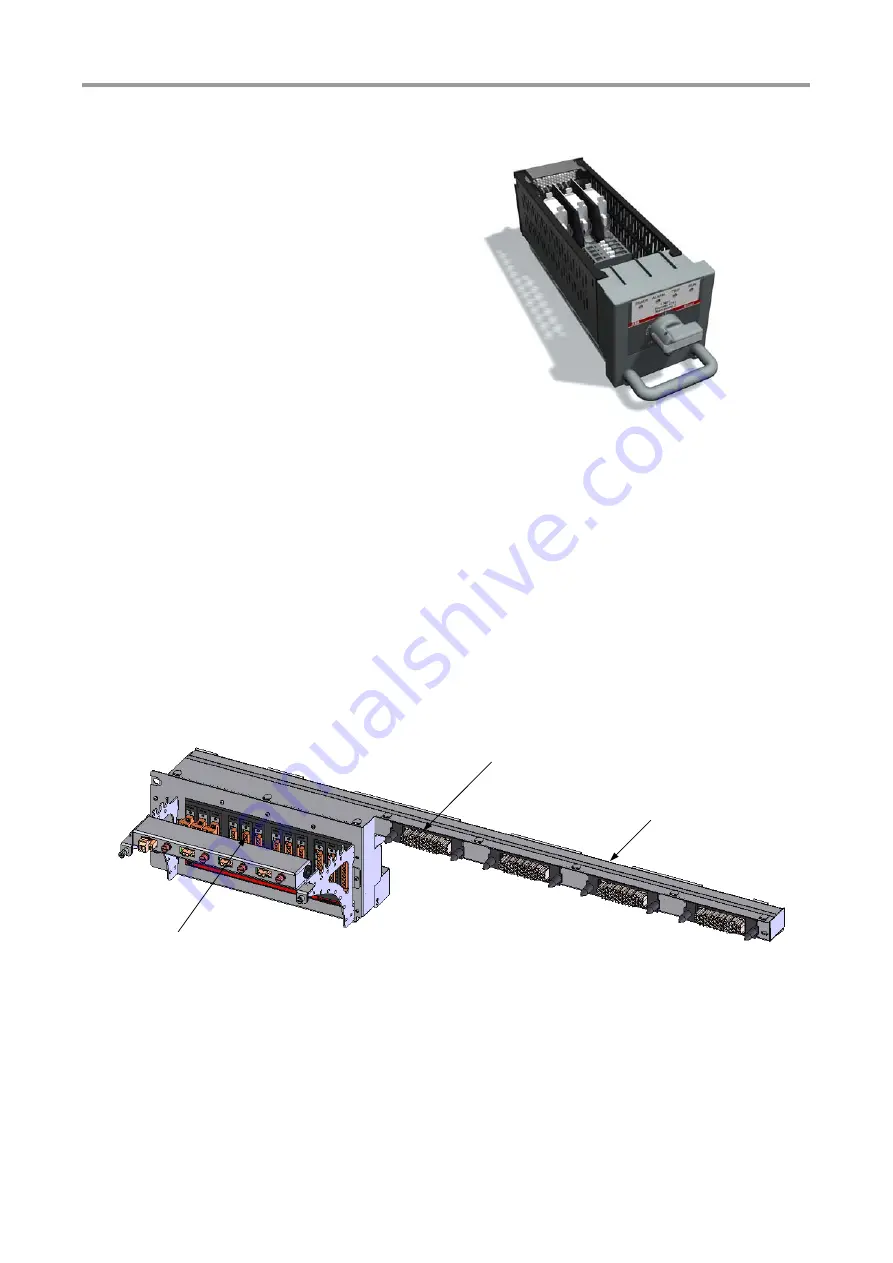
M
M
N
N
S
S
i
i
S
S
D
D
e
e
s
s
i
i
g
g
n
n
&
&
C
C
o
o
m
m
p
p
o
o
n
n
e
e
n
n
t
t
s
s
1
1
ABB MNS
i
S System Setup & Operation Quick Guide / System Release 6.0 – Rev.2 / Aug. 2011
1
1
5
5
*Specific
characteristics
of Fixed MStart modules
see page 10
1.6.2 Power Modules M
Start
/ M
Feed
The withdrawable M
Start
/ M
Feed
modules are
available in the sizes from 6E/4 to 24E depending
on the kW rating of the connected motor / load.
For module dimensions and selection tables,
please see page 9.
A combination of high precision shunt and micro-
processor forms a complete measuring system,
which does not only measure current very
precisely, but at the same time measures the
voltage and contact temperature.
Figure 10 M
Start
module size 6E/4
1.6.3 Conventional Feeder Modules
Feeder modules with module sizes described on
page 9, are also available for conventional
solutions, ready to be integrated into MNS
i
S
switchgear.
Utilisation of this option enables more cost
effective solutions for energy distribution
applications, where integrated solutions are not
required.
Connection details see section
Control terminal plug for
6E/4 conventional feeder module
Control Condapter
conventional type
Control connection plug set
with 3x8 control terminals
Figure 11 Control Condapter for conventional feeders