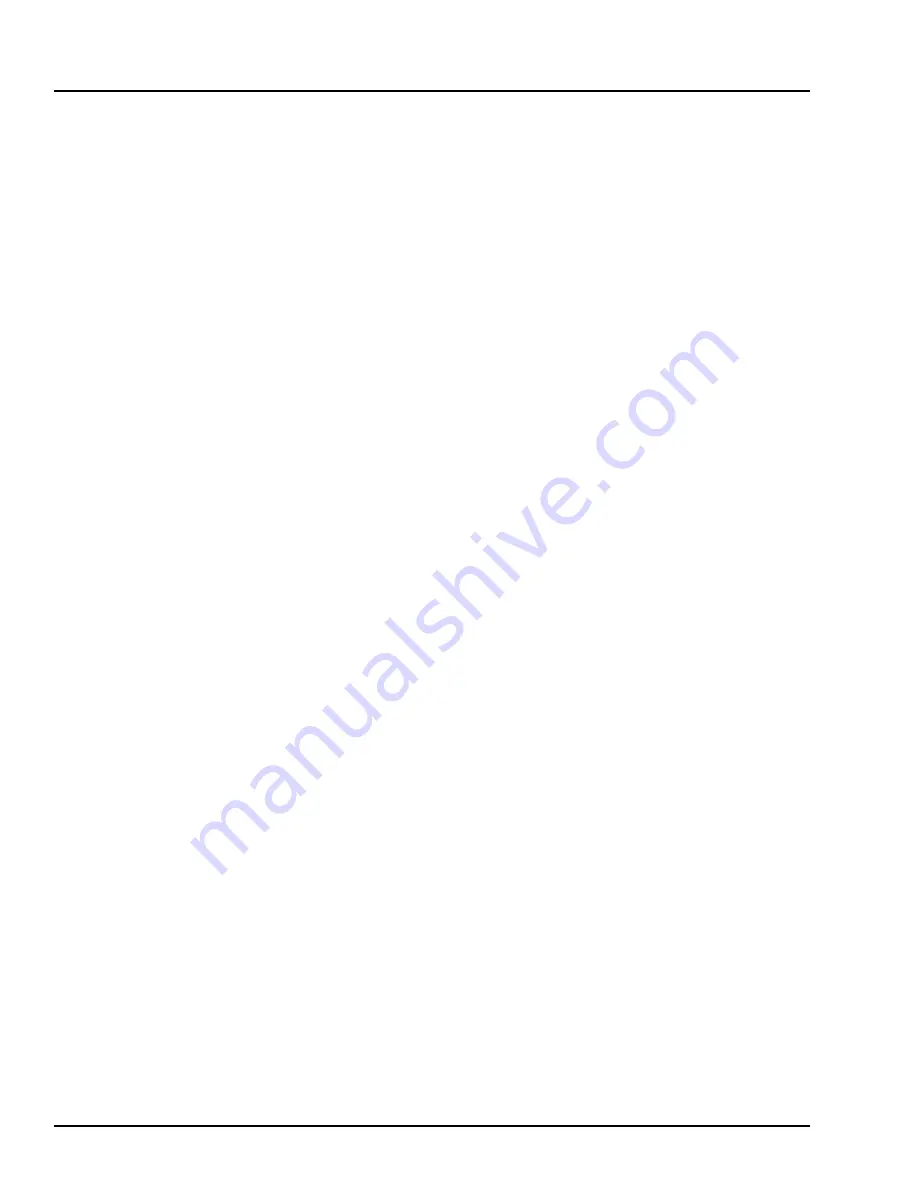
Swirlmeter (TRIO-WIRL S) 2 - 4
PN25080
TRIO-WIRL INSTRUCTION MANUAL
2.4 Installation
2.4.1 Inspection
All equipment should be inspected for damage that
may have occurred during shipment. All damage
should be reported to the shipping agent. If the equip-
ment is damaged to the extent that faulty operation
may result, contact ABB Inc. before installation. Always
reference the complete instrument serial number and
model number in all correspondence concerning the
equipment supplied.
2.4.2 Location & Mounting
2.4.2.1 Installation
The Swirlmeter may be installed at virtually any loca-
tion in a pipeline. The meter may be installed at any
angle and is available in a flange style body that
mounts between adjacent pipe flanges of the process
piping. Since the meter is unidirectional, it must be ori-
ented in accordance with the direction of the process
flow. A flow direction arrow is provided on the meter
body to assure correct orientation.
Take care to observe the following guidelines:
*
Do not exceed the ambient temperature require-
ments
*
Observe the recommended inlet and outlet straight
sections piping requirements (Refer to Figure
*
Make sure the flow direction corresponds to the
direction indicated by the arrow on the flowmeter
primary.
*
Make sure that the required minimum distance for
removing the converter and exchanging sensors is
provided.
*
The inside diameters of the flowmeter primary and
the pipeline should be identical.
*
Pressure fluctuations at zero flowrate in long pipe-
lines should be eliminated by installing intermedi-
ate gate valves.
*
Flow pulsations resulting from piston pump or com-
pressor operation should be reduced by using
appropriate dampeners.
*
When metering liquids, the flowmeter primary must
always be completely filled with fluid and cannot
drain.
*
For high fluid temperatures the flowmeter primary
is installed so that the electronic assembly is
mounted at the side or bottom of the flowmeter
(Refer to Figure
).
*
If the possibility of gas bubble formation exists, gas
separators should be provided.
*
Assuming a properly supported pipeline and the
converter’s DSP signal processing technology,
vibration problems should not be encountered in
normal industrial applications. However, it is good
practice to minimize mechanical vibrations using
supports if required. When installing in long pipe-
lines which have a tendency to vibrate, eliminators
should be installed upstream and downstream of
the flowmeter.
*
In vertical and sloping installations, the electrical
conduit entries should face downward to retard the
entry of condensation.
2.4.2.2 Recommended Inlet & Outlet Sections
Due to the measurement principles of the Swirl Flow-
meter it can be installed with very minimal inlet and out-
let straight section lengths. Strainers and flow
straighteners are not required. Figure
shows the
recommended lengths for the inlet and outlet straight
sections for various installation conditions. No inlet and
outlet straight sections are required when single or
double elbows are installed upstream or downstream
from the flowmeter primary when the radius of the
elbow is greater than 1.8 x D.
To assure optimum meter performance, the meter
should be installed in accordance with the upstream
and downstream straight run piping requirements
shown in Figure
. The straight run piping should be
schedule 80 or lighter pipe. Process flanges should be
raised face.
Remove the covers used to protect the meter inlet and
outlet surfaces from damage during shipment.
Place the two flange gaskets (supplied) against the
upstream and downstream flange faces (Refer to Table
for replacement flange gaskets). Align the gasket
holes with the flange hole pattern. When installing the
flange gaskets, make sure that the gaskets fit properly
and are alligned properly so that they don't project into
the pipe line causing an alteration of the flow profile. A
change in flow profile can adversely affect meter accu-
racy.