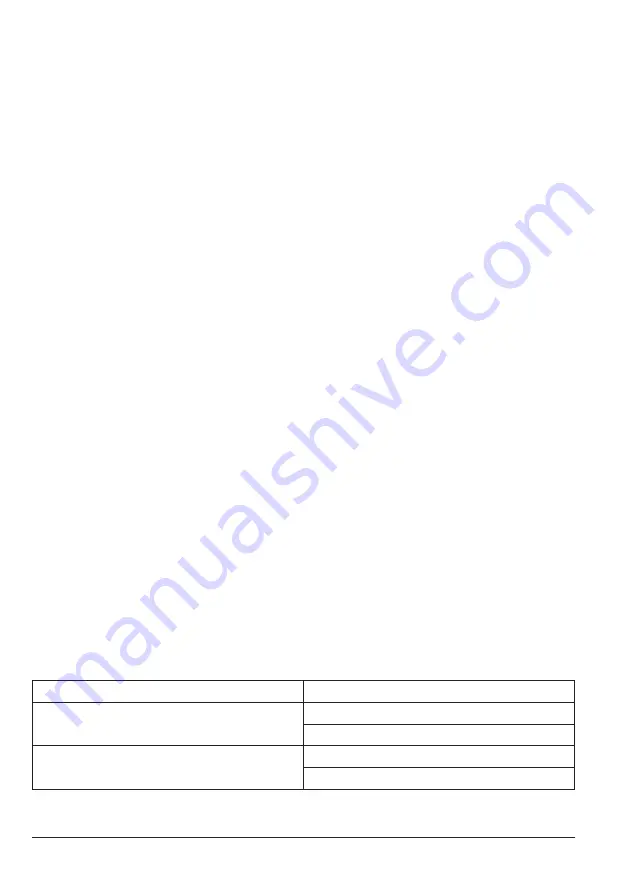
2-2
MN705
Motor Armature
Connect motor armature leads A+ and A-terminals and tighten to correct torque (Table 2-1).
The armature fuse provides overload protection for the motor and control. The factory installed fuse
is rated for maximum horsepower (type SC-40, 40Amp). To provide proper protection for motors rated
less than maximum, use a fuse sized at approximately 1.7 times the DC amperage rating of the motor.
Ground Connection
Connect an earth ground conductor to the green ground screw terminal on case (not shown). Tighten
to correct torque - 20 lb-in.
Field Connection
Shunt wound field motors only. Connect motor field to terminals F+ and F- (for full voltage 200 VDC),
or to terminals F+ and L1 (for half voltage 100 VDC) and tighten to correct torque (Table 2-1).
Control Circuit Wiring
For Speed Potentiometer, Enable, Inhibit, and Tachometer wiring, use terminals P1, P2, P3, E, I1, I2, 7V,
50V, J1, and J2, (remove J1 – J2 jumper for Tach Feedback) and tighten to correct torque (Table 2-1).
The control circuit fuse (not shown) provides protection for the Speed Control Module, power bridge
and field supply. The factory installed fuse is type 3AG, 4Amp, (or equivalent).
Speed Potentiometer Connection
A 5K ohm speed potentiometer is provided with each control. Connect the speed pot to the Control
Circuit Terminal strip, terminals P1, P2, and P3 and tighten to correct torque (Table 2-1)and tighten to
4.4 lb-in.
ENABLE
WARNING: When the Enable jumper is installed, the drive and motor will start and run when AC power is applied,
when power is restored after a momentary power loss, or after an overload or TCL fault is reset. The
user must ensure that automatic start up of the driven equipment will not cause injury to operating
personnel or damage to the driven equipment. The user is responsible for providing suitable audible or
visual alarms or other devices to indicate that the drive may start at any moment. Failure to observe
this warning could result in severe bodily injury or loss of life.
The BC155 can be started and stopped with the Enable Circuit, (open to stop), using a Switch or
contact connected to terminals ‘E’ and ‘P3’ on the Control Terminal strip. Remove the factory installed
jumper between the ‘E’ and ‘P3’ terminals (Figure 2-1) before connecting and using the Enable Circuit.
INHIBIT
The BC155 can be started and stopped with an Inhibit Circuit using a switch or contact, (close to stop),
connected to terminals ‘I1’ and ‘I2’ on the Control Terminal strip. When the switch or contact is closed,
the motor will coast to stop. When the switch or contact is opened, the motor will accelerate to the
speed set with the speed pot.
DC TACHOMETER CONNECTION
A DC tachometer can be used for speed regulation of 1% of set speed. If using a tachometer, remove
the factory installed jumper wire from terminals J1 and J2 terminal strip Figure 2-1.
Set IR Comp trimpot to fully CCW position.
Table 2-2 Tachometer Connections
Tachometer Output Voltage Rating
Terminal Connection
7 Volts / 1000 RPM
(+) Lead to Terminal 7V
(-) Lead to Terminal I2 or F-
50 Volts / 1000 RPM
(+) Lead to Terminal 50V
(-) Lead to Terminal I2 or F-
Summary of Contents for BALDOR BC155
Page 1: ...6 15 Installation Operating Manual MN702 DC SCR Drives for BC155...
Page 4: ...ii MN702...
Page 12: ...2 6 MN705...
Page 13: ......
Page 14: ......