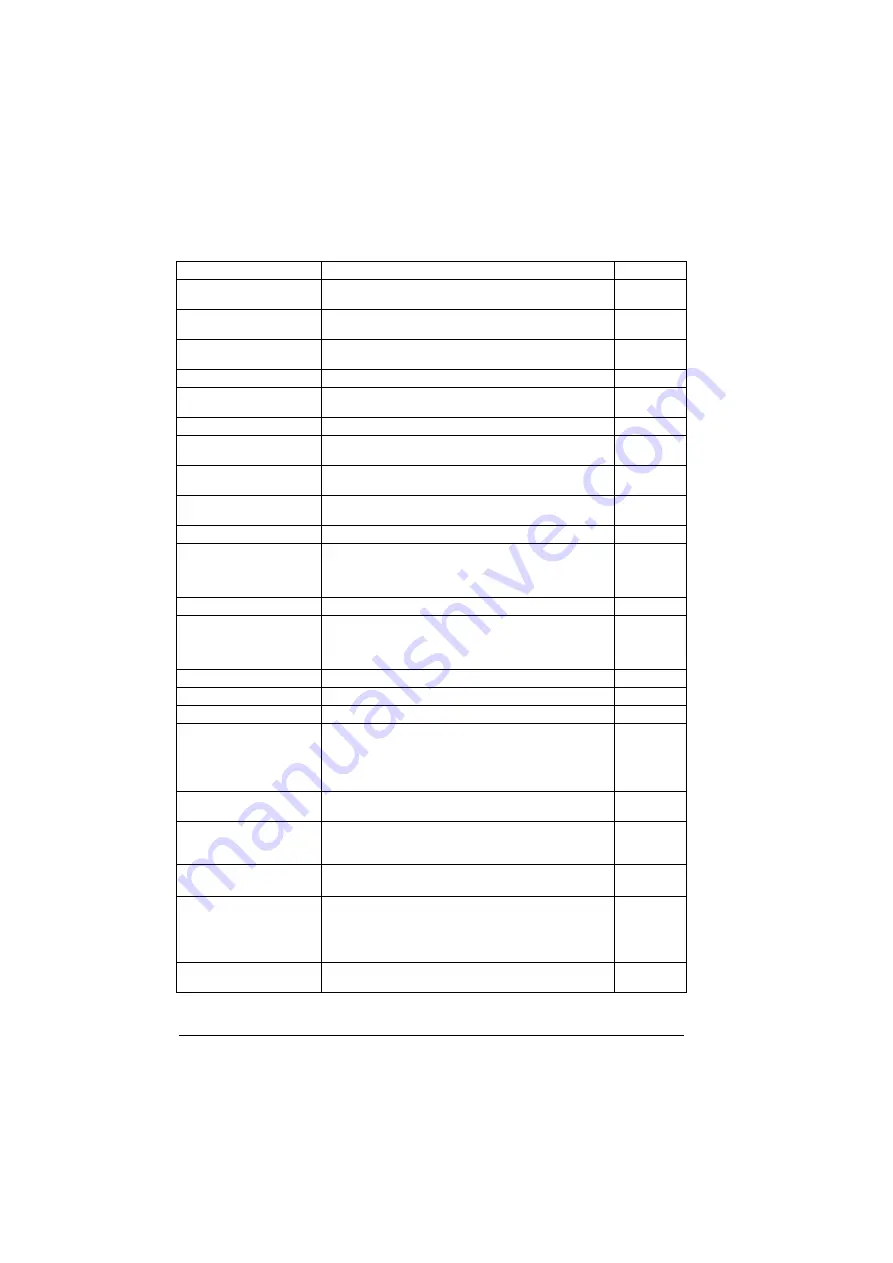
166 Parameters
Drive output power. A filter time constant for this signal can
be defined by parameter
-
-32768.00…
32767.00 kW
Output power.
See par.
Output power in percent of the nominal motor power.
-
-300.00… 300.00%
Output power.
1 = 1%
Output power in percent of the nominal drive power.
-
-300.00… 300.00%
Output power.
1 = 1%
Estimated mechanical power at motor shaft. The unit is
selected by parameter
.
-
-32768.00…
32767.00 hp or kW
Motor shaft power.
See par.
Amount of energy that has passed through the drive (in either
direction) in full gigawatt-hours. The minimum value is zero.
-
0…65535 GWh
Energy in GWh.
1 = 1 GWh
Amount of energy that has passed through the drive (in either
direction) in full megawatt-hours. Whenever the counter rolls
over,
is incremented. The
minimum value is zero.
-
0…1000 MWh
Energy in MWh.
1 = 1 MWh
Amount of energy that has passed through the drive (in either
direction) in full kilowatt-hours. Whenever the counter rolls
over,
is incremented. The
minimum value is zero.
-
0…1000 kWh
Energy in kWh.
10 = 1 kWh
Used flux reference in percent of nominal flux of motor.
-
0…200%
Flux reference.
1 = 1%
Torque that corresponds to 100% of nominal motor torque.
The unit is selected by parameter
.
Note:
This value is copied from parameter
if entered. Otherwise the value is calculated
from other motor data.
-
0.000…4000000
N·m or lb·ft
Nominal torque.
1 = 100 unit
Ambient temperature of the drive.
Note:
This parameter is applicable only for frames R6 or
larger.
-
°C or °F
Temperature
1 = 1 °
Current hour energy consumption. This is the energy of the
last 60 minutes (not necessarily continuous) the drive has
been running, not the energy of a calendar hour. The value is
set to the value before the power cycle when the drive is
again up and running.
-
0.00… 1000000.00
kWh
Energy.
1 = 1 kWh
No.
Name/Value
Description
Def/FbEq16
Summary of Contents for ACS560
Page 1: ...ABB GENERAL PURPOSE DRIVES ACS560 standard control program Firmware manual...
Page 4: ...4...
Page 30: ...30 Start up control with I O and ID run...
Page 32: ...32 Using the control panel...
Page 100: ...100 Program features...
Page 153: ...Control macros 153...
Page 160: ...160...
Page 374: ...374 Parameters...
Page 408: ...408 Additional parameter data...
Page 466: ...466 Fieldbus control through the embedded fieldbus interface EFB...
Page 504: ...504 Control chain diagrams...
Page 508: ...508 Parameterization with drive composer...
Page 512: ...512 Parameterization with automation builder drive manager...