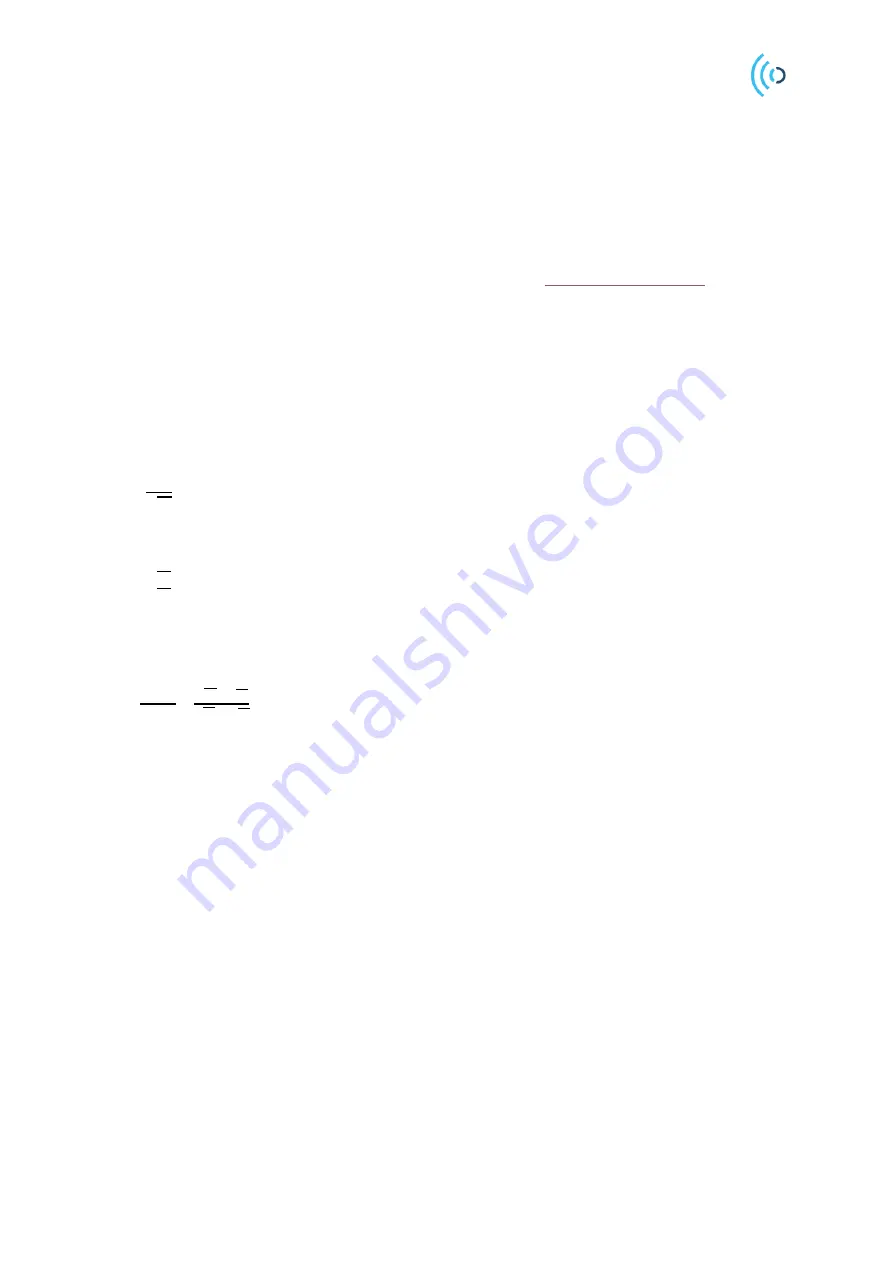
Hardware and physical integration guideline PCR Sensor A111
Page 12 of 32
© 2022 by Acconeer
– All rights reserved
2022-03-08
4 Physical Integration
EM waves can interact with the objects and the media in which they travel. As EM waves propagate,
they can be reflected, refracted, or diffracted. These interactions cause the radar pulse to change the
direction and to reach the areas which would not be possible if the radar pulse travelled in a direct line.
This chapter provides the integration guidelines for simplified sensor cover scenarios. In any case, it is
important to carefully design and characterize the integration to ensure that the desired performance is
obtained. The radiation pattern presented in the A111 datasheet (
), shows the
sensor performance when integrated in free space.
4.1 Radome integration
A radome is a structural enclosure that protects a radar assembly. Radomes are generally made of
materials which are mainly characterized by their dielectric properties. Dielectric materials have a
characteristic impedance of
𝑍
𝑑
=
𝑍
0
√𝜖
𝑟
where
𝜖
𝑟
is the dielectric constant relative to the free space and
𝑍
0
is the wave impedance in free-space.
𝑍
0
= √
𝜇
0
𝜀
0
= 377
Ω
When an EM wave hits a dielectric material at a normal incident angle, the reflection coefficient is
defined as
Γ =
𝑍
𝑑
−𝑍
0
𝑍
𝑑
+𝑍
0
=
√𝜀
0
− √𝜀
𝑟
√𝜀
0
+ √𝜀
𝑟
The transmission coefficient is defined as T = 1 +
Γ
. It is important to select dielectric materials for the
radome such that the reflection coefficient has a low value. Therefore, a low dielectric constant material
will minimize the reflections and reduce the impact on the radiation pattern and insertion loss. Typically,
radomes are made of plastic and the dielectric constant of common plastic (ABS, PC, Teflon, PP) is less
than 3, therefore, reflection coefficient for plastic materials is usually low. To further optimize the
radome integration, shape of the radome, distance to the radar and the thickness of the radome needs to
be considered in the design.
Figure 11 shows a scenario where a 1mm thick radome made of ABS plastic is placed at different
distances, D, from the radar. The amplitude variation of the reflected waves from the radar target can be
seen in the measured results shown in Figure 12. The variation of the amplitude is explained by the
standing wave phenomena. The transmitted wave (indicated as blue in Figure 13) travels in the air
medium until it reaches the second medium (plastic cover). Depending on the properties of the second
medium, part of the energy will be transmitted through the medium and part of it will be reflected. The
reflected pulse (indicated as yellow in Figure 13) will travel back to the PCB and be reflected again
(indicated as red in Figure 13). Depending on the distance D, the transmitted wave and the reflected
pulse can add up coherently or noncoherently. The maximum and minimum occur at multiples of the
half wavelength of the radar pulse. The impact of the pulse length is visible in the measurement results
(Figure 12). When the distance D gets larger than the pulse length, the standing wave disappears.