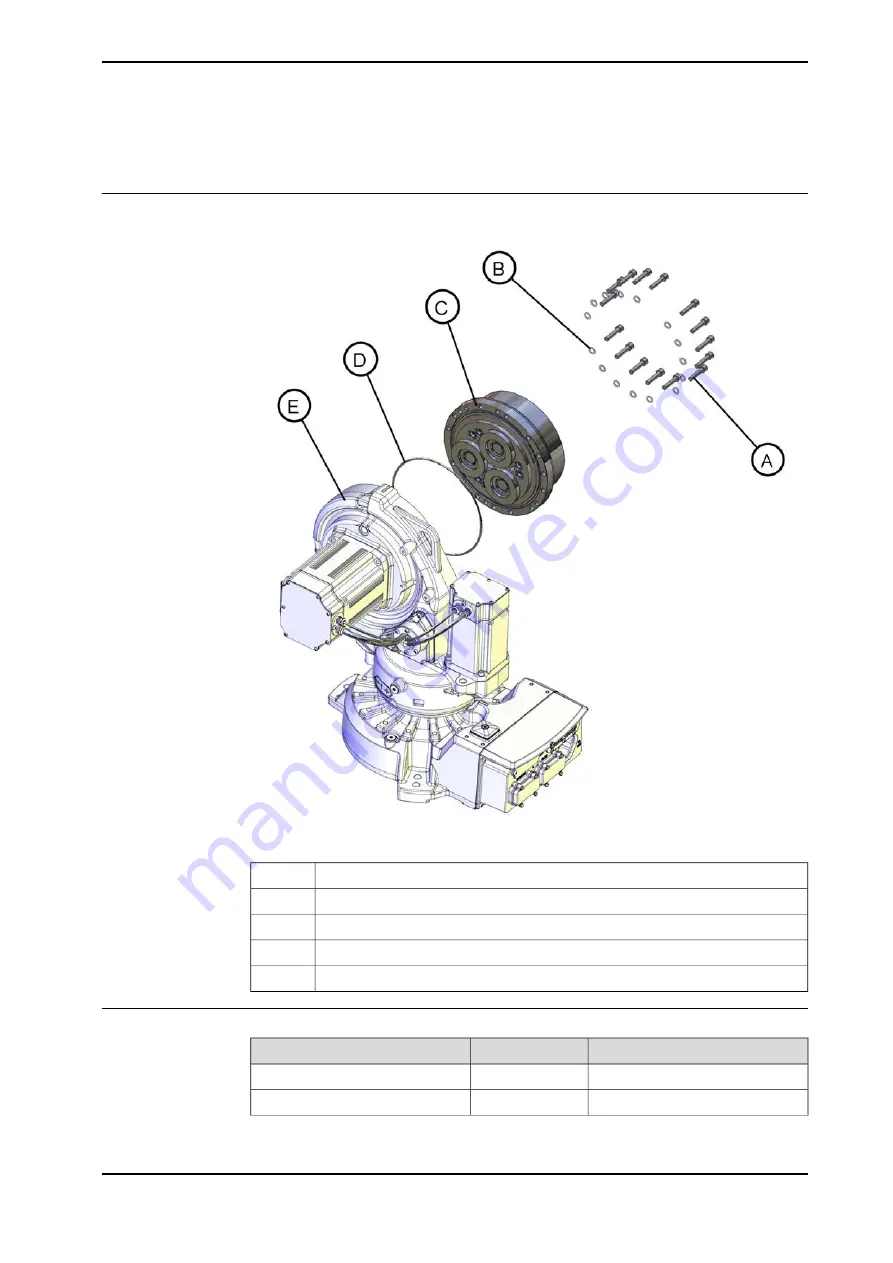
4.8.2 Replacing gearbox axis 2
Location of gearbox axis 2
The gearbox is located as shown in the figure.
xx0800000438
Attachment screws M12x50 quality Steel 12.9 Gleitmo (15 pcs)
A
Washers (15 pcs)
B
Gearbox axis 2
C
O-ring
D
Frame
E
Required equipment
Note
Art. no.
Equipment
3HAB7887-1
Rotation tool
Roundslings.
-
Lifting accessories
Continues on next page
3HAC033453-001 Revision: H
303
© Copyright 2009-2013 ABB. All rights reserved.
4 Repair
4.8.2 Replacing gearbox axis 2
Summary of Contents for IRB 4600 - 40/2.55
Page 1: ...ABB Robotics Product manual IRB 4600 ...
Page 108: ...This page is intentionally left blank ...
Page 318: ...This page is intentionally left blank ...
Page 332: ...This page is intentionally left blank ...
Page 373: ......