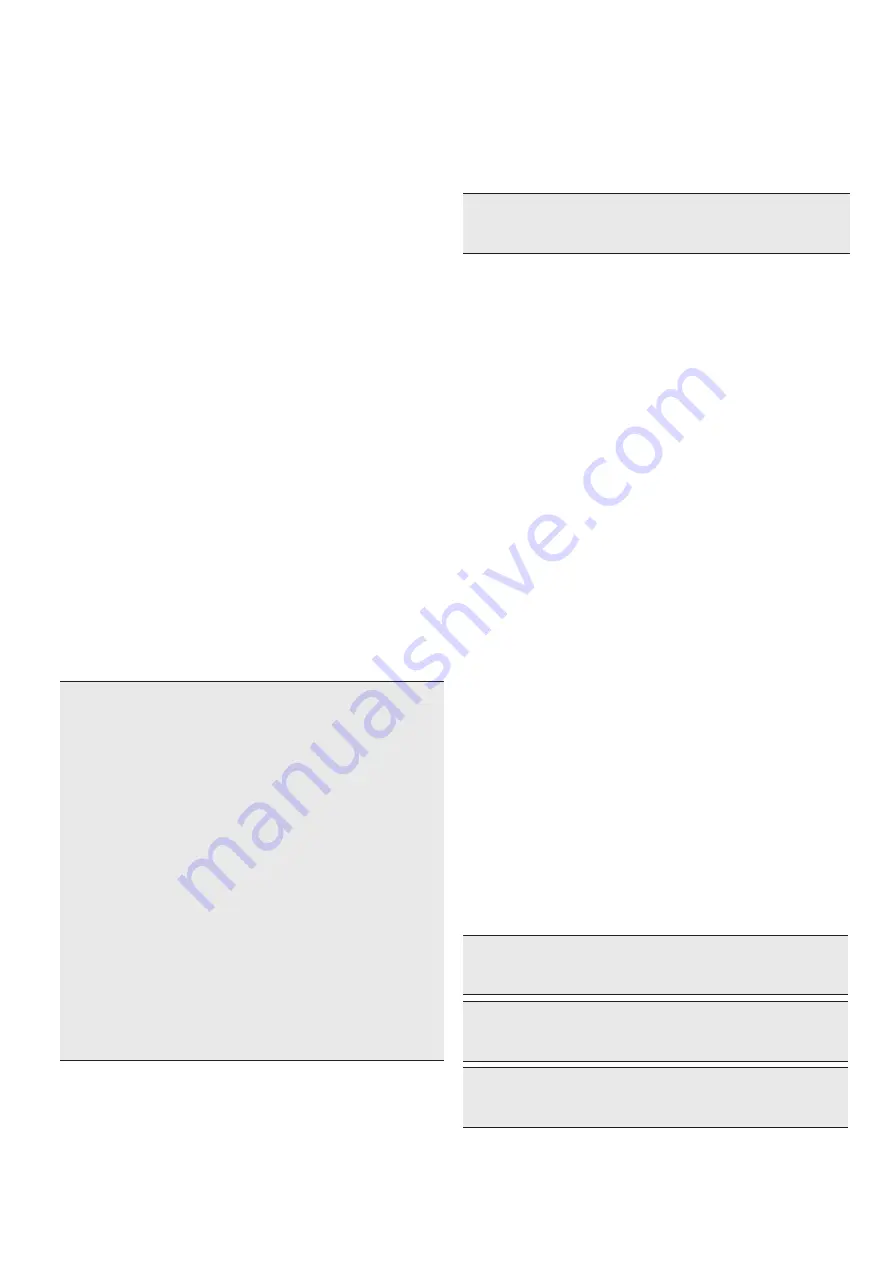
2 Safety
2.1 General safety information
The “Safety” section provides an overview of the safety aspects
to be observed for operation of the device.
The device has been constructed in accordance with the state
of the art and is operationally safe. It has been tested and left
the factory in perfect working conditions. The information in the
manual, as well as the applicable documentation and
certificates, must be observed and followed in order to maintain
this condition throughout the period of operation.
Full compliance with the general safety requirements must be
observed during operation of the device. In addition to the
general information, the individual sections in the manual
contain descriptions of processes or procedural instructions
with specific safety information.
Only by observing all of the safety information can you reduce
to the minimum the risk of hazards for personnel and/or
environment. These instructions are intended as an overview
and do not contain detailed information on all available models
or every conceivable event that may occur during setup,
operation, and maintenance work.
For additional information, or in the event of specific problems
not covered in detail by these operating instructions, please
contact the manufacturer. In addition, ABB declares that the
contents of this manual are not part of any prior or existing
agreements, commitments, or legal relationships; nor are they
intended to amend these.
All obligations of ABB arise from the conditions of the relevant
sales agreement, which also contains the solely binding
warranty regulations in full. These contractual warranty
provisions are neither extended nor limited by the information
provided in this manual.
Caution.
Only qualified and authorized specialist personnel should
be charged with installation, electrical connection, commissioning,
and maintenance of the transmitter. Qualified personnel are persons
who have experience in installation, electrical wiring connection,
commissioning, and operation of the transmitter or similar devices,
and hold the necessary qualifications such as:
— Training or instruction, i.e., authorization to operate and
maintain devices or systems according to safety engineering
standards for electrical circuits, high pressures, and
aggressive media
— Training or instruction in accordance with safety engineering
standards regarding maintenance and use of adequate safety
systems.
For safety reasons, ABB draws your attention to the fact that only
sufficiently insulated tools conforming to DIN EN 60900 may be
used.
Since the transmitter may form part of a safety chain, we
recommend replacing the device immediately if any defects are
detected. In case of use in Hazardous Area non sparking tools only
must be employed.
In addition, you must observe the relevant safety regulations
regarding the installation and operation of electrical systems,
and the relevant standards, regulations and guidelines about
explosion protection.
Warning.
The device can be operated at high levels of pressure and
with aggressive media. As a result, serious injury or significant
property damage may occur if this device is operated incorrectly.
2.2 Improper use
It is prohibited to use the device for the following purposes:
— As a climbing aid, e.g., for mounting purposes
— As a support for external loads, e.g., as a support for pipes.
— Adding material, e.g., by painting over the name plate or
welding/soldering on parts
— Removing material, e.g., by drilling the housing.
Repairs, alterations, and enhancements, or the installation of
replacement parts, are only permissible as far as these are
described in the manual. Approval by ABB must be requested
for any activities beyond this scope. Repairs performed by
ABB-authorized centers are excluded from this.
2.3 Technical limit values
The device is designed for use exclusively within the values
stated on the name plates and within the technical limit values
specified on the data sheets.
The following technical limit values must be observed:
— The Maximum Working Pressure may not be exceeded.
— The Maximum ambient operating temperature may not be
exceeded.
— The Maximum process temperature may not be
exceeded.
— The housing protection type must be observed.
2.4 Warranty prevision
Using the device in a manner that does not fall within the scope
of its intended use, disregarding this manual, using
underqualified personnel, or making unauthorized alterations,
releases the manufacturer from any liability for any resulting
damage. This makes the manufacturer’s warranty null and void.
2.5 Use of instruction
Danger – <Serious damage to health/risk to life>.
This message
indicates that an imminent risk is present. Failure to avoid this will
result in death or serious injury.
Caution – <Minor injuries>.
This message indicates a potentially
dangerous situation. Failure to avoid this could result in minor
injuries. This may also be used for property damage warnings.
Important.
This message indicates indicates operator tips or
particularly useful information. It does not indicate a dangerous or
damaging situation.
2600T Series Pressure transmitters |
OI/S266-EN Rev. B 5