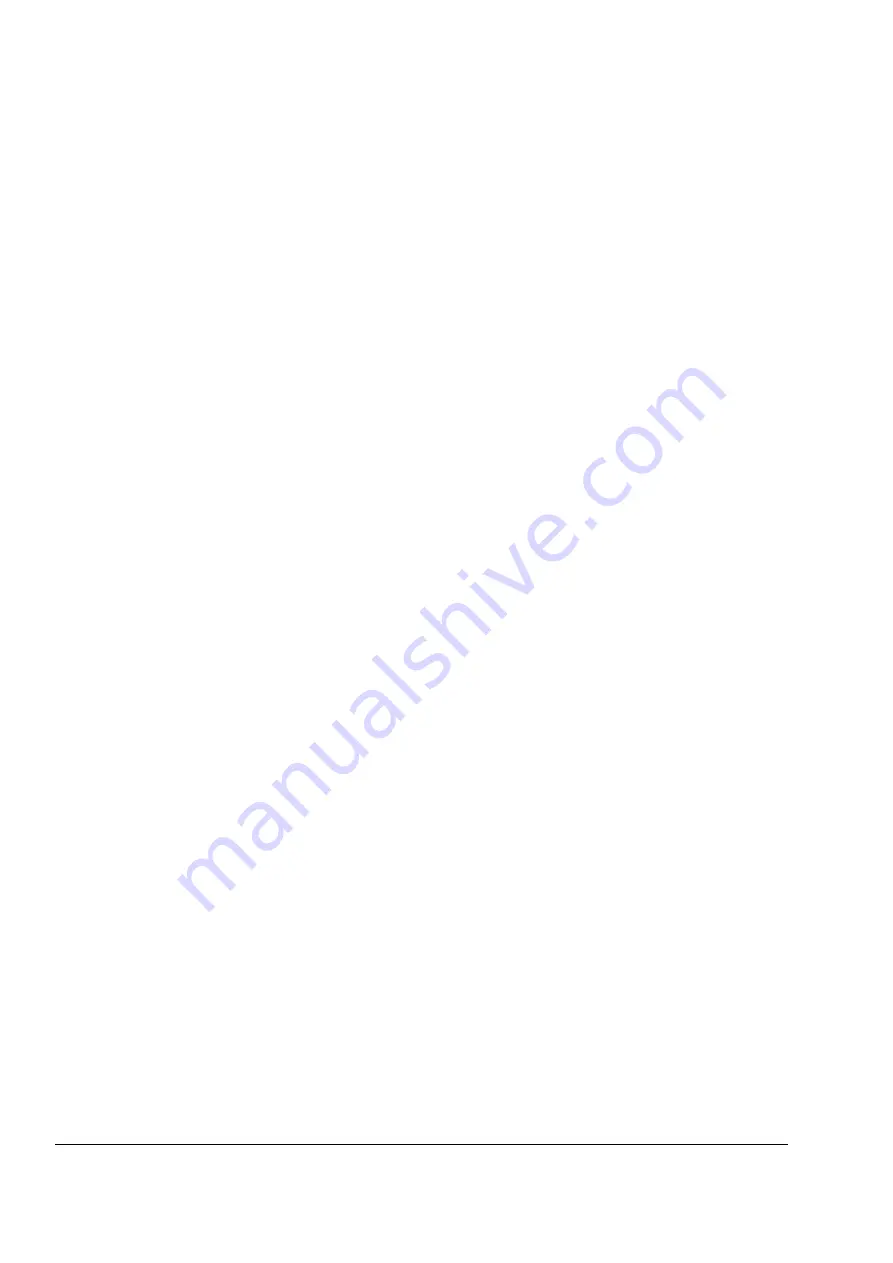
Program features
78
Preprogrammed faults
Overcurrent
The Overcurrent trip limit is 3.5 * I
hd
(nominal motor current for heavy duty use).
There are several sources of the overcurrent trip:
• Software trip (time level 100 ms, level = 97% of measurement scale)
• Hardware level trip (97% of measurement scale for 35 ms)
• Hardware derivative trip (12.5% of measurement scale for 75 ms)
• Hardware level trip in parallel connected units by PBU logic (94% of
measurement scale for 75 ms)
A fault “
OVERCURRENT
” is given during overcurrent condition.The current
measurement is calibrated automatically during the start procedure.
DC overvoltage
The DC overvoltage trip limit is 1.3 * 1.35 *
U
1max
, where
U
1max
is the maximum
value of the mains voltage range. For 400 V units,
U
1max
is 415 V. For 500 V units,
U
1max
is 500 V. For 690 V units,
U
1max
is 690 V.
The actual voltage in the intermediate circuit corresponding to the mains voltage trip
level is 728 V DC for 400 V units, 877 V DC for 500 V units, and 1210 V DC for 690 V
units. See the following
Figure: DC voltage control and trip limits.
DC undervoltage
The DC undervoltage trip limit is 0.6 *1.35 *
U
1min
, where
U
1min
is the minimum
value of the mains voltage range. For 400 V and 500 V units,
U
1min
is 380 V. For 690
V units,
U
1min
is 525 V.
The actual voltage in the intermediate circuit corresponding to the mains voltage trip
level is 307 V DC for 400 V and 500 V units, and 425 V DC for 690 V units. See the
following
Summary of Contents for ACS 800 Series
Page 1: ...ACS800 Firmware Manual Crane Control Program N697 ...
Page 4: ......
Page 26: ...Start up and control through the I O interface 26 ...
Page 36: ...Quick start up guide 36 ...
Page 52: ...Control panel 52 ...
Page 105: ...Program features 105 Figure Control diagram for Shaft synchronisation executed in 20 ms ...
Page 128: ...Program features 128 ...
Page 150: ...Application macros control location EXT1 EXT2 150 ...
Page 228: ...Actual signals and parameters 228 ...
Page 299: ...Adaptive Programming examples for crane control 299 ...
Page 305: ...Adaptive Programming examples for crane control 305 ...
Page 318: ...Analogue Extension Module 318 ...
Page 332: ...Additional data actual signals and parameters 332 ...
Page 334: ...DriveWindow 334 ...
Page 335: ...Control block diagrams 335 Control block diagrams ...
Page 336: ...Control block diagrams 336 ...
Page 337: ...Control block diagrams 337 ...
Page 338: ...Control block diagrams 338 ...
Page 340: ...www abb com drives www abb com drivespartners Contact us 3AFE68775230 Rev E EN 2012 09 25 ...