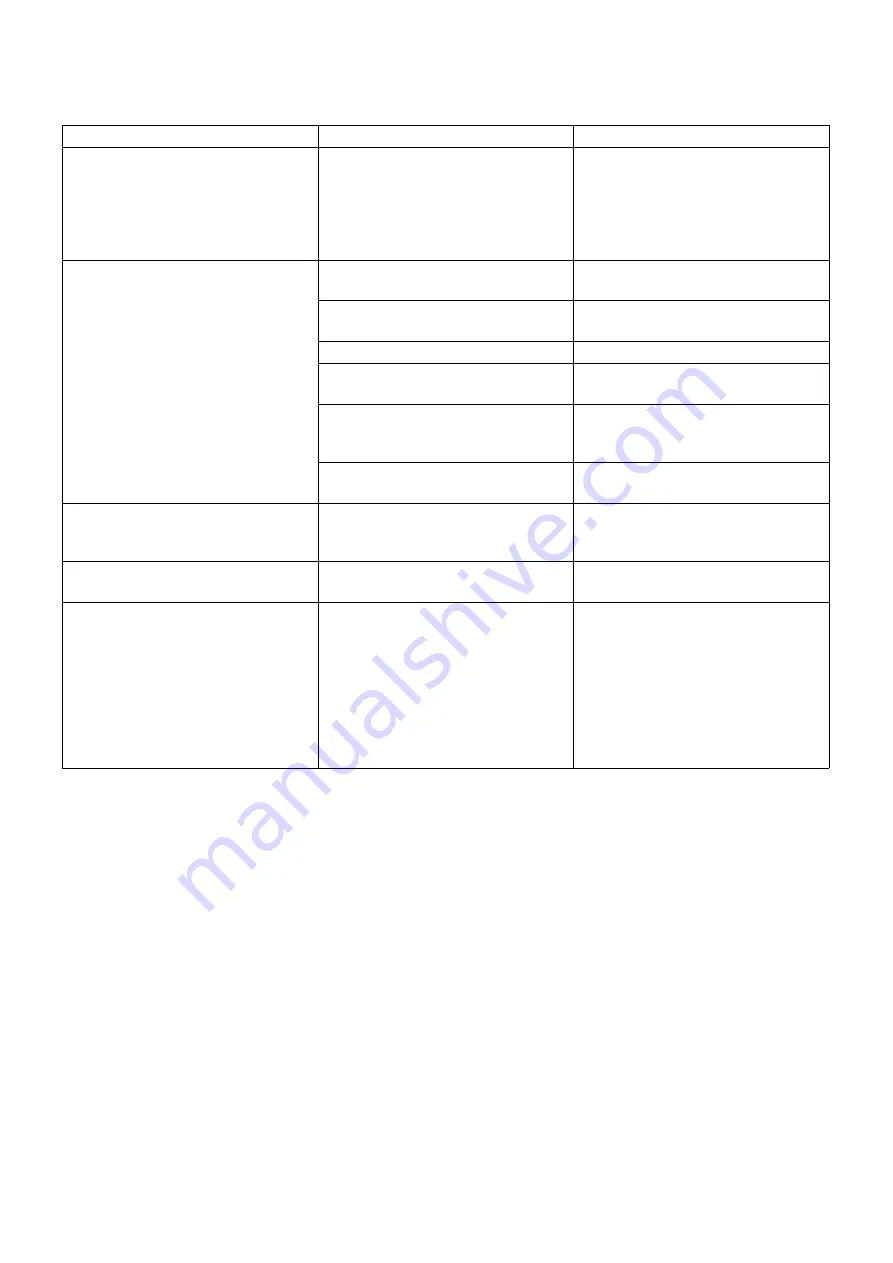
27
15. Troubleshooting
This section mainly describes how to handle hardware errors. Refer to the configuration program’s on-
line help for errors related to the software.
Table 8:
Error
Possible reason
Measures to be taken
Valve cannot be moved by actuator
Malfunction of actuator or valve (e.g.
stuffing box tightened too much)
Disconnect the actuator from the
valve.
If the actuator is working properly
then, the valve is likely to be defec-
tive. Otherwise, the actuator seems
to be the error source.
Actuator does not react
Wrong electronic unit or wrong data
Compare data lables of actuator and
electronic unit
Faulty electronic unit settings
Check / modify settings using the
configuration software
Faulty communication to DCS
Check wiring
Faulty wiring between the electronic
unit and the actuator
Check wiring
Motor / brake is defective
Check the winding resistances of the
motor and brake. Check the brake
fuse.
Digital inputs of electronic unit are
not connected
Connect
Actuator does not work in automatic
mode, although “AUT“ has been
selected in the configuration program
Digital input 1 (DI 1) has not been
connected.
-
Connect DI 1
-
Check software settings for digital
inputs
LEDs on the commissioning and ser-
vice field are flashing simultaneously
Actuator operating range has not
been adjusted properly
Adjust the actuator operating range
(see instruction for electronic unit).
Fault when approaching an end posi-
tion
Actuator is working in the limit range
of the position sensor
-
Move the actuator either manually
or with the LCP buttons to a posi-
tion beyond the end position (dis-
connect from valve if required).
-
Move actuator back. If required,
reconnect to to the valve (if appli-
cable)
-
Adapt actuator to new operating
range