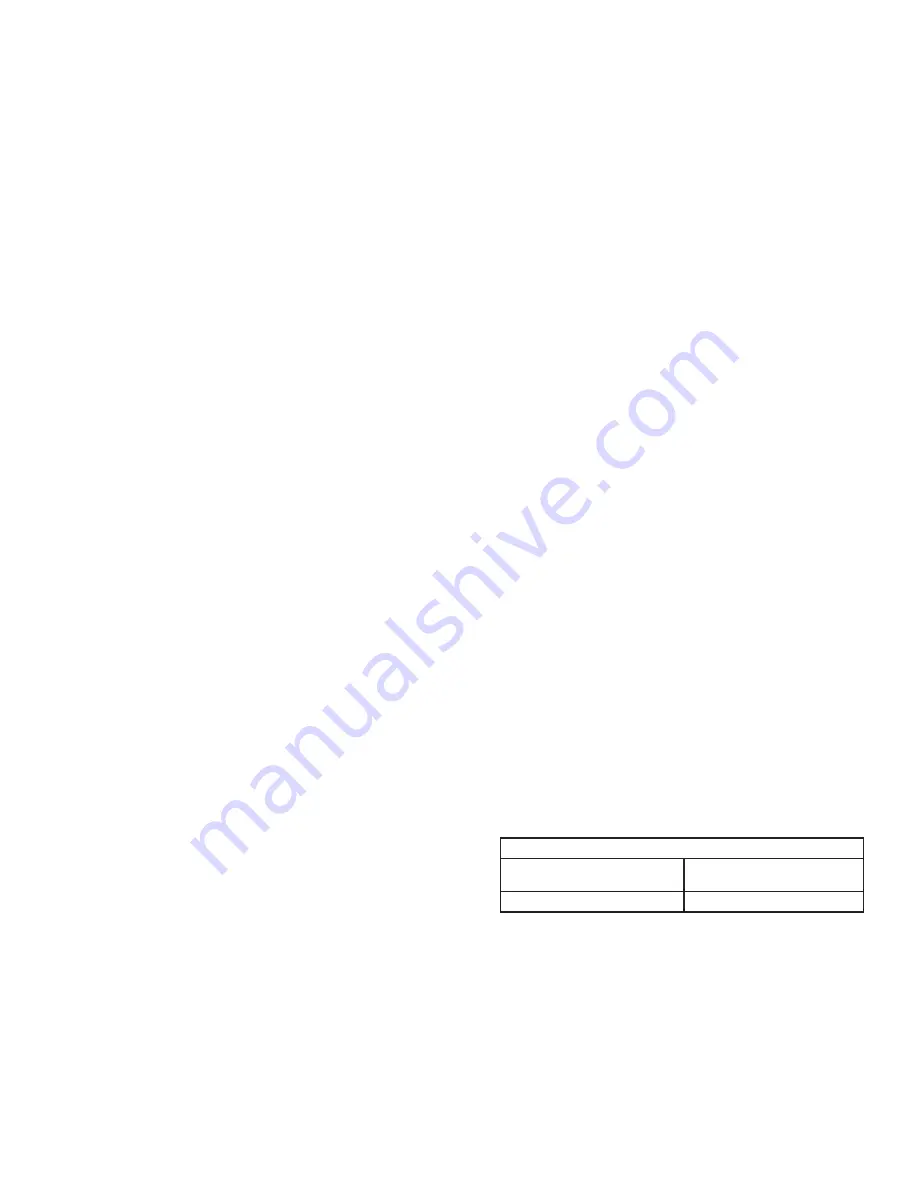
7
REPLACEMENT OF PARTS
A DODGE TORQUE-ARM Speed Reducer can be disassembled
and reassembled by careful attention to the instructions
following, using tools normally found in a maintenance
department.
Cleanliness is very important to prevent the introduction of dirt
into the bearings and other parts of the reducer. A tank of clean
solvent, an arbor press, and equipment for heating bearings
and gears should be available for shrinking these parts on
shafts.
Our factory is prepared to repair reducers for customers who
do not have proper facilities or who for any reason desire
factory service.
The oil seals are of the rubbing type and considerable care
should be used during disassembly and reassembly to avoid
damage to the surface on which the seals rub.
The keyseat in the input shaft as well as any sharp edges on
the output hub should be covered with tape or paper before
disassembly or reassembly. Also be careful to remove any burrs
or nicks on surfaces of the input shaft or output hub before
disassembly or reassembly.
ORDERING PARTS
When ordering parts for reducer, specify reducer size number,
reducer serial number, part name, part number and quantity.
It is strongly recommended that when a pinion or gear is
replaced, the mating gear or pinion be replaced also.
If the large gear on the output hub must be replaced, it is
recommended that an output hub assembly with a gear
assembled on the hub be ordered to secure undamaged
surfaces on the output hub where the oil seals rub. However, if it
is desired to use the old output hub, press the gear and bearing
off and examine the rubbing surface under the oil seal carefully
for possible scratching or other damage resulting from the
pressing operation. To prevent oil leakage at the shaft oil seals
the smooth surface of the output hub must not be damaged.
If any parts must be pressed from a shaft or from the output
hub, this should be done before ordering parts to make sure
that none of the bearings or other parts are damaged in
removal. Do not press against outer race of any bearing.
Because old shaft oil seals may be damaged in disassembly it
is advisable to order replacements for these parts.
REMOVING REDUCER FROM SHAFT
WARNING: External loads may cause machine movement.
Block machine before removing any drive train
components. Failure to observe these precautions could
result in bodily injury.
STRAIGHT BORE
Loosen screws in both output hub collars. Remove the collar
next to end of shaft. This exposes three puller holes in output
hub to permit use of wheel puller. In removing reducer from
shaft be careful not to damage ends of hub.
TAPER BUSHED
1. Remove bushing screws.
2. Place the screws in the threaded holes provided in the
bushing flanges. Tighten the screws alternately and
evenly until the bushings are free on the shaft. For ease of
tightening screws make sure screw threads and threaded
holes in bushing flanges are clean.
3. Remove the outside bushing, the reducer and then the
inboard bushing.
DISASSEMBLY
1. Position reducer on its side and remove all bolts. Gently tap
the output hub and input shaft with a soft hammer (rawhide
not a lead hammer) to separate the housing halves. Open
housing evenly to prevent damage to the parts inside.
2. Lift shaft, gear and bearing assemblies from housing.
3. Remove seals from housing.
REASSEMBLY
1. Output Hub Assembly:
Heat gear to 325"F to 350"F to
shrink onto hub. Heat bearings to 250"F to 270"F to shrink
onto hub. Any injury to the hub surfaces where the oil seals
rub will cause leakage making it necessary to use a new
hub.
2. Input Shaft Assembly:
Shaft and pinion are integral. Press
bearings on shaft. Press against inner (not outer) race of
bearings.
3. Drive the two dowel pins into place in the right-hand
housing half. Position right half of housing (as shown in
drawing) on blocks to allow clearance for protruding end of
output hub.
4. Place output hub assembly in housing half. Place input
shaft assembly in housing half. Tap lightly with a soft
hammer (rawhide not lead hammer) until bearings are
properly seated in the housing. Make sure that the snap
rings on the O.D. of the bearings come into contact with the
housing.
5. Clean housing flange surfaces on both halves, making
sure not to nick or scratch flange face. Place a new bead
of gasket replacer on flange face and spread evenly over
entire flange leaving no bare spots. Note: If reducer was
originally supplied with a housing gasket, do not use gasket
replacer. Reorder gasket per part number given in parts list.
Place other housing half into position and tap with a soft
hammer until housing bolts can be used to draw housing
halves together. Torque housing bolts per torque values
listed below:
Housing Bolt Torque Values
Reducer Size
Recommended Torque
(in.-lbs.)
TXT105, TXT205
360
6. Extreme care should be used in installing seals on input
shaft and output hub to avoid damage to seals due to
contact with sharp edges of the keyseat in the input shaft
or the retaining ring groove in the output hub. This danger
of damage and consequent oil leakage can be decreased
by covering the keyseat and groove with tape or paper
which can be removed subsequently. Chamfer or deburr
housing bore if end of bore is sharp or rough. Fill cavity
between lips of seal with grease. Seals should be pressed
or tapped with a soft hammer evenly into place in the
housing; apply force only on outer corner seals. A slight oil
leakage at the seals may be evident during initial running in,
but will disappear unless the seals have been damaged.