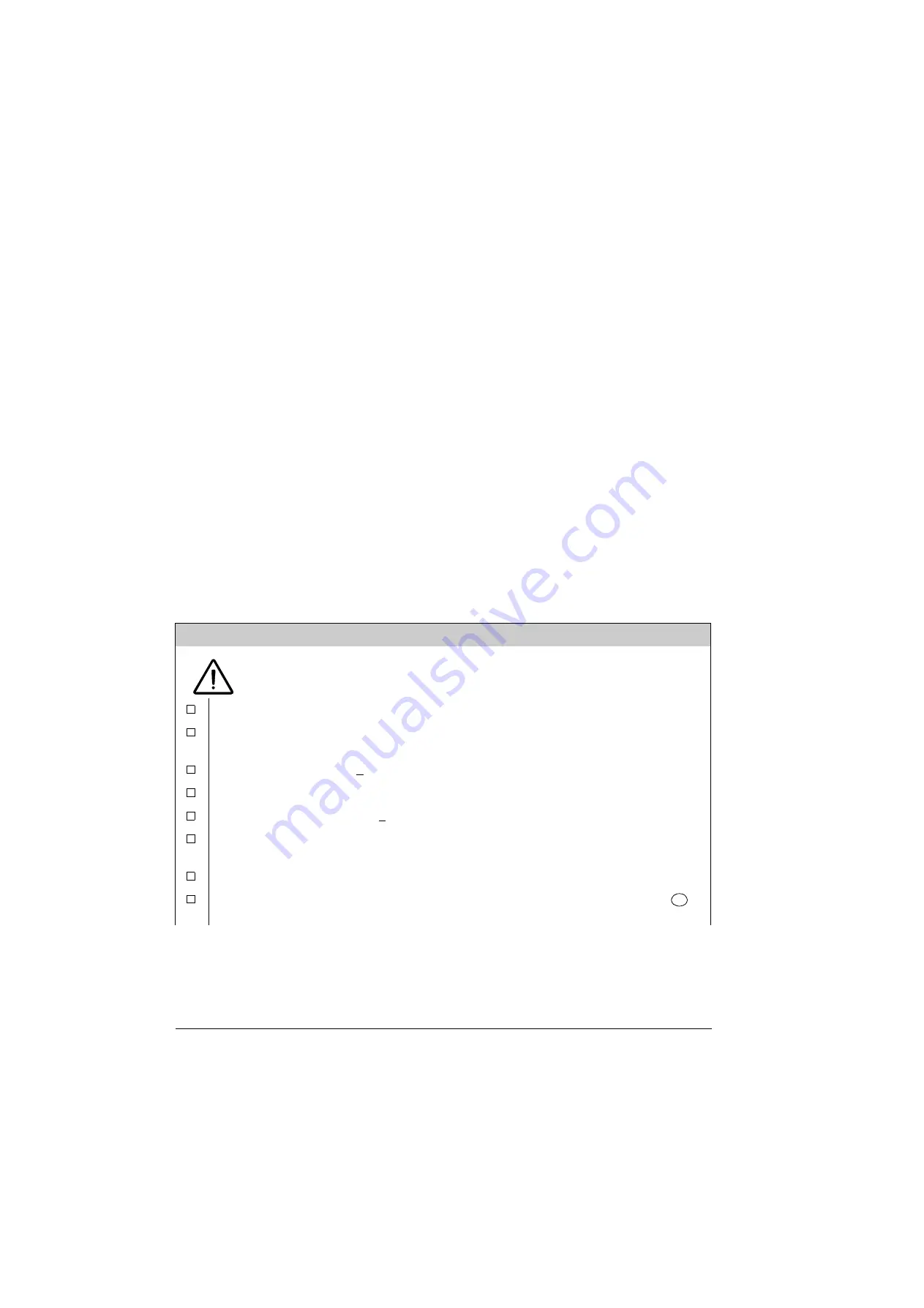
Start-up, control with I/O and ID Run
54
How to perform the ID Run
The drive estimates motor characteristics automatically when the drive is started for
the first time and after any motor parameter (group
) is changed.
ID RUN has value 0 (OFF/IDMAGN).
In most applications there is no need to perform a separate ID Run. The ID Run
should be selected if:
• vector control mode is used [parameter 9904 = 1 (VECTOR:SPEED) or
2 (VECTOR:TORQ)], and
• operation point is near zero speed and/or
• operation at torque range above the motor nominal torque, over a wide speed
range, and without any measured speed feedback (i.e without a pulse encoder) is
needed.
Note:
) are changed after the ID
Run, it must be repeated.
ID Run procedure
The general parameter setting procedure is not repeated here. For Basic Control
Panel, see page
and for Assistant Control Panel, see page
in chapter
. The ID Run cannot be performed without a control panel.
PRE-CHECK
WARNING!
The motor will run at up to approximately 50…80% of the nominal speed
during the ID Run. The motor will rotate in the forward direction.
Ensure that it is
safe to run the motor before performing the ID Run!
De-couple the motor from the driven equipment.
If parameter values (group
) are changed
before the ID Run, check that the new settings meet the following conditions:
MINIMUM SPEED < 0 rpm
MAXIMUM SPEED > 80% of the motor rated speed
MAXIMUM CURRENT >
I
2N
MAX TORQUE 1 > 50% or
MAX TORQUE 2 > 50%, depending on which limit
is in use according to parameter
MAX TORQUE SEL
Check that the Run Enable signal is on (parameter
).
Ensure that the panel is in local control (LOC shown on the left / at the top). Press key
to
switch between local and remote control.
LOC
REM
Summary of Contents for ACS350 Series
Page 1: ...ACS350 User s Manual ACS350 Drives 0 37 22 kW 0 5 30 HP ...
Page 4: ......
Page 8: ...Safety 8 ...
Page 18: ...Table of contents 18 ...
Page 24: ...Hardware description 24 ...
Page 44: ...Installation checklist 44 ...
Page 56: ...Start up control with I O and ID Run 56 ...
Page 140: ...Program features 140 ...
Page 242: ...Actual signals and parameters 242 ...
Page 266: ...Fieldbus control with embedded fieldbus 266 ...
Page 284: ...Fault tracing 284 ...
Page 288: ...Maintenance and hardware diagnostics 288 ...
Page 309: ...Dimensions 309 Frame size R2 IP20 NEMA 1 3AFE68586658 A Frame size R2 IP20 NEMA 1 VAR EMC ...
Page 311: ...Dimensions 311 Frame size R3 IP20 NEMA 1 3AFE68579872 B Frame size R3 IP20 NEMA 1 VAR EMC ...
Page 313: ......