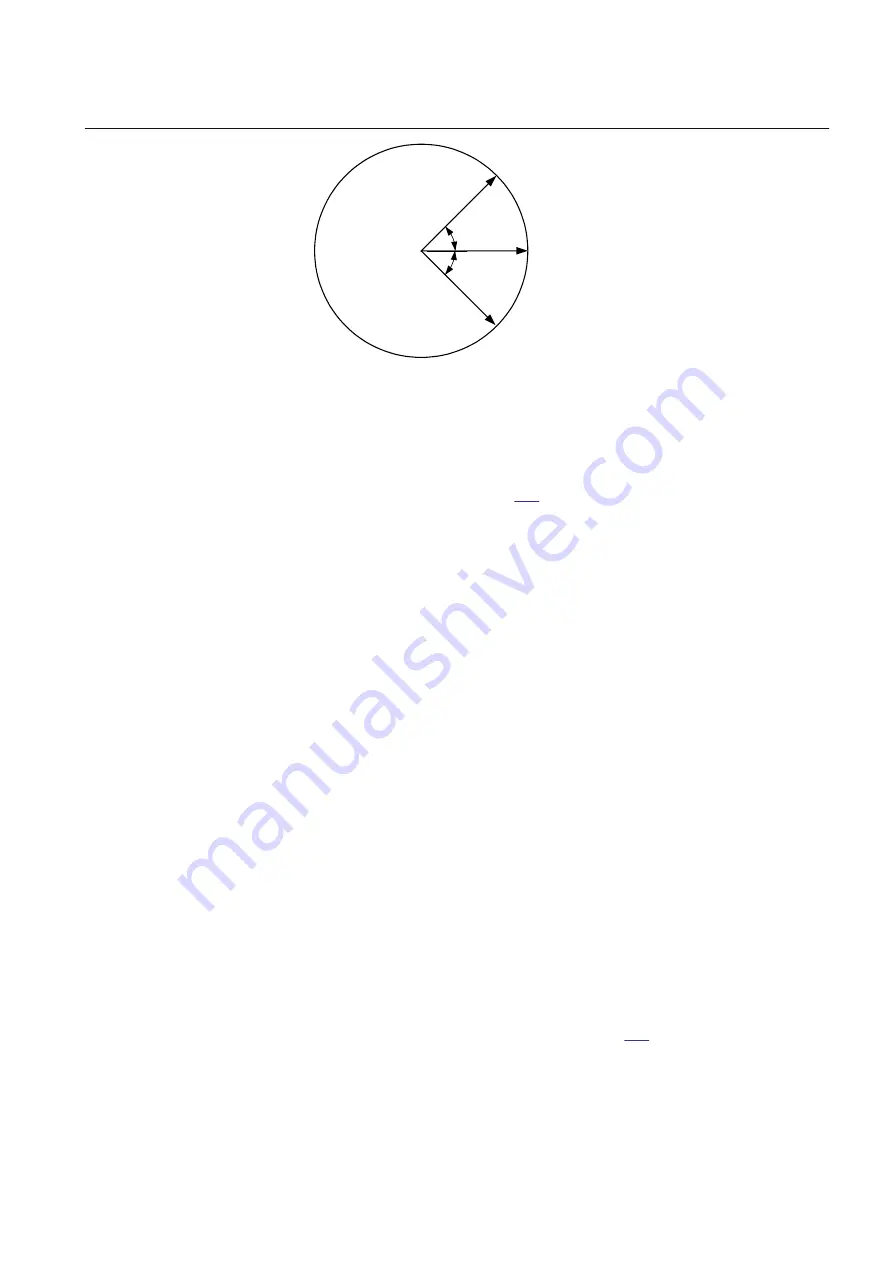
+d
j
-d
j
U-Bus
U-Line operation
U-Bus
No operation
en05000551.vsd
IEC05000551 V1 EN
Figure 104:
Test of phase difference.
3.
Change the phase angle bdφ and -dφ and verify that the two outputs
are activated for phase differences between these values but not for phase
differences outside, see figure
.
Testing the frequency difference
The frequency difference test should verify that operation is achieved when the
FreqDiffA
and
FreqDiffM
frequency difference is lower than the set value for
manual and auto synchronizing check,
FreqDiffA
and
FreqDiffM
respectively and
that operation is blocked when the frequency difference is bigger.
Test with frequency difference = 0 mHz
Test with a frequency difference outside the set limits for manual and auto
synchronizing check respectively.
1.
Apply voltages U-Line equal to 100%
UBaseLine
and U-Bus equal to 100%
UBaseBus
, with a frequency difference equal to 0 mHz and a phase difference
lower than the set value.
2.
Check that the AUTOSYOK and MANSYOK outputs are activated.
3.
Apply voltage to the U-Line equal to 100%
UBaseLine
with a frequency
equal to 50 Hz and voltage U-Bus equal to 100%
UBaseBus
, with a frequency
outside the set limit.
4.
Check that the two outputs are not activated. The test can be repeated with
different frequency values to verify that the function operates for values lower
than the set ones. If a modern test set is used, the frequency can be changed
continuously.
Testing the reference voltage
1.
Use the same basic test connection as in figure
.
1MRK 502 029-UEN A
Section 15
Verifying settings by secondary injection
217
Installation and commissioning manual
Summary of Contents for Relion 670 series
Page 1: ...Relion 670 series Generator protection REG670 Installation and commissioning manual...
Page 2: ......
Page 16: ...10...
Page 24: ...18...
Page 26: ...20...
Page 28: ...22...
Page 92: ...86...
Page 96: ...90...
Page 102: ...96...
Page 108: ...102...
Page 112: ...106...
Page 126: ...120...
Page 140: ...134...
Page 150: ...144...
Page 234: ...228...
Page 238: ...232...
Page 250: ...244...
Page 259: ...253...