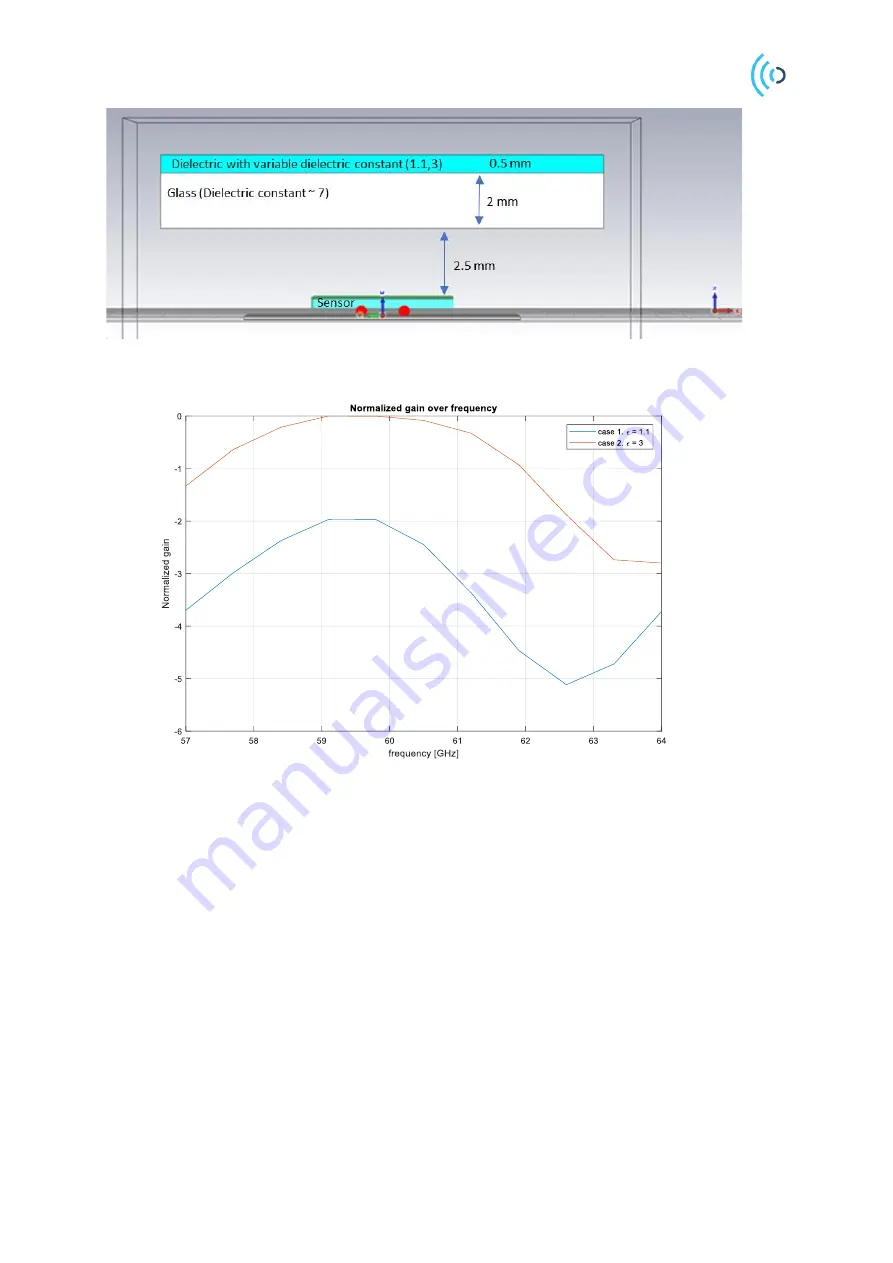
Hardware and physical integration guideline PCR Sensor A111
Page 20 of 32
© 2022 by Acconeer
– All rights reserved
2022-03-08
Figure 20. Simulation scenario: Sensor, air-gap, the matching layer and the screen.
Figure 21. Normalized antenna gain (Tx or Rx antenna gain) where the matching layer dielectric constant is set to 1.1
and 3.