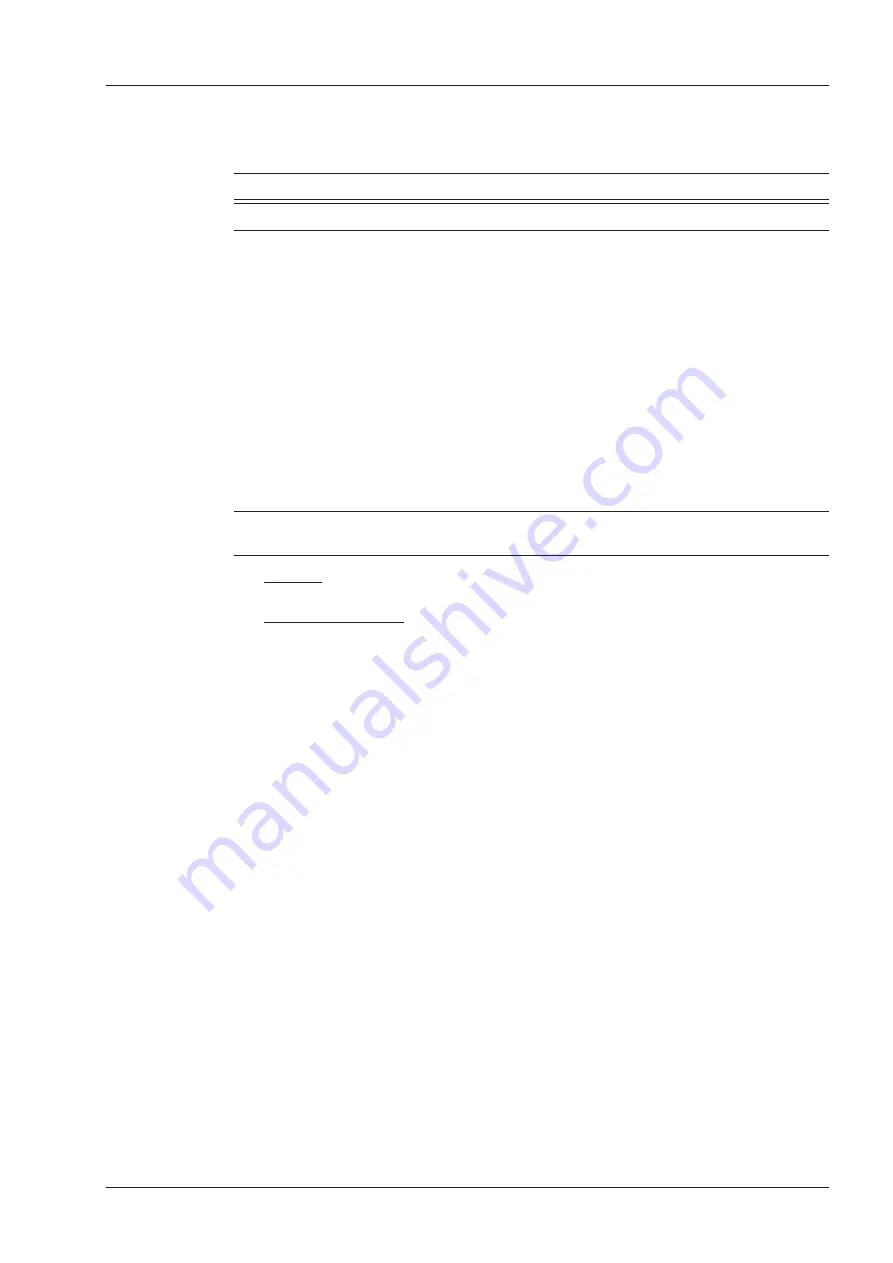
25
1ZSE 5492-129 en, Rev. 6
CAUTION
Make sure that no loose parts fall into the transformer through the hole for the gear box.
No driving shaft of the on-load tap-changer is allowed to be rotated.
10.
Remove the cover of the new gear box.
11.
Adjust the new gear box to the same position as the motor-drive and to its exact posi-
tion by rotating the shafts.
12. The shafts of the gear box have spherical couplings with driving pins that fit in the
grooves of the couplings in the shaft ends. Turn the driving pin of the vertical coupling
so its flat sides are vertical, parallel to the shaft in the transformer tank.
13. Mount a new O-ring in the flange for the gear box.
14.
Check the position of the groove in the coupling of the shaft in the transformer tank,
visible in the hole in the flange for the gear box. The driving pin of the spherical coupling
should be positioned as the groove.
15. Lower the gear box on to the flange, directed as the old one. The driving pin should
enter the groove in the insulating shaft.
CAUTION
The gear box must not be forced down! If the coupling does not engage, lift the gear box
and adjust the setting of the driving pin.
16.
For UCL:
Mount the four screws (lock the screws with locking fluid) and the sealing
washers.
For UCG, UCC, UCD: Mount the four clamps with screws and washers.
17.
If there are two horizontal shafts on the gear box, start with the one closest to the
motor-drive. Connect the end of the shaft with the fixed brass coupling to the gear box
closest to the motor-drive. Put on the protection tubes and hose clamps.
18.
Fit the loosened coupling to the replaced gear box. Tighten the two screws closest to
the gear box first leaving an axial play of 2 mm. Tighten the remaining screws.
Check that the position indicator in the gear box is in its exact position, see Fig. 8. If
not, loosen the two screws in the multihole coupling on the gear box and find the posi
-
tion of the screws that positions the opening in the brass toothed wheel closest to the
red point in the gear box housing. The deviation from exact alignment
must not
be
more than shown in Fig. 8! Tighten the screws.
19.
Apply grease on the couplings. Fit the protection tubes to the gear boxes, turning the
slots downwards. Fit and tighten the hose clamps.
For a single unit on-load tap-changer or when a gear box of the last unit is
replaced, continue with point 23.
If the on-load tap-changer consists of more than one unit and the gear box of
the unit next to the one with replaced gear box also should be replaced, start
doing that by restart from point 7. If not, proceed with point 20.
20.
If the replaced gear box has two horizontal shafts, mount the second shaft as follows:
Loosen the screws holding one of the brass couplings on the shaft. Connect the end
of the shaft with the fixed brass coupling to the gear box it was connected to before
disassembly. Put on the protection tubes and hose clamps. Fit the loosened coupling to
the replaced gear box. Tighten the two screws closest to the gear box first leaving an
axial play of 2 mm. Tighten the remaining screws.
3. Repairs and adjustment