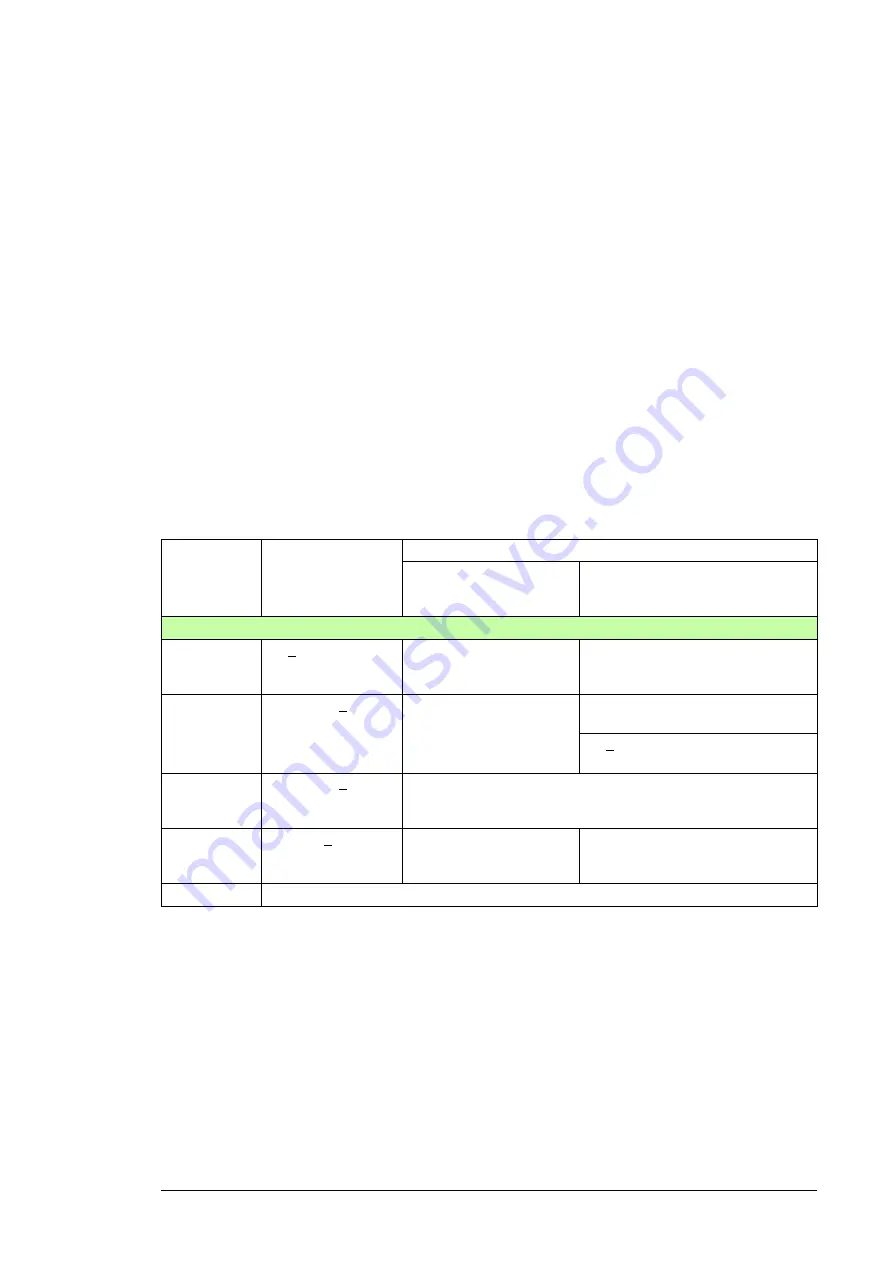
Guidelines for planning the electrical installation 59
Protecting the motor insulation and bearings
The drive uses modern IGBT inverter technology. Regardless of frequency, the drive
output has pulses of approximately the drive DC bus voltage with a very short rise time. Up
to twice bus voltage can be at the motor terminals, depending on the attenuation and
reflection properties of the motor cable and the terminals. The increased voltage can
cause additional stress on the motor and motor cable insulation.
Modern variable speed drives with their fast rising voltage pulses and high switching
frequencies can generate current pulses that flow through the motor bearings. This can
gradually erode the bearing races and rolling elements.
Optional d
u
/d
t
filters protect motor insulation system and reduce bearing currents. Optional
common mode filters mainly reduce bearing currents. Insulated N-end (non-drive end)
bearings protect the motor bearings.
Requirements table
The following table shows how to select the motor insulation system and when optional
ABB d
u
/d
t
filters, insulated N-end (non-drive end) motor bearings and ABB common mode
filters are required. Failure of the motor to fulfill the following requirements or improper
installation may shorten motor life or damage the motor bearings and voids the motor
warranty.
Motor type
Nominal AC supply
voltage
Requirement for
Motor insulation system
ABB d
u
/d
t
and common mode
filters, insulated N-end motor
bearings
ABB motors
Random-
wound M2_,
M3_ and M4_
U
N
< 500 V
Standard
+ N + CMF
Form-wound
HX_ and AM_
380 V <
U
N
< 690 V
Standard
P
N
<
500 kW:
+N + CMF
P
N
>
500 kW
+N + d
u
/d
t
+ CMF
Old* form-
wound HX_
and modular
380 V <
U
N
< 690 V
Check with the motor manufacturer.
Random-
wound HX_
and AM_ **
0 V <
U
N
< 500 V
Enamelled wire with fiber
glass taping
+ N + CMF
HDP
Consult the motor manufacturer.
* manufactured before 1.1.1998
** For motors manufactured before 1.1.1998, check for additional instructions with the motor manufacturer.
Summary of Contents for ACS880-04F
Page 1: ...ABB industrial drives Hardware manual ACS880 04F drive modules ...
Page 4: ......
Page 24: ...24 Introduction to the manual ...
Page 46: ...46 Guidelines for planning the mechanical installation ...
Page 102: ...102 Installation checklist ...
Page 106: ...106 Fault tracing ...
Page 135: ...Technical data 135 Declaration of Conformity ...
Page 136: ...136 Technical data ...
Page 140: ...140 Technical data ...
Page 142: ...142 Dimension drawings Standard configuration IP20 UL Open Type ...
Page 143: ...Dimension drawings 143 Drive module with options E208 and H370 IP20 UL Open Type ...
Page 144: ...144 Dimension drawings Drive module with options 0B051 E208 0H371 IP00 UL Open Type ...
Page 145: ...Dimension drawings 145 Drive module with options 0B051 E208 0H371 C217 IP00 UL Open Type ...
Page 146: ...146 Dimension drawings Drive module with options 0B051 0H371 IP00 UL Open Type ...
Page 147: ...Dimension drawings 147 Mounting plate 3AXD50000038119 ...
Page 148: ...148 Dimension drawings 3AXD50000038119 ...
Page 149: ...Dimension drawings 149 External control unit 3axd50000011687 ...
Page 150: ...150 Dimension drawings ...
Page 164: ...164 Safe torque off function ...