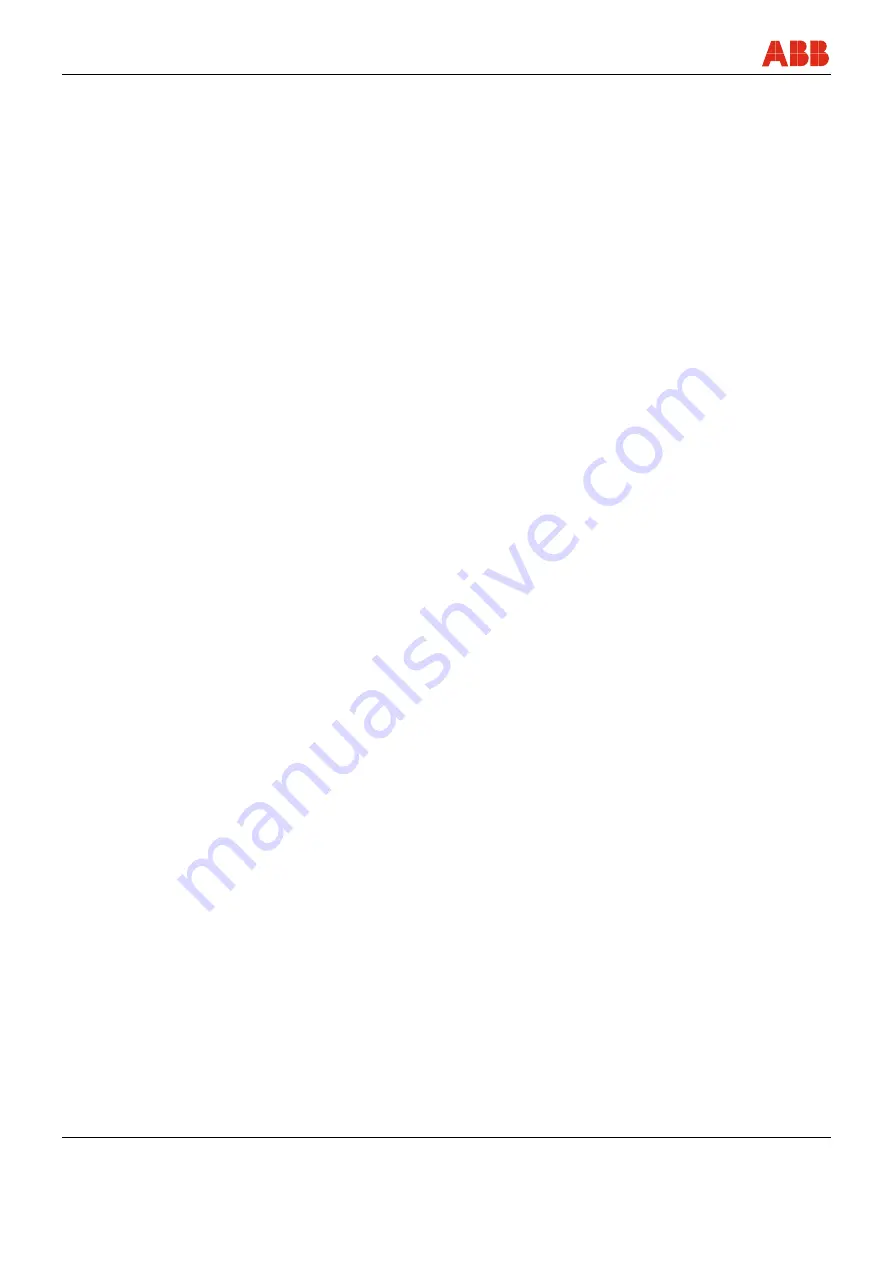
Periodic checks
10 SensyTemp
TSP
SM/TSP/SIL-EN
7 Periodic
checks
7.1
SensyTemp TSP temperature sensors with TTH300 transmitter
Safety inspections
The safety function for the entire safety loop must be checked regularly in accordance with IEC
61508. The inspection intervals are defined when calculating the individual safety loops for a
system.
Users are responsible for selecting the type of inspection and the intervals within the specified
period. The PFD
AV
value depends on the selected inspection interval. For the PFD
AV
values in
the SIL declaration of conformity, the inspection interval T[Proof] for checking the safety function
is 1 year. For additional inspection intervals with corresponding PFD
AV
values, refer to the
chapter “Management Summary FMEDA”.
Inspections must be conducted in a manner that enables users to verify proper function of the
safety equipment in combination with all components.
One possible procedure for recurring tests to detect hazardous and unidentified device errors is
described in the following section. Some 99% of the “Du” errors in the transmitter electronic unit
are detected by this test.
Checking the safety function
To check the safety function of the device, proceed as follows:
1. Bridge the safety DCS or take other appropriate measures to ensure the alarm is not
triggered unintentionally.
2. Deactivate write protection (refer to the relevant operating instructions).
3. Set the current output of the transmitter to a high alarm value by using the DTM simulation
command (Diagnosis/Simulation/Current Output).
4. Check whether the current output signal reaches this value.
5. Set the current output of the transmitter to a low alarm value by using the DTM simulation
command.
6. Check whether the current output signal reaches this value.
7. Activate write protection (refer to the relevant operating instructions) and wait at least 20
seconds.
8. Restart by switching off the device.
9. Check the current output with reference temperature; set the LRV value (4 mA) and URV (20
mA) via 2-point calibration.
10. Remove the bridge from the safety DCS or use another method to restore the standard
operating mode.
11. After performing the test, the events must be documented and archived properly.
A suitable sensor simulator (PT100-simulator, Ref. voltage source) can be used to check the
transmitter electronic unit without sensor. Test the sensor according to SIL requirements for
customer applications. ABB temperature sensors are checked according to the quick check
(see next section).
Summary of Contents for SensyTemp TSA101
Page 16: ...Safety engineering parameters 16 SensyTemp TSP SM TSP SIL EN ...
Page 18: ...Management Summary FMEDA 18 SensyTemp TSP SM TSP SIL EN 12 Management Summary FMEDA ...
Page 19: ...Management Summary FMEDA SM TSP SIL EN SensyTemp TSP 19 ...
Page 20: ...Management Summary FMEDA 20 SensyTemp TSP SM TSP SIL EN ...
Page 21: ...Management Summary FMEDA SM TSP SIL EN SensyTemp TSP 21 ...