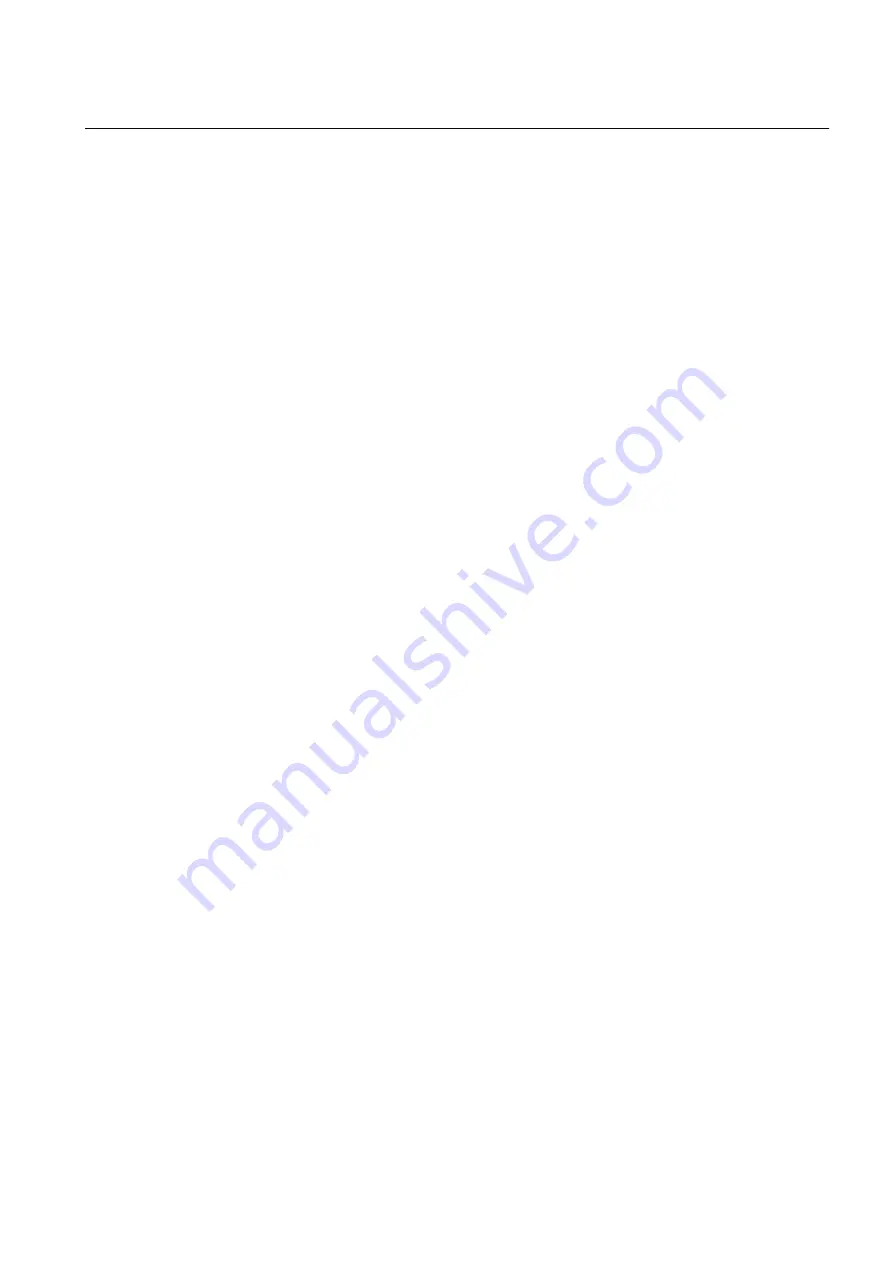
Each logical I/O module has an error flag that indicates signal or module failure.
The error flag is also set when the physical I/O module of the correct type is not
detected in the connected slot.
1MRK 505 372-UEN A
Section 5
Configuring the IED and changing settings
Busbar protection REB670 2.2 IEC
55
Commissioning manual