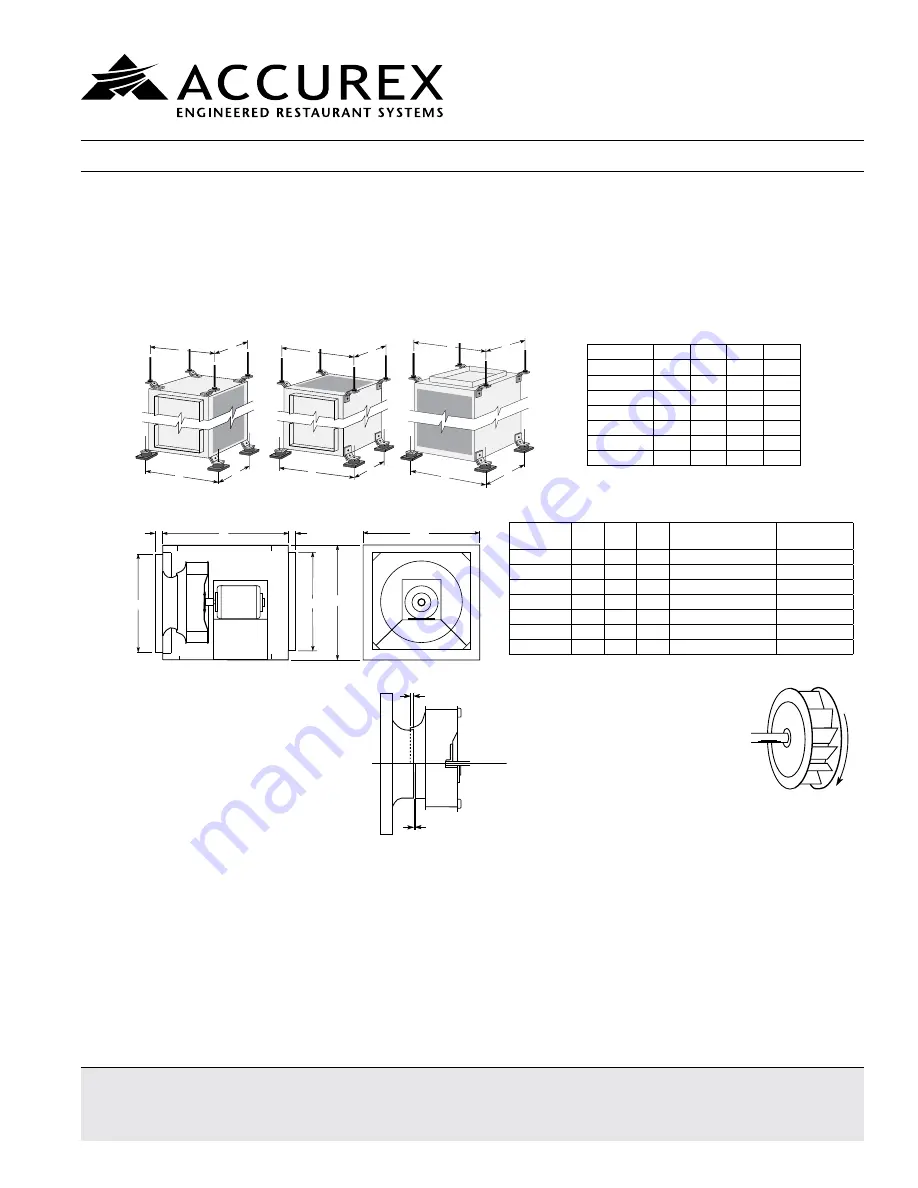
Maintenance
Motor maintenance is generally limited to cleaning and lubrication (where applicable). Cleaning should be limited to
exterior surfaces only. Removing dust buildup on motor housing ensures proper motor cooling. Greasing of motors
is only intended when fittings are provided. Many fractional motors are permanently lubricated and should not be
lubricated after installation. Motors supplied with grease fittings should be greased in accordance with manufacturer’s
recommendations. With motor temperatures under 104ºF (40ºC), the grease should be replaced after 2000 hours of
running time as a general rule.
Wheels require very little attention when moving clean air. Occasionally, oil and dust may accumulate causing
imbalance. When this occurs, the wheel and housing should be cleaned to ensure smooth and safe operation.
All fasteners should be checked for tightness each time maintenance checks are performed prior to restarting unit.
A proper maintenance program will help these units deliver years of dependable service.
Unit Size
A
B
C
D
60-75
10
5
⁄
8
16
3
⁄
4
14
1
⁄
2
8
7
⁄
8
80-95
13
1
⁄
4
19
3
⁄
4
17
1
⁄
2
11
7
⁄
8
100
18
5
⁄
8
21
3
⁄
4
19
1
⁄
2
13
7
⁄
8
120
18
5
⁄
8
23
3
⁄
4
21
1
⁄
2
15
7
⁄
8
130
18
5
⁄
8
25
3
⁄
4
23
1
⁄
2
17
7
⁄
8
140
19
1
⁄
2
27
3
⁄
4
25
1
⁄
2
19
7
⁄
8
160
23
1
⁄
2
31
28
1
⁄
2
22
7
⁄
8
All dimensions are in inches.
Vibration Isolator Dimensional Data
C
A
A
C
Ac
ces
s
Pa
nel
B
A
A
Access Panel
B
D
D
B
B
Access Panel
Fig. 1
Pre-Starting Checks
Check all fasteners for tightness. The
wheel should rotate freely and be aligned
as shown in Fig. 3. Wheel position is
preset and the unit tested at the factory.
However, movement may occur during
shipment, and realignment may be
necessary. Centering (height alignment)
may be accomplished by loosening the set
screws in the wheel and moving the wheel
to desired position.
Overlap 1/4 in.
Gap 1/8 in.
XID
100-160
XID
60-95
Fig. 3
PN 470389
Installation
Move fan to desired location and determine position of access panels, discharge, and motor. Make sure inlet and
outlet have at least 2.5 times the wheel diameter (duct diameter) before any obstructions like an elbow or transaction.
Attach fan to suitable framework as specified (hanging or base vibration isolators are recommended). See chart below
for dimensions of vibration isolator centerlines (Fig.1). See Fig. 2 for physical dimensions.
The voltage rating of the motor must be checked for compatibility to supply voltage prior to final electrical connection.
Electrical lead-in wires are then connected to the factory supplied safety disconnect switch. All wiring must conform to
local and national codes.
Installation, Operation, and Maintenance Manual
Model XID Direct Drive
Centrifugal Inline Fans
Please read and save these instructions for future reference. Read carefully before attempting to assemble, install, operate
or maintain the unit. Failure to comply with instruction could result in personal injury and/or property damage!
Upon receiving unit, check for any damage that may have occurred during transit and report it immediately to the shipper.
Also check to see that all accessory items are accounted for.
June 2007
A
1in.
C sq.
B sq.
B sq.
1in.
C sq.
XID Dimensional Data
Fig. 2
Unit Size
A
B
C
Material Thickness
(ga.)
Approx. Unit
Weight (lbs.)
60-75
13
12
8
7
⁄
8
20
25
80-95
16
15
11
7
⁄
8
20
40
100
21
17
13
7
⁄
8
20
60
120
21
19
15
7
⁄
8
20
75
130
21
21
17
7
⁄
8
20
90
140
22
23
19
7
⁄
8
18
105
160
26
26
22
7
⁄
8
18
130
All dimensions are in inches.
Wheel Rotation
Direction of wheel rotation is
critical. Reversed rotation will
result in poor air performance,
motor overloading and possible
burnout. Check wheel rotation
(all XID fans have CW wheel
rotation when viewed from top
of fan) by momentarily energizing the unit.
Rotation should be clockwise as shown in Fig. 4 and
correspond to the rotation decal on the unit.
C
lo
ck
w
is
e
Fig. 4