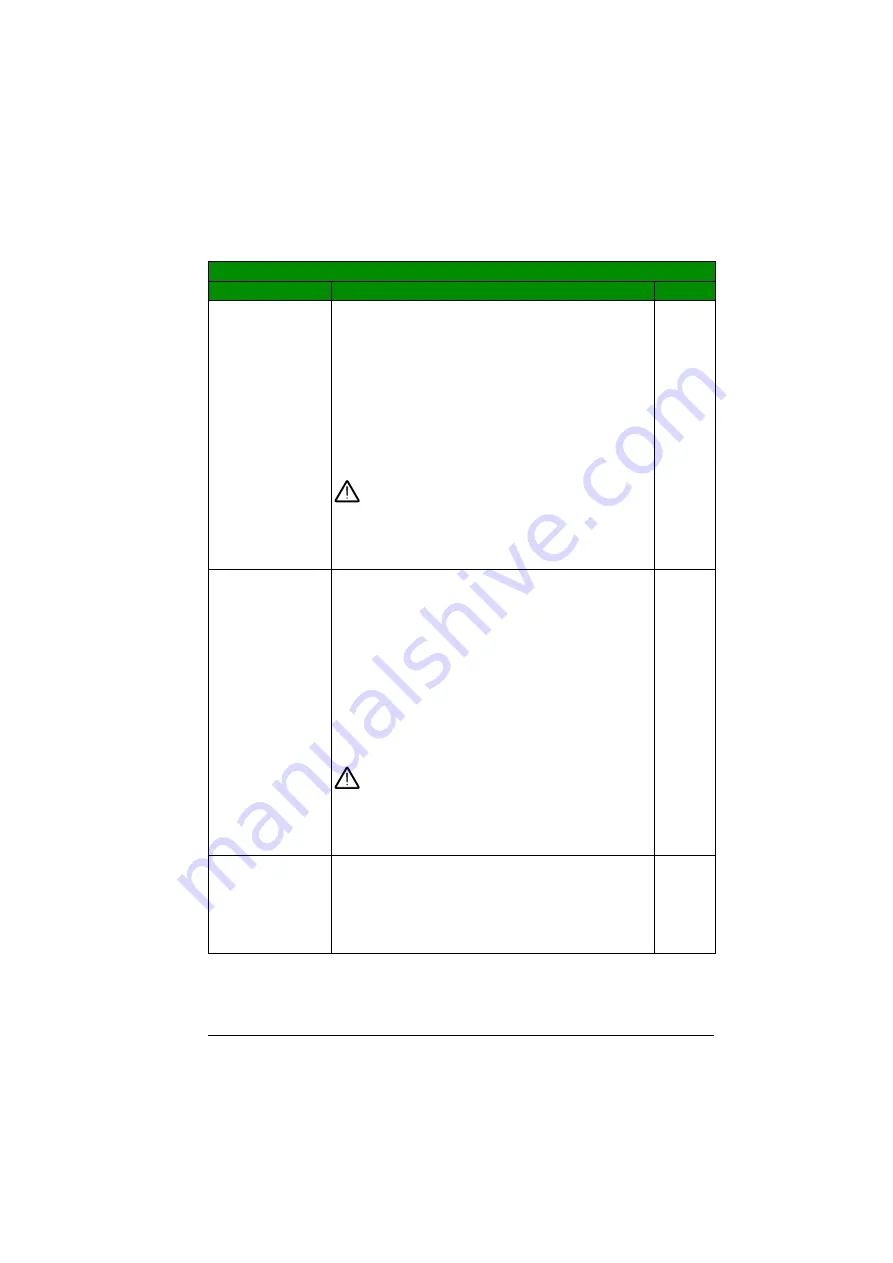
Actual signals and parameters 227
DC MAGN
The drive pre-magnetizes the motor with DC current before
the start. The pre-magnetizing time is defined by parameter
If parameter
value is
, DC magnetizing guarantees
the highest possible break-away torque when the pre-
magnetizing is set long enough.
Note:
Starting the drive connected to a rotating motor is not
possible when
is selected. When a permanent
magnet synchronous motor is used, alarm
) is generated.
WARNING!
The drive will start after the set pre-
magnetizing time has passed even if the motor
magnetization is not completed. In applications where a full
break-away torque is essential, always ensure that the
constant magnetizing time is long enough to allow
generation of full magnetization and torque.
2
TORQ BOOST Torque boost should be selected if a high break-away
torque is required. Used only when parameter
setting is
.
The drive pre-magnetizes the motor with DC current before
the start. The pre-magnetizing time is defined by parameter
Torque boost is applied at start. Torque boost is stopped
when output frequency exceeds 20 Hz or when it is equal to
the reference value. See parameter
Note:
Starting the drive connected to a rotating motor is not
possible when
is selected.
WARNING!
The drive will start after the set pre-
magnetizing time has passed although the motor
magnetization is not completed. In applications where a full
break-away torque is essential, always ensure that the
constant magnetizing time is long enough to allow
generation of full magnetization and torque.
4
SCAN START
Frequency scanning flying start (starting the drive
connected to a rotating motor). Based on frequency
scanning (interval
) to identify the frequency. If frequency identification
fails, DC magnetization is used (see selection
).
Not for multimotor drives.
6
All parameters
No.
Name/Value
Description
Def/FbEq
Summary of Contents for ACS355 series
Page 1: ...ABB machinery drives User s manual ACS355 drives ...
Page 4: ......
Page 16: ...16 ...
Page 32: ...32 Operation principle and hardware description ...
Page 58: ...58 Electrical installation ...
Page 74: ...74 Start up control with I O and ID run ...
Page 106: ...106 Control panels ...
Page 120: ...120 Application macros ...
Page 178: ...178 Program features ...
Page 338: ...338 Fieldbus control with embedded fieldbus ...
Page 368: ...368 Fault tracing ...
Page 404: ...404 Dimension drawings ...
Page 410: ...410 Appendix Resistor braking ...
Page 434: ...434 Appendix Permanent magnet synchronous motors PMSMs ...