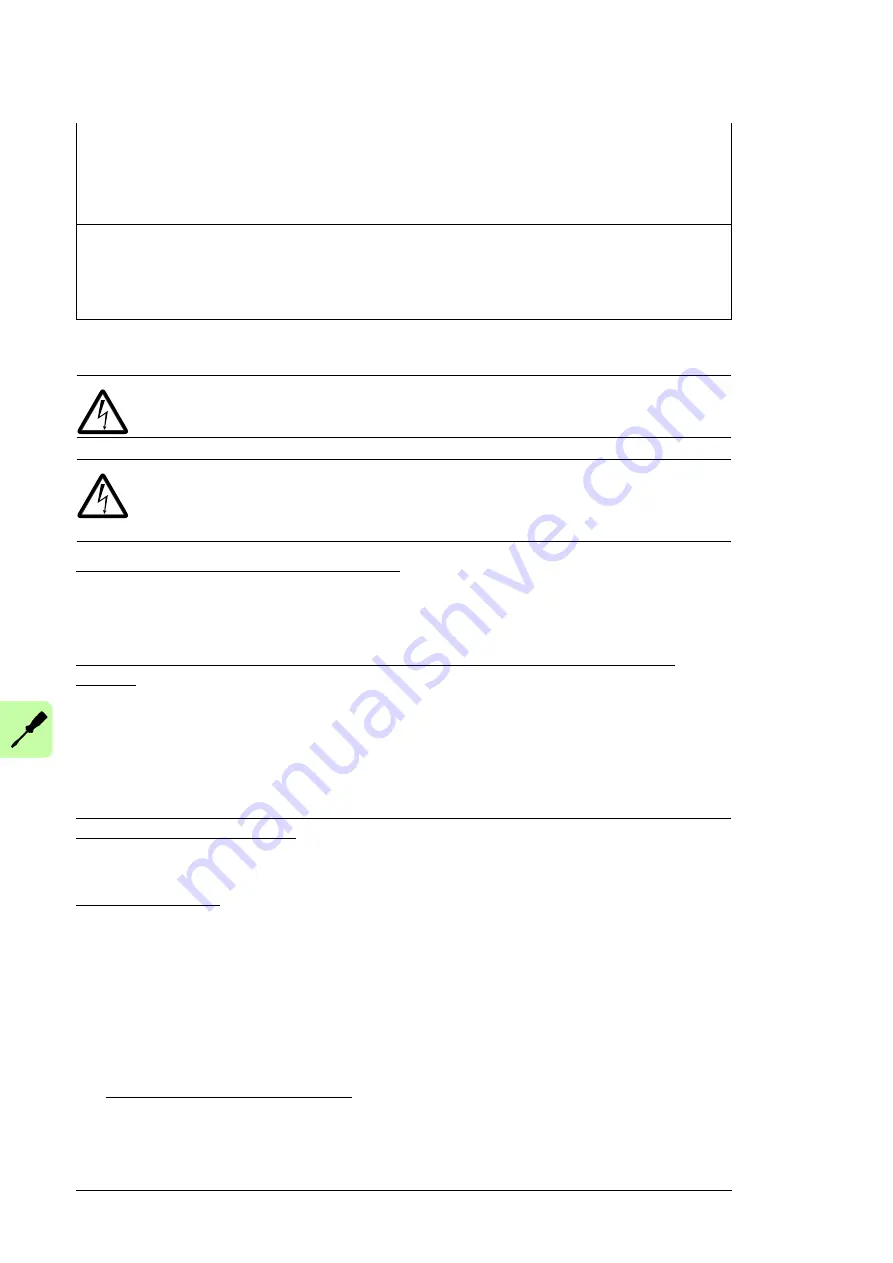
82 Electrical installation
Power cable connection procedure
WARNING!
Obey the safety instructions in chapter
. If you
ignore them, injury or death, or damage to the equipment can occur.
WARNING!
Apply grease to stripped aluminum conductors before attaching them
to non-coated aluminum cable lugs. Obey the grease manufacturer.’s instructions.
Aluminum-aluminum contact can cause oxidation in the contact surfaces
For the standard drive module configuration:
•
See the step-by-step installation drawings in
ACS880-04F quick installation guide
(3AXD50000044913 [multilingual])
•
Connect the full-size output cable connection terminals to the drive module.
For optional input power cable connection terminals and ground busbar assembly
(+H370):
•
Install the metallic shroud with ground bar as shown in section
shroud (standard and with ground bar [H370])
on page
•
Connect the full-size input power cable connection terminals in a similar way as the
motor cable connection terminals, see
ACS880-04F quick installation guide
(3AXD50000044913 [multilingual]).
For drive modules without full-size output cable connection terminals (0H371) and
IP20 shrouds (0B051), Connect the power cables directly to the drive module
input and output terminals with cable lugs or by busbars. Protect the power cable terminals
and electrical parts against contact and ground the drive module correctly.
Cabinet installation:
1. Run the motor cables from the motor to the cabinet. Ground the cable shields 360° at
the lead-through plate.
2. Twist the cable shields of the motor cables into bundles and connect them and any
separate ground conductors or cables to the ground terminal of the drive module or to
the cabinet ground bar.
3. Connect the phase conductors of the motor cables to terminals T1/U2, T2/V2 and
T3/W2
of the drive module. For the tightening torques, see page
.
4. Drive modules with D150: Run the power cables from the brake resistor to the
cabinet. Ground the cable shield (if present) 360° at the lead-through plate. Connect
the conductors to the R+ and R- terminals. For the tightening torques, see page
.
6
External brake resistor (optional, see page
)
7
Common mode filter (optional, see page
8
du/dt filter (optional, see page
9
The drive module frame must be connected to the cabinet frame. See section
on page
Note:
If there is a symmetrically constructed grounding conductor in the motor cable in addition to the conductive
shield, connect the grounding conductor to the grounding terminal at the drive and motor ends.
Do not use an asymmetrically constructed motor cable. Connecting its fourth conductor at the motor end
increases bearing currents and causes extra wear.
Summary of Contents for ACS880-04F
Page 1: ...ABB industrial drives Hardware manual ACS880 04F drive modules ...
Page 4: ......
Page 24: ...24 Introduction to the manual ...
Page 46: ...46 Guidelines for planning the mechanical installation ...
Page 102: ...102 Installation checklist ...
Page 106: ...106 Fault tracing ...
Page 135: ...Technical data 135 Declaration of Conformity ...
Page 136: ...136 Technical data ...
Page 140: ...140 Technical data ...
Page 142: ...142 Dimension drawings Standard configuration IP20 UL Open Type ...
Page 143: ...Dimension drawings 143 Drive module with options E208 and H370 IP20 UL Open Type ...
Page 144: ...144 Dimension drawings Drive module with options 0B051 E208 0H371 IP00 UL Open Type ...
Page 145: ...Dimension drawings 145 Drive module with options 0B051 E208 0H371 C217 IP00 UL Open Type ...
Page 146: ...146 Dimension drawings Drive module with options 0B051 0H371 IP00 UL Open Type ...
Page 147: ...Dimension drawings 147 Mounting plate 3AXD50000038119 ...
Page 148: ...148 Dimension drawings 3AXD50000038119 ...
Page 149: ...Dimension drawings 149 External control unit 3axd50000011687 ...
Page 150: ...150 Dimension drawings ...
Page 164: ...164 Safe torque off function ...