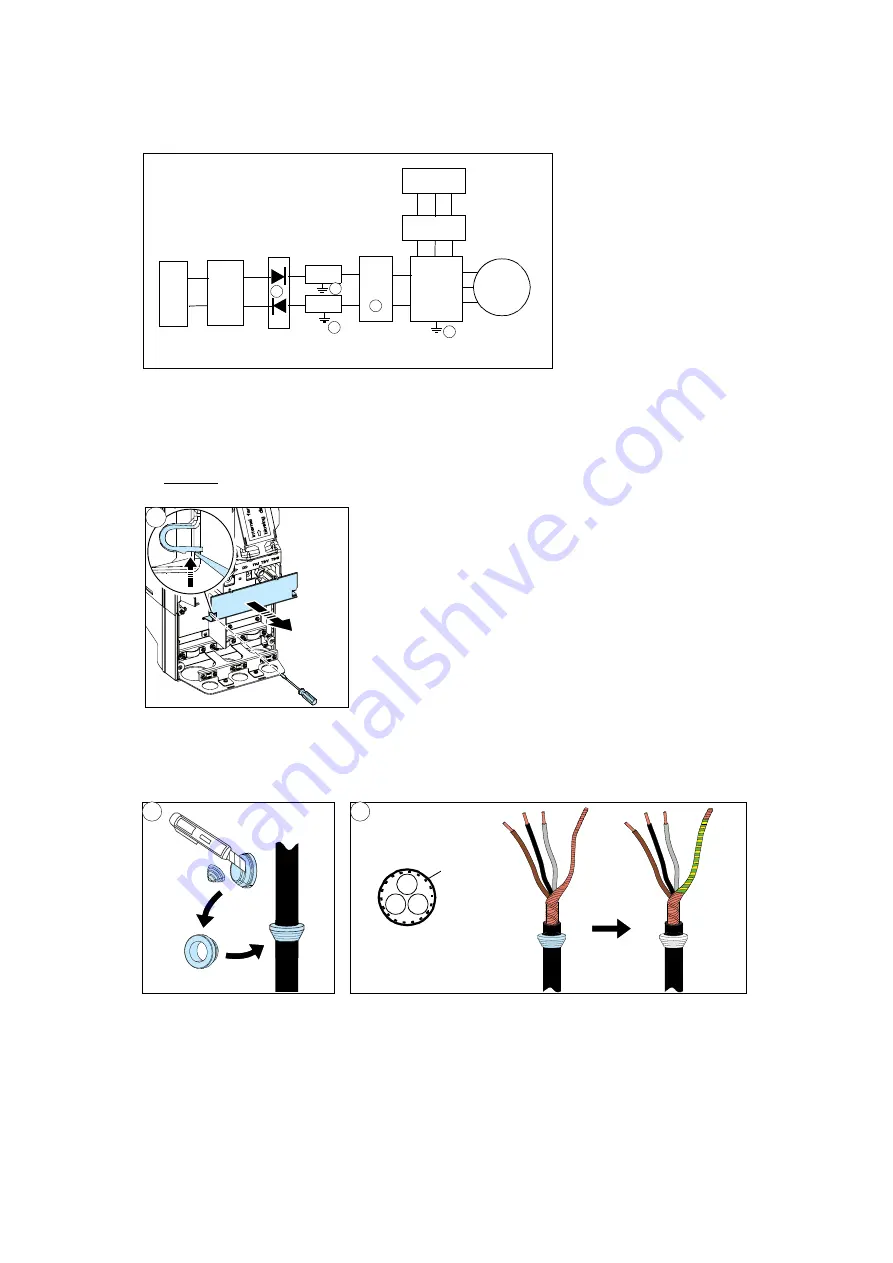
5
If you do wiring in conduits, see the drive hardware manual for more information.
1.
Reverse polarity diodes.
2.
EMI filter is optional but is mandatory for IEC/EN62920 standard compliance which is required in Europe.
3. Ground connection should be common for MOV, drive, and pump.
Note:
ACQ80-01 drive is intended to be used for speed control of 3-phase AC pump motors and is powered from either AC
Grid or DC photo-voltaic array. ABB recommends not to use it as an island grid forming inverter or to supply generic single
phase or 3-phase loads, other than the 3-phase AC pump motors.
Connection procedure
1.
Frames R5: Remove the shroud(s) on the power cable terminals.
2.
Prepare the power cables:
•
Remove the rubber grommets from the cable entry.
•
Cut a sufficient hole in the rubber grommet. Slide the grommet onto the cable (a).
•
Prepare the ends of the input power cable and motor cable as illustrated in the figure (b).
•
Slide the cables through the holes in the cable entry and attach the grommets to the holes.
•
If you use aluminum cables, apply grease to the stripped conductors before you connect them to the drive.
P
V
in
p
u
t
te
rm
in
a
l
DC/
MCB/
Fuse
MOV
EMI
filter
DC+
DC-
L1
L2 L3
U
V
W
PE
Pump
motor
AC MCB/
MPCB
AC grid or
generator
1
2
3
3
ACQ80-01
drive
3
Earth pit 1
MOV
Earth pit 1
Earth pit 1
R5
1
PE
2a
2b