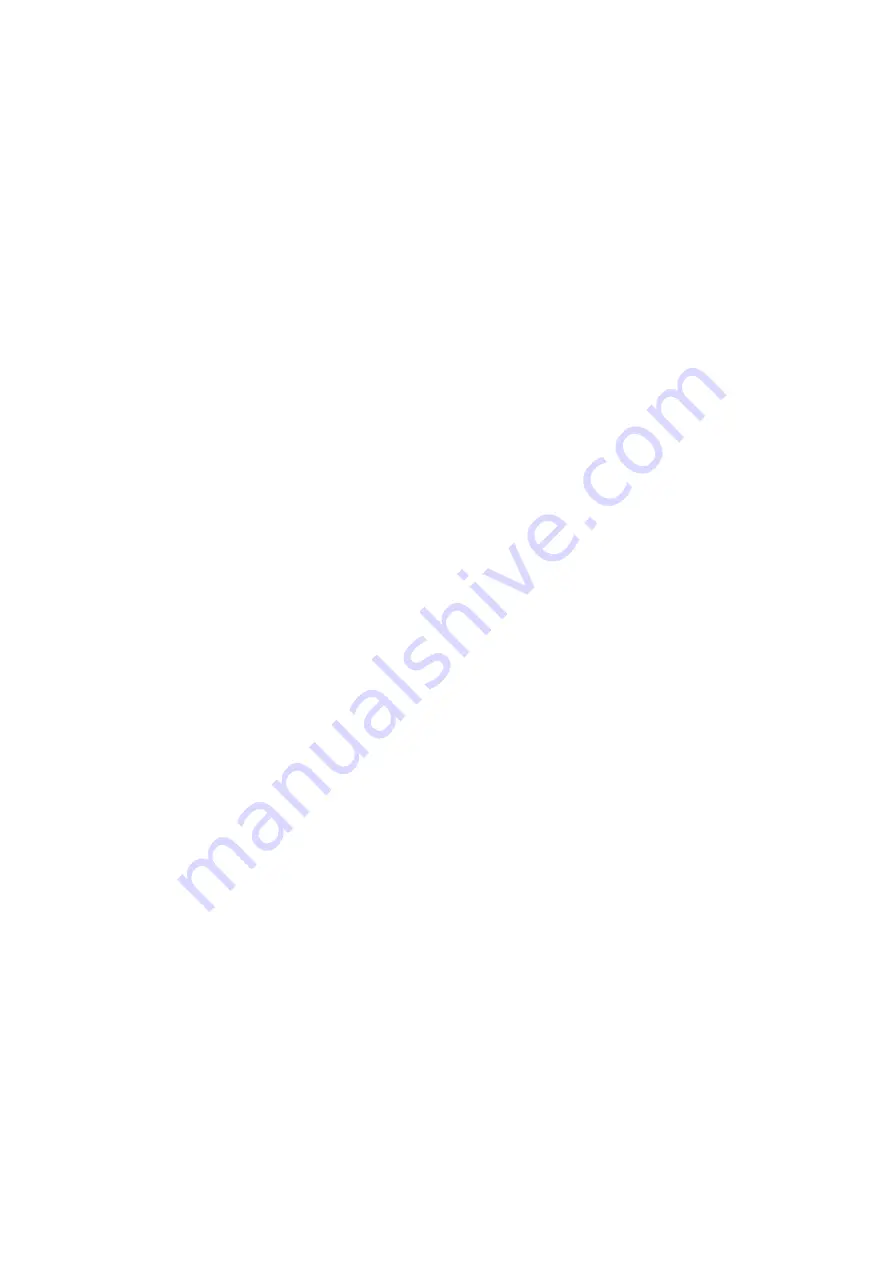
13.0 Service and maintenance
Cleaning
After maintenance the switch disconnector must be cleaned
before being put into service. Strong solvents and alcoholic
fluids must not be used. After cleaning, the contact area of the
main blades and the fixed contacts must be greased, type ISO-
FLEX TOPAS NCA 52. If the switch-disconnector is placed in
a very humid and polluted area, which will reduce the tracking
resistance, it is recommended to polish the insulators and insu-
lated components with Silicon Type DC200 Fluid 100 cst.
Switch disconnectors in service
The switch disconnector should be checked by conducting a
number of operations to check all the functions. The frequency
of maintenance depends on the service and environmental
conditions.
For new design NAL – marked with “NAL New Design 2008”
label if below specified service conditions are met, maintenan-
ce can be done even extended to 15-year-intervals:
1. Apparatus must be transported and stored in a genuine box.
2. Service conditions – installation:
a) apparatus must work in indoor application under normal
service conditions – according to IEC 62271:2007 – p. 2.1,
b) apparatus must be installed by qualified staff according to
manufacturer’s recommendation,
c) maximum number of mechanical cycles (1,000) must not be
exceeded,
d) maximum values and numbers of the making and breaking
capacity must not be exceeded,
e) safe distances to earthed parts or to other lived parts must
be kept,
f) in special cases (e.g.: fault in the circuit where the NAL is
installed or the apparatus has been overloaded) apparatus
should be inspected,
g) visible label stating „NAL New Design 2008”.
For all other NAL, switch-disconnector should be checked at
least once a year.
– moving and fixed contacts are greased with – ISOFLEX
TOPAS NCA 52,
– mechanisms do not need any greasing under normal condi-
tions,
Note!
Arcing knives, piston and cylinder must not be greased.
Mechanical overhaul
For new design NAL – marked with “NAL New Design 2008”
label, complete overhaul of the switch disconnector should be
carried out after 1000 operations or 15 years in service, prefe-
rably by ABB’s staff.
For all other NAL, complete overhaul of the switch disconnec-
tor should be carried out after 1000 operations or 5 years in
service, preferably by ABB’s staff.
Electrical overhaul
The frequency of overhaul depends also on the number of
operations and the magnitude of the breaking current. After
about 100 operations at rated current or about 500 operations
at half the rated current the main contacts, the arcing contacts
and the arc
extinguishing chamber should be inspected and replaced if
necessary.
Replacement should take place when:
– the tip of the arcing contact knives has diminished approx.
3 mm (by minor damage might only cause polishing of the
arcing tip),
– the fixed arcing fingers are burned or do not make any con-
tact,
– the width of the slot in the arcing chamber is more than
8 mm.
NAL/NALF – Mounting and operation manual
21