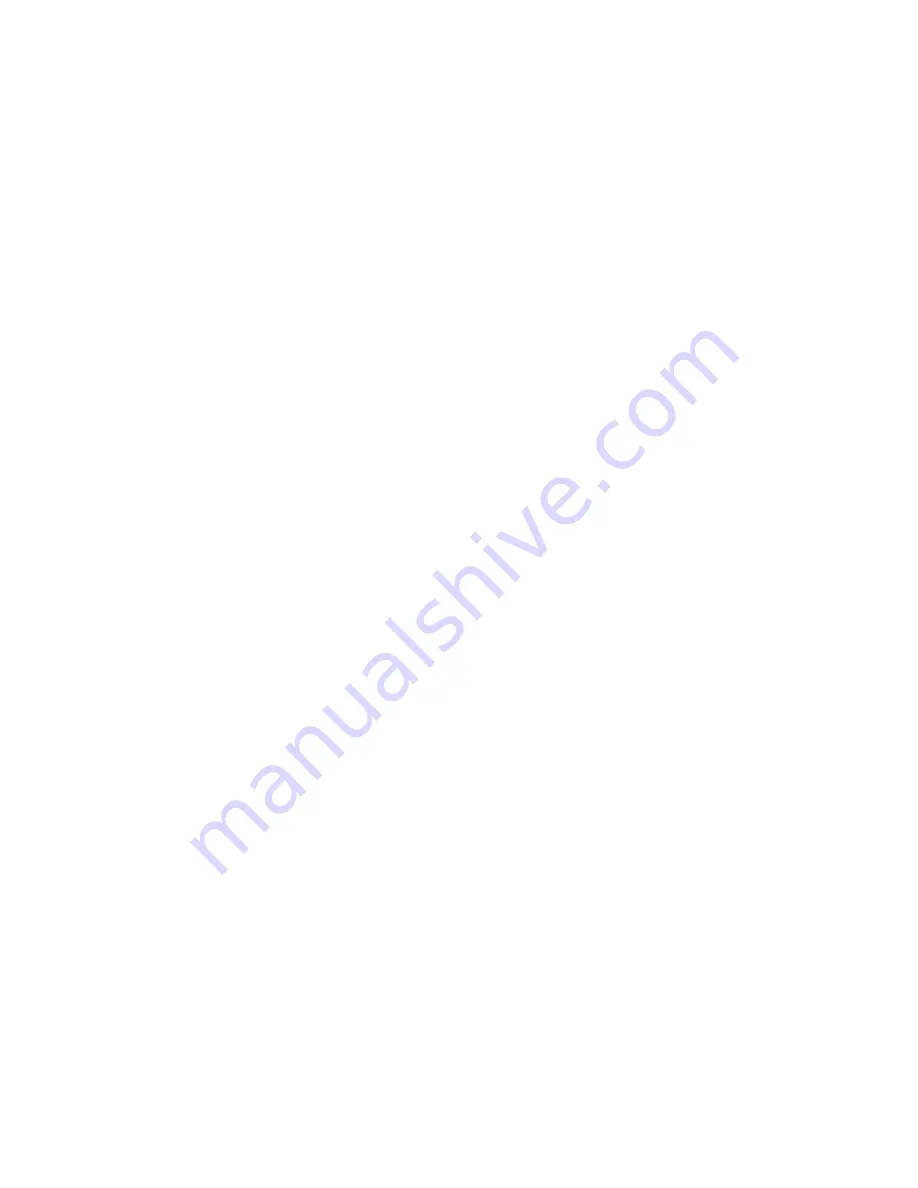
24
data logging will occur anytime the Data Logging Input (Auxiliary Input #1) is
connected to an electrical ground source. Logging will stop when the input is
disconnected from the electrical ground source.
Logger Data Source
If your Engine Analyzer is connected to an ACCEL/DFI Generation 7+ ECM, and you
want to record internal data values from within the ECM, set this switch to RECORD
GEN 7+ ECM DATA. Set this switch to INTERNAL DATA CHANNELS ONLY if you do
not want to record data from an ECM.
Setting this switch improperly will cause the logger to record data improperly, or to
not record any at all. If you see instances of a data run being recorded with 0 data
samples stored in the logger, this switch was probably set wrong – or the data cable
was connected improperly (or not at all) to the Gen 7+ ECM.
Log File Creation
When this switch is in the NEW LOG FILE FOR EACH RUN, data will be downloaded
from the Data Logger and stored in separate files for each run that was recorded.
The file names will have _RUN1, _RUN2… appended to the end of their names in
order to distinguish one run from another.
When this switch is in the STORE ALL DATA IN ONE FILE position, all the data
samples stored in the Data Logger will be downloaded into a single data file.
Logging Mode
When this switch is in the BACKGROUND – CONTINUOUS RECORDING position, only
1 data logging session may be stored in memory at a time. However, if the length of
the recording session exceeds the capacity of the data logger, data recording
continues with the oldest data in the logger memory being overwritten with newest
data. This allows data to be recorded in a continuous loop as long as the Data
Logging Enable input is activated. Upon deactivation, the last several minutes of
data will always remain in the logger’s memory. See below for a table of the
available recording time based on the available data recording rates.
This feature is useful for troubleshooting intermittent engine problems. Data
recording can be stopped once an intermittent event has occurred, allowing the data
recorded during the period of time leading up to the condition to be retained in the
logger memory. This permits easy analysis of the conditions leading up to the
problem.
Setting this switch to the MANUAL – RECORD UNTIL MEMORY IS FULL position will
cause the Data Logger to record data only until the internal memory becomes full.
See the table below for a list of recording times vs. data recording rates.
RPM Data Source
When recording Generation 7+ ECM data, this switch controls the source of the
Engine Speed data channel. Setting this switch to the GEN 7+ ECM position will
cause the Data Logger to record the RPM input from your ECM.
Setting this switch to the EXTERNAL RPM INPUT WIRE position will read engine speed
values from the RPM input wire on the Data Logger. You must supply a 5 Volt
square wave signal to the input wire in order for the Data Logger to read engine
speed.