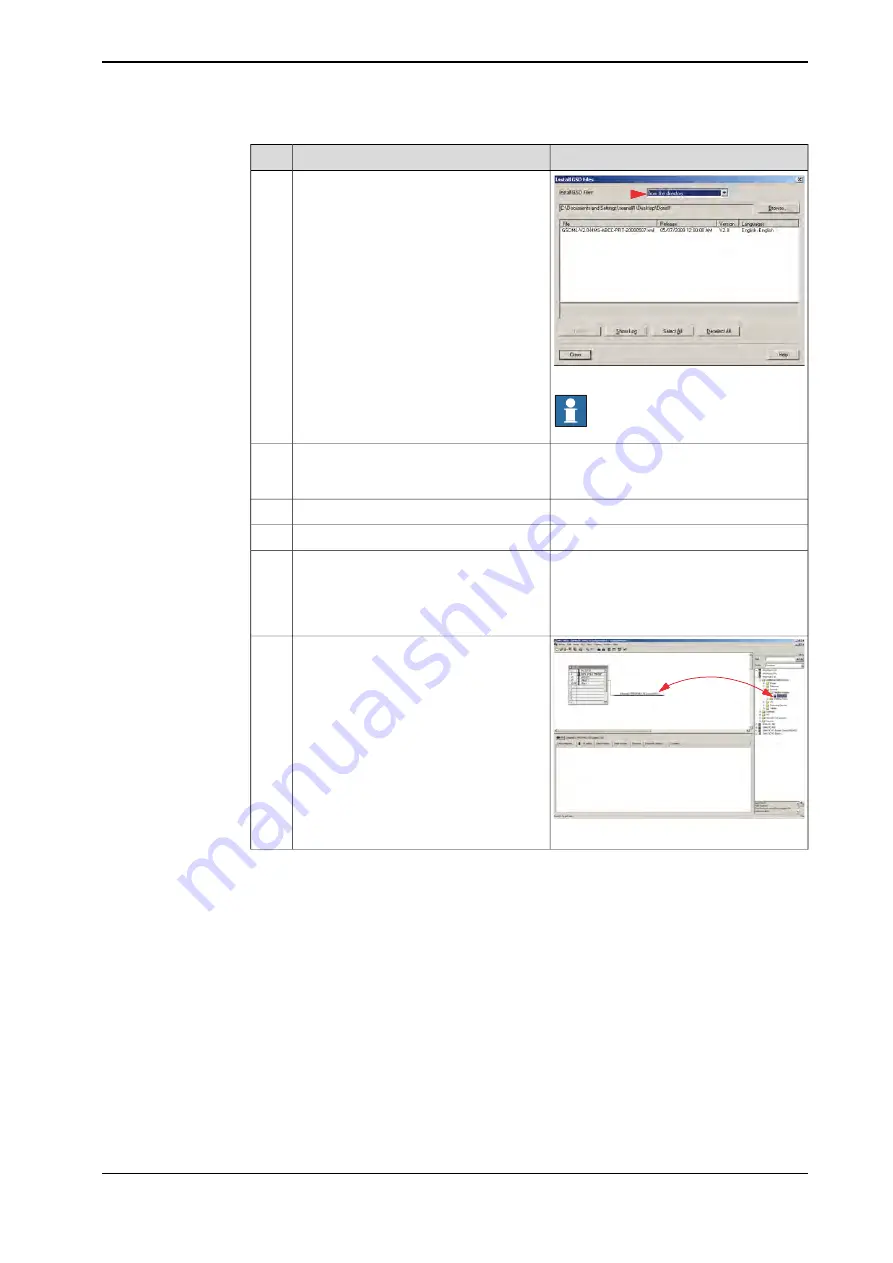
Note
Action
xx0800000190
In the
Install GSD Files
menu, select
from
the directory
and click
Browse
.
9
Note
Select the GSDML file from the Robot-
Ware DVD and click
Install
. Click
Yes
to
confirm the warning.
10
Click
OK
to complete the installation.
11
Click
Close
.
12
In the device list on the right-hand side of
the HW Config, expand
PROFINET
IO\Additional Field Devices\Gener-
al\Fieldbus Adapter
and select
DSQC
688
.
13
xx0800000193
Drag the DSQC 688 device to the industri-
al network.
14
Continues on next page
Application manual - PROFINET Anybus Device
31
3HAC050968-001 Revision: C
© Copyright 2008-2016 ABB. All rights reserved.
4 Configuring the anybus device
4.4.1 Configuring an external controller using Siemens Step7 PC tool
Continued
Summary of Contents for 3HAC031670-001
Page 1: ...Application manual PROFINET Anybus Device ...
Page 6: ...This page is intentionally left blank ...
Page 14: ...This page is intentionally left blank ...
Page 18: ...This page is intentionally left blank ...
Page 22: ...This page is intentionally left blank ...
Page 34: ...This page is intentionally left blank ...
Page 42: ...This page is intentionally left blank ...
Page 44: ......
Page 45: ......