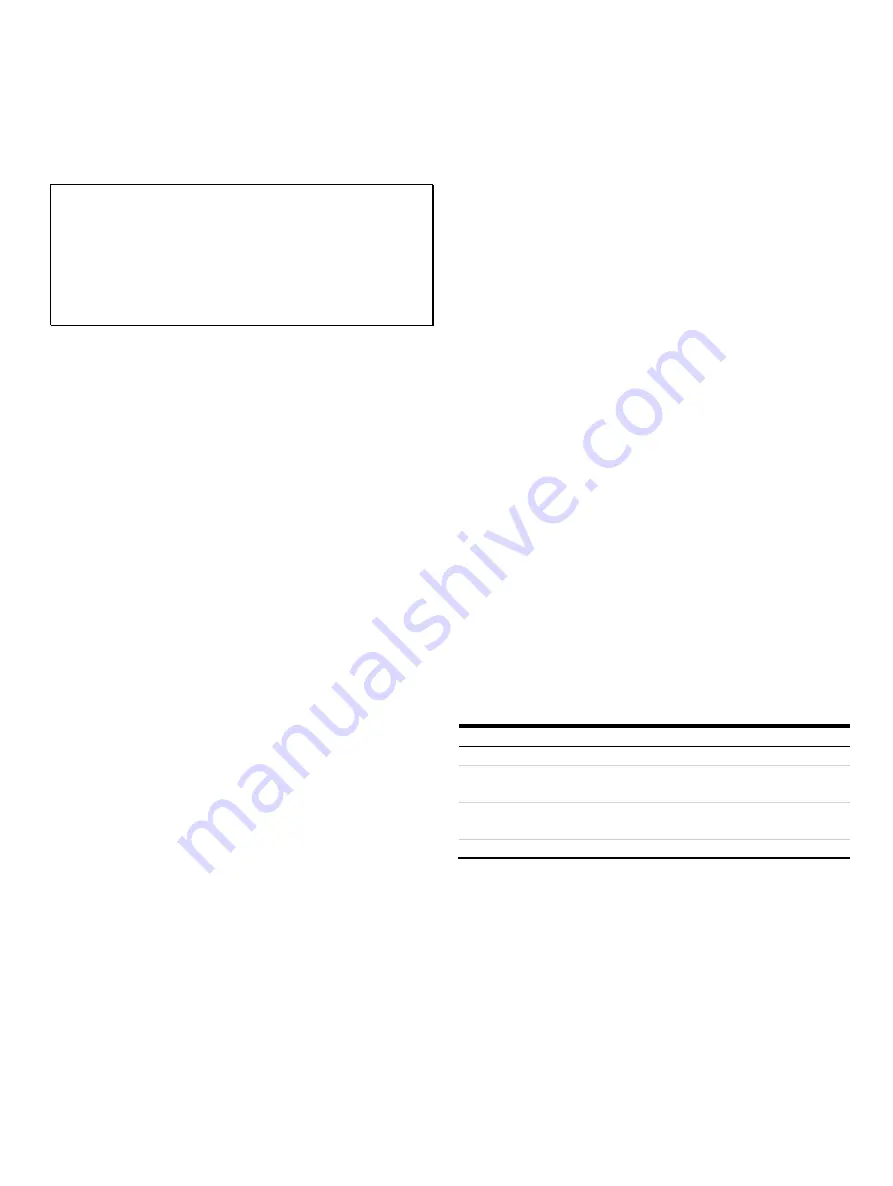
FMT230, FMT250
THERMAL MASS FLOWMETER | CI/FMT230/250-EN REV. B
17
Cable entries
1
Transport protection plugs
Figure 2: Cable entry
The devices are delivered with ½ in NPT threads with transport
protection plugs.
• Unused cable entries must be sealed off prior to
commissioning using either approved pipe fittings or cable
glands in accordance with national regulations (NEC, CEC).
• Make sure that the pipe fittings, cable glands and, if
applicable, sealing plugs are installed properly and are leak-
tight.
• If the device is to be operated in areas with combustible
dusts, a threaded pipe connection or cable gland with
suitable approval must be used.
• The use of standard cable glands and closures is prohibited.
Note
Devices which are certified for use in North America are supplied
with a ½ in. NPT thread only and without cable glands.
Electrical connections
Grounding
The sensor must be grounded in accordance with the applicable
international standards.
In accordance with NEC standards, an internal ground
connection is present in the device between the sensor and the
transmitter.
Perform grounding of the device in accordance with
Pin
assignment
on page 41.
Process sealing
In accordance with ‘North American Requirements for Process
Sealing between Electrical Systems and Flammable or
Combustible Process Fluids’.
Note
The device is suitable for use in Canada.
• For use in Class II, Groups E, F and G, a maximum surface
temperature of 165 °C (329 °F) may not be up-scaled.
• All cable (conduits) should be sealed from the device within a
distance of 18 in (457 mm).
ABB flowmeters are designed for the worldwide industrial
market and are suitable for functions such as the measurement
of flammable and combustible liquids and can be installed in
process pipes.
Connecting devices with cable (conduits) to the electric
installation makes it possible for measuring media to reach the
electric system.
To prevent measuring media from seeping into the electric
installation, the devices are equipped with process gaskets
which meet requirements in accordance with ANSI / ISA 12.27.01.
SensyMaster flowmeters are designed as ‘Dual Seal Devices’.
In accordance with the requirements of standard
ANSI / ISA 12.27.01, the existing operating limits of temperature,
pressure and pressure bearing parts must be reduced to the
following limit values:
Limit values
Flange or pipe material
No limitations
Nominal sizes
DN 25 to DN 2000
(1 to 78 in)
Operating temperature
−
20 °C to 280 °C
(−4
°F to 536 °F)
Process pressure
PN 40 / Class 300