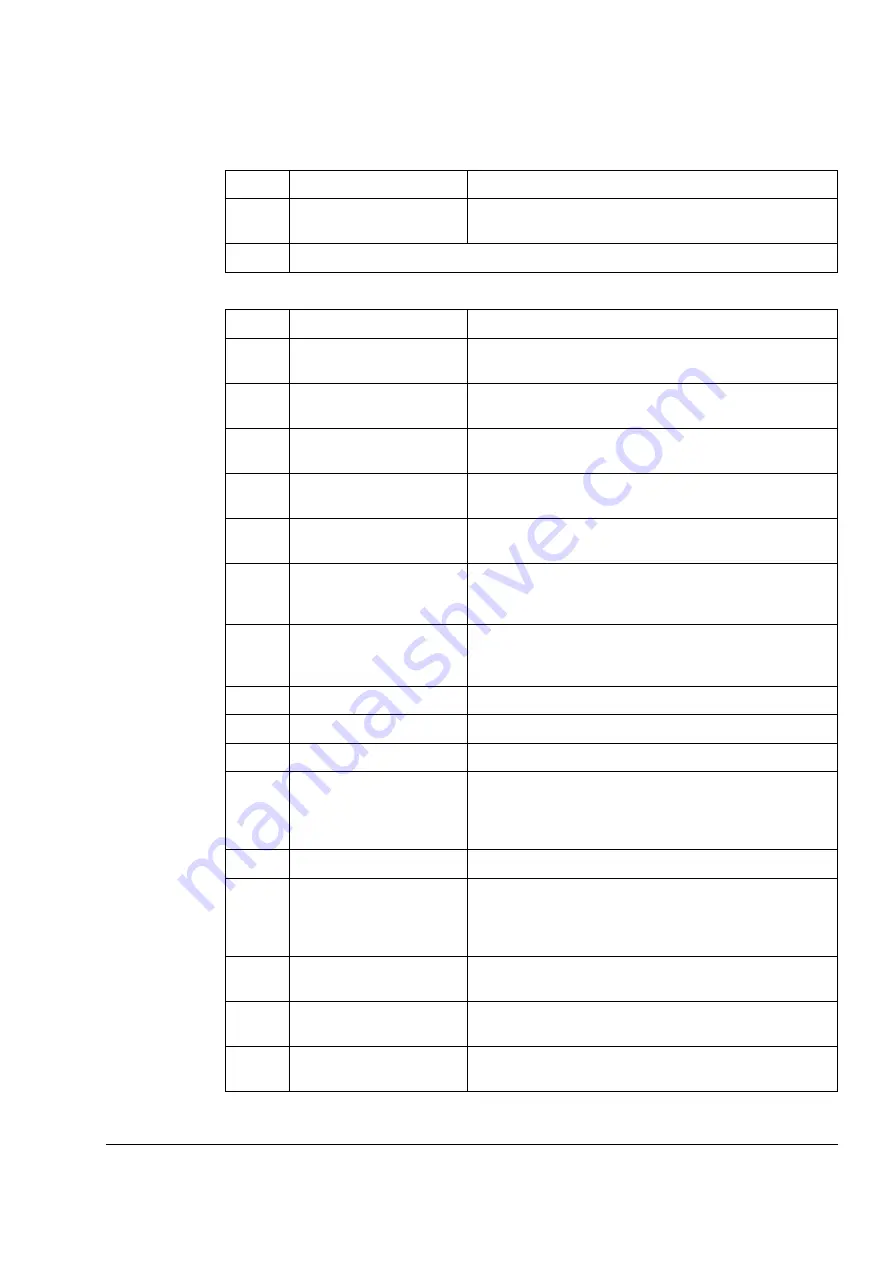
Fieldbus control
275
03.31 ALARM WORD 6
03.32 CRANE STATUS WORD
Bit
Name
Description
0
INV OVERTEMP
For the possible causes and remedies, see chapter
.
1 … 15
Reserved
Bit
Name
Description
0
SLOW DOWN ENABLED
Slow down enabled by the activation of the configured
input. See Par.
1
FAST STOP ENABLED
Fast Stop enabled by the activation of the configured input.
See Par.
2
HIGH END LIMIT INPUT
ENABLED
High-end limit enabled by the activation of the configured
input. See Par
3
LOW END LIMIT INPUT
ENABLED
Low-end limit enabled by the activation of the configured
input. See Par.
4
LOAD SPEED CTRL
ENABLED
The Load speed control function is activated using Par
5
LOAD SP UP LIM
The speed is limited in the forward direction by the Load
speed control function. See chapter
for more
details.
6
LOAD SP DW LIM
The speed is limited in the reverse direction by the Load
speed control function. See chapter
for more
details.
7
SYNC ENABLED
Synchro control active. See Par.
8
POWER ON ACK SIGNAL
Start Interlock DI active.
9
BRK LONG TIME
Brake long time sequence active. See Par.
10
LOAD SPEED CTRL ERR
The Load speed control function is activated but not able to
calculate the speed limit according to the motor current
because of wrong configuration of parameters in group
77.
See chapter
for more details.
11
WATCH DOG BIT-N
12
CTRL LOC DIFF
EXT1/EXT2 mismatch. For more information, see sections
Master/Follower use of several drives (Only in EXT2
Control)
and
Control location EXT1/EXT2 supervision
.
13
ZERO POS WARN
Zero position warning from joystick Zero position. For more
information, see Par.
14
START HIGH
Crane start signal high when power is switched on, or
running to direction where end limit sensor is high.
15
SYNCH ERROR BLOCK
LEVEL
Synch error correction is blocked.
Summary of Contents for ACS 800 Series
Page 1: ...ACS800 Firmware Manual Crane Control Program N697 ...
Page 4: ......
Page 26: ...Start up and control through the I O interface 26 ...
Page 36: ...Quick start up guide 36 ...
Page 52: ...Control panel 52 ...
Page 105: ...Program features 105 Figure Control diagram for Shaft synchronisation executed in 20 ms ...
Page 128: ...Program features 128 ...
Page 150: ...Application macros control location EXT1 EXT2 150 ...
Page 228: ...Actual signals and parameters 228 ...
Page 299: ...Adaptive Programming examples for crane control 299 ...
Page 305: ...Adaptive Programming examples for crane control 305 ...
Page 318: ...Analogue Extension Module 318 ...
Page 332: ...Additional data actual signals and parameters 332 ...
Page 334: ...DriveWindow 334 ...
Page 335: ...Control block diagrams 335 Control block diagrams ...
Page 336: ...Control block diagrams 336 ...
Page 337: ...Control block diagrams 337 ...
Page 338: ...Control block diagrams 338 ...
Page 340: ...www abb com drives www abb com drivespartners Contact us 3AFE68775230 Rev E EN 2012 09 25 ...