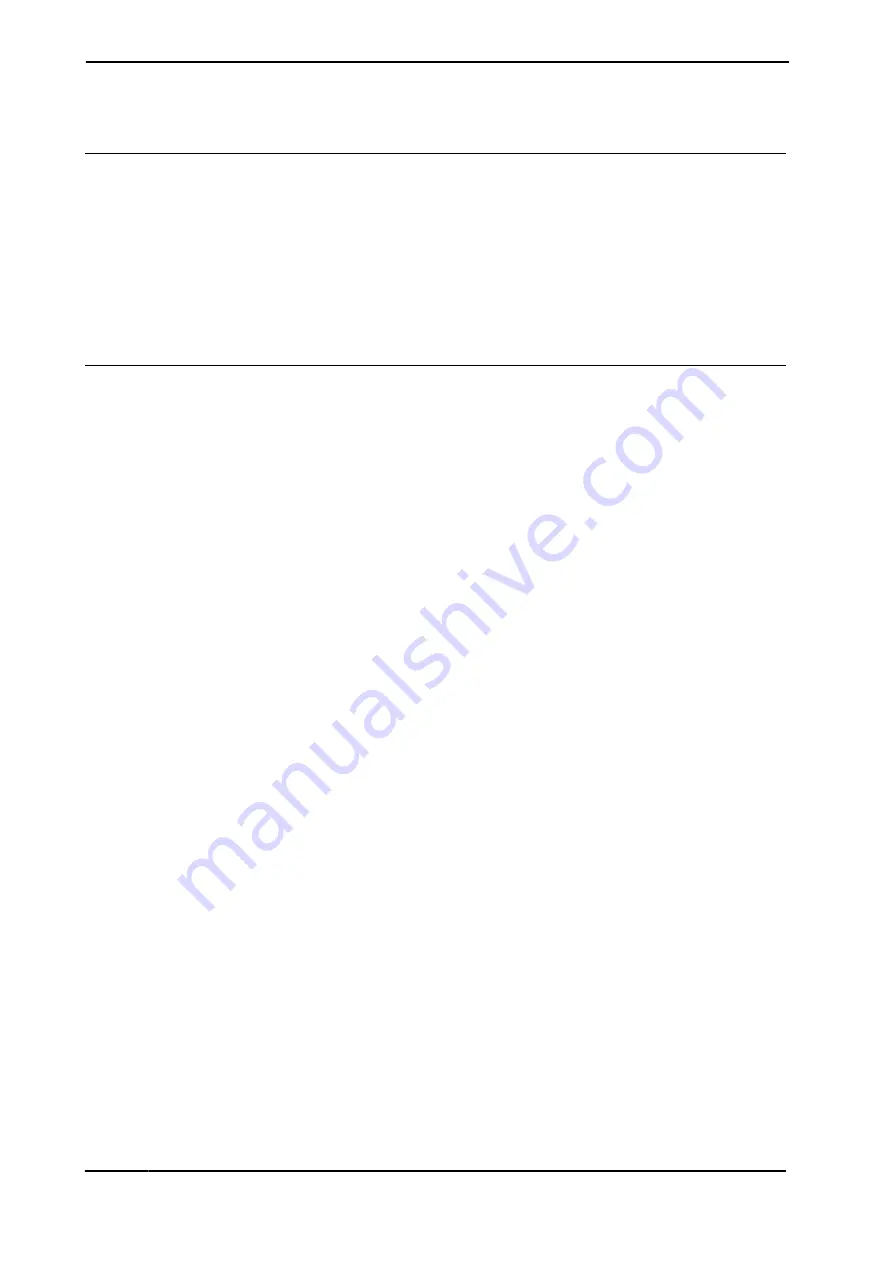
Product documentation, M2004
3HAC023637-001 Revision: B
10
Application manuals
Specific applications (e.g. software or hardware options) are described in Application
manuals. An application manual can describe one or several applications.
An application manual generally contains information about:
•
The purpose of the application (what it does and when it is useful)
•
What is included (e.g. cables, I/O boards, RAPID instructions, system parameters)
•
How to use the application
•
Examples of how to use the application
Operating manuals
This group of manuals is aimed at those having first hand operational contact with the robot,
i.e. production cell operators, programmers and trouble shooters. The group of manuals
includes:
•
Getting started - IRC5 and RobotStudio Online
•
Operating manual - IRC5 with FlexPendant
•
Operating manual - RobotStudio Online
•
Trouble shooting manual for the controller and robot
Continued
Summary of Contents for IRB 1600 - 5/1,2 type A
Page 2: ......
Page 8: ...Table of Contents ...
Page 14: ...How to read the product manual 3HAC023637 001 Revision B 12 ...
Page 38: ...1 Safety 1 3 6 WARNING Safety risks during work with gearbox oil 3HAC023637 001 Revision B 36 ...
Page 100: ...3 Maintenance 3 5 1 Cleaning complete robot 3HAC023637 001 Revision B 98 ...
Page 176: ...4 Repair 4 7 2 Service work on gearboxes axes 3 4 5 and 6 3HAC023637 001 Revision B 174 ...
Page 186: ......
Page 212: ...7 Spare parts and exploded views 7 7 Spare parts options 3HAC023637 001 Revision B 210 ...
Page 215: ...Circuit diagram 3HAC 021351 003 Rev 00 Contents Sheet 2 Circuit diagram IRB 1600 ...
Page 216: ...Revision 00 sheet 101 Circuit diagram 3HAC 021351 003 List of contents ...
Page 217: ...Revision 00 sheet 102 Circuit diagram 3HAC 021351 003 Connection point location ...
Page 219: ...Revision 00 sheet 104 Circuit diagram 3HAC 021351 003 Motor axes 1 2 ...
Page 220: ...Revision 00 sheet 105 Circuit diagram 3HAC 021351 003 Feedback axes 1 2 ...
Page 221: ...Revision 00 sheet 106 Circuit diagram 3HAC 021351 003 Motor axes 3 4 ...
Page 222: ...Revision 00 sheet 107 Circuit diagram 3HAC 021351 003 Feedback axes 3 4 ...
Page 223: ...Revision 00 sheet 108 Circuit diagram 3HAC 021351 003 Motor axes 5 6 ...
Page 224: ...Revision 00 sheet 109 Circuit diagram 3HAC 021351 003 Feedback axes 5 6 ...
Page 227: ...Revision 00 sheet 113 Circuit diagram 3HAC 021351 003 Position indicator axis 1 options ...
Page 228: ......
Page 233: ......